Mechanical Insulation Design Guide
Materials and Systems
- Categories of Insulation Materials
- Insulation Forms
- Physical Properties of Insulation Materials
- Product Characteristics of Thermal Insulation Materials
- Cellular Insulations
- Granular Insulations
- Reflective Insulations
- Categories of Weather Barriers, Vapor Retarders, and Finishes
- Physical Properties of Weather Barriers, Vapor Retarders, and Finishes
- Product Characteristics of Weather Barriers, Vapor Retarders, and Finishes
- Fabrications of Insulation Products
- Accessory Products
- Glossary of Terms
- Example Bills of Materials
- Insulation Textiles
There are a wide variety of insulation materials, facings, and accessory products available for use on mechanical systems. The list changes continuously as existing products are modified, new products are developed, and some products are phased out. The task for the insulation system designer is to select the products or combination of products that will satisfy the design requirements at the lowest total cost over the life of the project. Cost is not always the deciding factor, however, as insulation systems provide needed personnel protection, save energy, mitigate environmental impacts and development of corrosion under insulation (CUI), enhance the longevity of energy equipment, and help meet return on investment goals. The design task is not easy. In most cases, the designer will find that a number of products or systems will work, and the final choice will depend on cost, availability, compatibility, ambient environmental conditions within operating areas, or other considerations.
This section reviews commonly used materials and describes important performance properties. Links to data sheets for commercially available products also are provided. It is important to continually check for changes to existing products, as well as the availability of new products, that may enhance successful use and efficiency of a well-designed insulation envelope. Within the Resource Section you can find listings of mechanical insulation standards and guidelines, along with Manufacturers—Associate Members of the National Insulation Association (NIA), categorized in the same format as materials contained in this section.
Categories of Insulation Materials
Insulation materials may be categorized (Turner and Malloy, 1981) into one of five major types: 1) cellular, 2) fibrous, 3) flake, 4) granular, and 5) reflective.
Cellular insulations are composed of small individual cells either interconnected with or sealed from each other to form a cellular structure. The base material may be composed of glass, plastics, and rubber, and a variety of foaming agents are used.
Cellular insulations are often further classified as either open cell (i.e., the cells are interconnecting) or closed cell (the cells sealed are from each other). Generally, materials that have greater than 90% closed-cell content are considered to be closed-cell materials.
Fibrous insulations are composed of small-diameter fibers that finely divide the air space. The fibers may be organic or inorganic, and they are normally (but not always) held together by a binder. Typical inorganic fibers include glass, rock wool, slag wool, and alumina silica.
Fibrous insulations are further classified as either wool or fiber insulations. Textile-fiber insulations are composed of woven and non-woven fibers and yarns. The fibers and yarns may be organic or inorganic. These materials are sometimes supplied with coatings or as composites for specific properties—e.g., weather and chemical resistance, reflectivity, etc.
Flake insulations are composed of small particles or flakes that finely divide the air space. These flakes may or may not be bonded together. Vermiculite, or expanded mica, is flake insulation.
Granular insulations are composed of small nodules that contain voids or hollow spaces. These materials are sometimes considered open-cell materials because gases can be transferred between the individual spaces. Aerogel, calcium silicate, microporous, and expanded perlite insulations are considered granular insulation. It has two subcategories: Flexible and Rigid, defined below.
Granular, Flexible insulation can be bent (flexed) without loss of strength or integrity. It can be supplied flat or in rolls, with or without facings. Aerogel and microporous are produced in flexible types. Flexible granular usually includes a carrier or a facing to contain or support the granular material during use.
Granular, Rigid insulation opposes any tendency to bend (flex) under load and may lose strength or integrity when bent. It can be supplied as blocks or in a preformed pipe configuration. Calcium silicate, microporous, and expanded perlite are produced in rigid types.
Reflective Insulations and treatments are added to surfaces to lower the long-wave emittance, thereby reducing the radiant heat transfer to or from the surface. Some reflective insulation systems consist of multiple parallel thin sheets or foil spaced to minimize convective heat transfer. Low-emittance jackets and facings are often used in combination with other insulation materials.
Another material, sometimes referred to as thermal insulating coatings or paints, is available for use on pipes, ducts, and tanks. These paints have not been extensively tested, and additional research is needed to verify their performance. While these materials are in some cases marketed as “thermal insulation,” it is important to remember that they are a liquid coating or paint. They are normally applied by spraying, which dries or cures, depending on the formulation, to create a protective finish of a specified mil thickness. From NIA’s perspective, it is a coating or paint, and its role as such will be left to the coating or paint experts. Thus, it is not included in the scope of this guide.
From an insulation perspective, thermal insulation coatings are primary used for personnel protection purposes. According to ASTM C1055, the maximum allowable surface temperature for metallic objects is 140°F.
“The possibility of burn occurring depends on three primary factors: surface temperature, thermal properties of the hot surface, and contact time of the skin to the surface… Depending on the type of material of the hot object, the skin temperature can be close to or significantly cooler, after the 5-second contact time, than the temperature of the hot surface. For metal objects (which typically have high thermal conductivities), the heat transfer is rapid and will the heat the skin to within a few degrees of the temperature of the metal surface within the 5-second rule.”
– From “Determination of Skin Burn Temperature Limits for Insulative Coatings Used for Personnel Protection,” NACE Accepted Paper by Howard Mitschke, Mitschke Coating Consulting, LLC and George More, Mascoat.
Both thermal insulation coatings and traditional insulation systems are used for personnel protection, based on many considerations and environmental conditions.
Temperature Range
Insulation materials or systems also may be categorized by service temperature range.
Opinions vary over the classification of mechanical insulation by the service temperature range for which the insulation is used. As an example, the word “cryogenics” means "the production of freezing cold." However, the term is used widely as a synonym for many low-temperature applications. At what point on the temperature scale refrigeration ends and cryogenics begins is not well defined. The National Institute of Standards and Technology (NIST) in Boulder, Colorado considers the field of cryogenics to involve temperatures below -180°C. NIST based its determination on the understanding that the normal boiling points of “permanent” gases such as helium, hydrogen, nitrogen, oxygen, and normal air are below -180°C, while the Freon refrigerants, hydrogen sulfide, and other common refrigerants have boiling points above -180°C.
Understanding that there is variance in the accepted ranges of service temperature by which to classify mechanical insulation, the mechanical insulation industry has generally adopted the following category definitions:
Category | Definition |
---|---|
Cryogenic applications | -50°F and below |
Thermal applications: Refrigeration, chilled water, and below-ambient applications Low to high-temperature applications |
-49°F to +1,200°F |
Refractory Applications | +1,200°F and above |
Insulation Forms
Several terms are used to define the shape, consistency, or flexibility of insulation products. Often, these product definitions are not mentioned in project specifications, but they are commonly used in the industry.
- Sectional Pipe Coverings
- Hinged and Half Sections
- Quads or Pipe Section Quarters (PSQ)
- V-Groove Pipe Covering
- Slip on
- Wrap-Around Single or Multiple Layers
- Additional Pipe Covering and Equipment Insulation Forms
- Mitered, Routed, Stovepipe, and Contoured Fittings
- Scored Insulation Block
- V-Groove Insulation Block
- Curved Radius Block (CRB) or Curved Segments and Beveled Lags
- Flat Block and Lags
- Blanket
- Sheet and Board
- Flexible-Faced Fiber
- Insulation Material Form Definitions
- Engineered Head Segment
- Pipe and Tank Wrap
- Board
- Blanket or Sheet
Physical Properties of Insulation Materials
Selecting an insulation material for a particular application requires an understanding of the physical properties associated with the various materials available.
Use Temperature is often the primary consideration in the selection of an insulating material for a specific application. Maximum temperature capability is normally assessed using ASTM C411 or C447. The test methods involve exposing samples to hot surfaces for an extended time and subsequently assessing the materials for any changes in properties. ASTM C411 is specified when exposing the insulation material to an ambient-temperature surface and then utilizing a specified heat-up cycle. ASTM C447 requires the insulation material be installed on a surface that has been preheated to the maximum operating temperature. Evidence of warping, cracking, delamination, flaming, melting, or dripping indicates that the maximum use temperature of the material has been exceeded. There is currently no industry-accepted test method for determining the minimum use temperature of an insulation material, but minimum temperatures are normally determined by evaluating the integrity and physical properties of the material after exposure to low temperatures.
Thermal Conductivity is defined in ASTM C168 as the time rate of steady-state heat flow through a unit area of a homogeneous material induced by a unit temperature gradient in a direction perpendicular to that unit area. The term “apparent thermal conductivity” is used to indicate that additional non-conductive modes of heat transfer (e.g., radiation or free convection) may be present for many insulation materials.
In the insulation industry, thermal conductivity is typically expressed as the symbol k, in units of Btu·in/(h ft² °F), or λ, in units of W/(m·°C).
The apparent thermal conductivity of insulation materials is a function of temperature. Many specifications call for insulation conductivity values evaluated at a mean temperature of 75°F. Most manufacturers provide conductivity data over a range of temperatures to allow evaluations closer to actual operating conditions. Conductivity of flat insulation products is measured per ASTM Test Method C177 or C518, while the conductivity of pipe insulation is generally determined using ASTM Test Method C335. At present, ASTM does not provide a consensus test procedure for pipe insulation at below-ambient temperatures (i.e., heat flow in). Conductivity data for below-ambient applications is therefore obtained either by extrapolation from above-ambient tests or via tests on flat material. Note that in some cases, tests on flat materials have yielded lower conductivity values than tests on equivalent cylindrical materials.
Additional terms related to thermal conductivity are sometimes used (see the Glossary). These are not material properties but are used to describe the thermal performance of specific products or systems.
Thermal Conductance, or C-value, is the time rate of steady-state heat flow through a unit area of a material or construction induced by a unit temperature difference between the body surfaces. On a flat board or blanket insulation, C is calculated as the thermal conductivity divided by the thickness (C=k/t).
Thermal Resistance, or R-value, is the quantity determined by the temperature difference, at steady state, between two defined surfaces of a material or construction that induces a unit heat flow rate through a unit area. For a flat board or blanket insulation, R is calculated as the thickness divided by the thermal conductivity (R=t/k). Thermal resistance is the inverse of thermal conductance.
Thermal Transmittance, or U-factor, is the heat transmission rate through unit area of a material or construction and the boundary air films induced by a unit temperature difference between the environments on each side. Units of U are typically Btu/(h·ft²·°F)
Density is the mass per unit volume of a material. For insulation we are normally concerned with the "bulk" or the "apparent" density of a product. Bulk density is the mass of the product divided by the overall volume occupied and is an average of the densities of the individual materials making up the product. Density is denoted by the symbol ρ and expressed in units of lb./ft³ or kg/m³. Historically, density was used as a proxy for other properties of insulation (e.g., compressive resistance) and is still found in various insulation specifications. It is useful in the design of support/hanger systems where the overall weight of the system must be considered. It also becomes important in transient heat flow situations.
Specific Heat is the amount of thermal energy required to raise the temperature of a unit mass of a material by 1°. Normally expressed in units of Btu/lb.·°F or kJ/kg·°K.
Thermal Diffusivity is the ratio of the conductivity of a material to the product of its density and specific heat. It is an important property in transient situations. Generally, the lower the diffusivity, the more "thermal flywheel" in the system. Units are ft²/h or m²/s.
Alkalinity or pH describes the tendency of a material to have either a basic or acidic reaction. For insulation materials, it is measured on an extract of the material in distilled water. Results are reported on the pH scale, with readings above 7.0 indicating alkaline and below 7.0 indicating acidic.
Compressive Resistance is defined as the compressive load per unit of area at a specified deformation. When the specified deformation is the start of complete failure, the property is called “compressive strength,” which is measured in lb./in² or lb./ft² and is important when the insulation material must support a load without crushing (e.g., insulation inserts used in pipe hangers and supports). When insulation is used in an expansion or contraction joint to take up a dimensional change, lower values of compressive resistance are desirable. ASTM Test Method C165 is used to measure compressive resistance for fibrous materials, and ASTM Test Method D1621 is used for foam plastic materials.
Flexural Resistance of a block or board insulation product is the ability to resist bending. It is determined by ASTM C203 and is measured in lbs./in² or lbs./ft². The related term “flexural strength” refers to the flexural resistance at breaking.
Linear Shrinkage is a measure of the dimensional change that occurs in an insulation material under conditions of soaking heat. Most insulation materials will begin to shrink at some definite temperature. Usually, the amount of shrinkage increases as the exposure temperature rises. Eventually, a temperature will be reached at which the shrinkage becomes excessive and the material has exceeded its useful temperature limit. Linear shrinkage is determined by ASTM C356, which specifies soaking heat for a period of 24 hours.
Water Vapor Permeability is defined as the time rate of water vapor transmission through unit area of flat material of unit thickness induced by unit vapor-pressure difference between two specific surfaces under specified temperature and humidity conditions. For insulating materials, water vapor permeability is commonly expressed in units of perm-in. A related (and often confused) term is “water vapor permeance,” which describes the water vapor flux through a material of a specified thickness. Water vapor permeance is expressed in perms and is generally used to define the performance of a vapor retarder. In below-ambient applications, it is important to minimize the rate of water vapor flow to the cold surface. This is normally accomplished by using vapor retarders with low permeance, insulation materials with low permeability, or both. ASTM Test Method E96 is used to measure the water vapor transmission properties of insulation materials.
Water Absorption is generally measured by immersing a sample of material under water for a specified time period. It is a useful measure when considering the amount of liquid water that may be absorbed due to water leaks in weather barriers or during construction. Water absorption is measured by a number of different immersion methods (ASTM C209, ASTM C240, ASTM C272, ASTM C1763, and ASTM C610). These methods differ in length of immersion time (from 10 minutes to 48 hours), in the reported units (% by weight or % by volume), and in the requirements for both preconditioning (i.e., heat aging) and post-conditioning (specimen draining and pat-off). These differences make direct comparison of water absorption data difficult.
Water Vapor Sorption is a measure of the amount of water vapor sorbed (either by absorption or adsorption) by an insulation material under high-humidity conditions. The test procedure (ASTM C1104) involves drying a sample to constant weight and then exposing it to a high-humidity atmosphere (120°F, 95% relative humidity [RH]) for 96 hours.
Wicking is the infiltration of a wetting liquid into a material by capillary action. For insulation materials, wicking of liquid water is undesirable because it can degrade the properties of the insulation. Wicking is measured by ASTM C1559, which involves inserting insulation samples in a pan of liquid water and measuring the capillary rise after a 1-week period.
Table 1: Performance Property Guide for Insulation Materials
Typical physical properties of interest are given in Table 1. Values in this table are generally taken from the relevant ASTM material specification. Within each material category, a variety in types and grades of materials exist. A representative type and grade are listed in Table 1 for each material category, but users are referred to the ASTM Material Standards or to manufacturers for specific data.
This tool provides the reader with physical properties as specified in ASTM material specifications and is a guide to material properties, but may not be sufficient for writing specifications.
Enter the operating temperature in F° below.
Product Characteristics of Thermal Insulation Materials
The following section describes the commonly available materials used as insulation on mechanical systems. The information is primarily drawn from the appropriate ASTM material specification. These material specifications are the responsibility of ASTM Committee C16 on Thermal Insulation and are published in the Annual Book of ASTM Standards, Volume 04.06, available in book or CD format from ASTM International. Individual standards in downloadable PDF format are also available.
Note that these ASTM standard specifications are industry-consensus standards. Compliance with the requirements of these industry standards is voluntary. Standards become legally binding only when a government body references them in regulations, or when they are cited in a specification that is part of a contract. Manufacturers who claim compliance with these standards are required to have appropriate documentation supporting their claim.
Also note that the property requirements of these standards are generally stated as minimums or maximums. Most insulation manufacturers will claim to "meet or exceed" these requirements. In some cases, the performance of specific products may significantly exceed the minimum or maximum requirements. Check the manufacturer's specific product data sheets for specific product performance.
A brief discussion of imported insulation materials is appropriate. Ever since two catastrophic fiber glass manufacturing facility fires occurred in 2003, import and use of materials manufactured outside the United States have been more acceptable to North American industry participants. The end user, in many cases, does not place primary importance on where a product is made as long as the product meets the specifications. Therein lies an important question: Does the foreign-manufactured material meet the applicable ASTM material specification? It may look and feel the same, and be sold in a similar wrapper, but have its composition, health and safety attributes, quality, and performance standards been measured on the same basis as materials manufactured domestically?
This is not suggesting that materials manufactured overseas are somehow inferior to those manufactured in North America. It is simply raising a caution flag for individuals and companies considering the use of imported materials. Have they been tested and their performance measured on the same basis as those made in North America? The burden of proof and ownership of the material ultimately lies with the end user, but all participants involved in the decision-making process will shoulder some degree of responsibility if a failure were to occur. A failure of any magnitude, regardless of the cause, is detrimental to the industry. Assumption of equivalence and warranty support could be costly.
Cellular Insulations
Elastomeric
Elastomeric insulations are defined by ASTM C 534, Type I (preformed tubes) and Type II (sheets). There are three grades in the ASTM standard which are widely available.
Grade | Basic description | Temperature Limits | Flame Spread Index/Smoke Developed Index |
---|---|---|---|
1 | Widely used on typical commercial systems | -297°F to 220°F | 25/50 through 1–½" thickness. |
2 | High temperature uses | -297°F to 350°F | Not 25/50 Rated |
3 | Use on stainless steel applications above 125 °F | -297°F to 250°F | Not 25/50 Rated |
Elastomeric Insulation Products
All three grades are flexible and resilient closed-cell expanded foam insulation made of butyl rubber, flame retardants, and plasticizers. The maximum water vapor permeability is 0.10 perm-inch for Grade 1 and 0.30 perm-inch for Grades 2 and 3. The maximum thermal conductivity at 75°F is 0.28 Btu·in/(h·ft²·°F) for Grades 1 and 3, and 0.30 Btu·in/(h·ft²·°F) for Grade 2. Grade 3 formulation contains low levels of any leachable chlorides and fluorides.
The preformed tubular insulation is available in inner diameter (ID) sizes from 3/8" to 10 iron pipe size (IPS), in wall thickness from 3/8" to 2", and in typical lengths of 6 feet or continuous coil. The tubular product is available with and without pre-applied adhesive. The sheet insulation is available in continuous lengths of 4′ widths or in 3' by 4′ sections, and in wall thicknesses from 1/4" to 2". The sheet product is available both with and without pre-applied adhesive.
For outdoor applications, a weatherable jacket or coating must be applied to protect against UV rays and ozone.
These materials are normally installed without additional vapor retarders, but additional vapor-retarder protection may be necessary when installed on very-low-temperature piping or where continually exposed to high-humidity conditions. All seams and termination points must be sealed with manufacturer-recommended contact adhesive. For outdoor applications, a weatherable jacket or manufacturer-recommended coating must be applied to protect against UV rays and ozone.
Cellular Glass
Cellular glass insulation is a rigid, inorganic, non-combustible, impermeable, chemically resistant form of glass. It is available jacketed or unjacketed. Cellular glass is defined by ASTM as insulation composed of glass processed to form a rigid foam, having a predominantly closed-cell structure. For mechanical insulation applications, cellular glass is covered by ASTM C552, Standard Specification for Cellular Glass Thermal Insulation, and is intended for use on surfaces operating at temperatures between -450°F and 800°F. The standard defines three types, as follows.
Cellular Glass Insulation Products
Type | Form and Grades Available |
---|---|
I | Flat Block |
II | Pipe and Tubing, Fabricated |
III | Special Fabricated Shapes |
Cellular glass is produced in block form (Type I). Blocks of Type I product are typically shipped to fabricators who produce fabricated shapes (Types II and III) that are supplied to distributors and/or insulation contractors. Cellular glass insulation within Types I, II, and III are also offered in a range of grades. Grade 6 is the most common grade for mechanical insulation applications. The standard also contains requirements for compressive strength, flexural strength, water absorption, water-vapor permeability, thermal conductivity, hot surface performance, and surface burning characteristics.
Fabrication techniques for cellular glass block to produce pipe and tubing insulation is specified in ASTM C1639, Standard Specification for Fabrication of Cellular Glass Pipe and Tubing Insulation. Typically, fabrication of cellular glass insulation involves adhering multiple blocks together to form a "billet," which is then used to produce pipe insulation or special shapes. The adhesives used vary with the intended end use and design operating temperatures. Bond joint and fabrication adhesive for below-ambient temperatures ≥ -297°F (-183°C) should be hot asphalt, Specification D312, Type II, III, or IV, or a manufacturer-approved, low-permeability alternative. For operating temperatures above ambient temperature, or where organic adhesives could pose a problem (e.g., LOX service), inorganic adhesives such as gypsum-based cement of the type and grade specified by the cellular glass insulation manufacturer should be used.
Polystyrene
Extruded Polystyrene Foam (XPS) Insulation Products
Polystyrene thermal insulation is rigid, cellular foam insulation. It is commonly classified as either Expanded Polystyrene Foam (EPS) or Extruded Polystyrene Foam (XPS). XPS is a closed cell material manufactured as rectangular billets in various sizes. Prior to actual installation, billets are fabricated into various shapes including preformed pipe half-shells 3 ft long designed to fit NPS pipe and tubing. Complex shapes can also be fabricated to fit valves, fittings, and other equipment. ASTM material specification C 578 covers several types of polystyrene insulation, but Types IV or XIII are usually specified for mechanical applications. The standard contains requirements for compressive resistance, flexural strength, thermal conductivity, water absorption, water vapor permeability, and dimensional stability. For comparison purposes, the maximum thermal conductivity of the Type IV XPS is 0.20 Btu-in/hr-ft2-F while Type XIII XPS has a maximum of 0.26 Btu-in/hr-ft²-°F at 75°F.
Key applications for XPS insulation are on pipe, equipment, tanks, and ducts operating at temperatures below ambient. These include food and beverage lines, and refrigeration lines.
Polyisocyanurate
Polyisocyanurate Insulation Products
Polyisocyanurate thermal insulation (PIR) is rigid foam insulation with a closed cell structure. It is usually manufactured as large rectangular buns typically 4 ft wide x 3-24 ft long x 1-2 ft tall and in a range of densities and compressive strengths. Prior to actual installation, buns are fabricated into various shapes including flat boards and preformed pipe half-shells 3-4 ft long designed to fit NPS pipe and tubing. Complex shapes can also be fabricated to fit around valves, fittings, and other equipment. ASTM material specification C 591 covers PIR at service temperatures from -297°F to +300°F ASTM C 591 contains requirements for density, compressive resistance, thermal conductivity, water absorption, water vapor permeability, dimensional stability, closed cell content, and hot-surface performance. This ASTM specification lists two grades and six types with the types identifying the various densities as noted below. The most commonly used densities are in the 2-2.5 lb/ft³ range (types IV and II). For comparison purposes, the thermal conductivity of the Grade 2, Types IV and II PIR is a maximum of 0.20 Btu·in/(hr·ft²·°F) at 75°F.
Type | Minimum Density (lbs/ft³) | Minimum Compressive Resistance (lbs/in²) |
---|---|---|
I | 1.8 | 20 |
IV | 2.0 | 22 |
II | 2.5 | 35 |
III | 3.0 | 45 |
V | 4.0 | 80 |
VI | 6.0 | 125 |
The two Grades, 1 and 2, identify PIR designed for different temperature ranges. Grade 1 has a temperature range of -70°F to +300°F while Grade 2 has a temperature range of -297°F to +300°F.
Key applications for PIR insulation are on pipe, equipment, tanks, and ducts operating at temperatures below ambient. Examples include commercial chilled water, refrigeration, and liquefied natural gas lines. It is also used as the core material in the manufacture of foam core panels for various applications including transportation, building construction, and temporary shelters.
Polyurethane
Polyurethane insulation, commonly called PUR, is a closed-cell foam insulation material. It is typically either spray-applied or poured-in-place. Spray applied polyurethane Foam (SPF) requires specialized equipment to apply the material and proper technical training is important in order to get the best results. SPF is used in a wide variety of applications including industrial applications like pipes, tanks, cold storage facilities, freezers, and walk-in coolers.
ASTM C 1029 Standard Specification for Spray-applied Rigid Cellular Polyurethane Thermal Insulation covers the types and physical properties for use as thermal insulation between -22°F and 225°F. The standard classifies materials into four types by compressive strength as follows:
Type | Compressive Strength, psi |
---|---|
I | 15 |
II | 25 |
III | 40 |
IV | 60 |
The standard covers requirements for thermal resistance of 1.0 inch thickness, compressive strength, water vapor permeability, water absorption, tensile strength, response to thermal and humid aging, and closed cell content. For comparison purposes, the max thermal conductivity for all types is 0.16 Btu-in/(h ft²°F)
ASTM C 945 Standard Practice for Design Considerations and Spray Application of a Rigid Cellular Polyurethane Insulation System on Outdoor Service Vessels covers substrate preparation, priming, selection of the polyurethane system, and the selection of the protective covering for outdoor service. The Spray Polyurethane Foam Alliance (www.sprayfoam.org) is a trade organization of SPF producers and contractors who can provide additional assistance on SPF.
Polyurethane foam is also available as one or two component poured-in-place systems in disposable containers.
Phenolic
Phenolic Insulation Products
Phenolic insulation is rigid foam insulation with a closed-cell structure. It is manufactured as large rectangular buns typically 4 ft wide x 3-12 ft long x 1-2 ft tall at a density of 2 lbs/ft³. Prior to actual installation, buns are fabricated into various shapes including flat boards and preformed pipe half-shells 3 ft long and designed to fit over NPS pipe and tubing. More complex shapes can also be fabricated to fit around fittings, elbows, and other equipment. ASTM material specification C 1126, Type III, Grade 1 covers this type of insulation at service temperatures from -290°F to +257°F. The specification defines requirements for density, compressive resistance, thermal conductivity, water absorption, water vapor permeability, and dimensional stability. While this ASTM spec lists two grades and three types, only the Type III, Grade 1 is appropriate for use in pipe insulation. The other types are boards either faced with a vapor retarder or not and used for building sheathing and roofing, respectively. Grade 2 is an open cell product. For comparison purposes, the maximum thermal conductivities at 75°F for the Type III, Grade 1 phenolic insulation is 0.13 Btu-in/hr-ft²-°F.
Key applications for this phenolic insulation are on pipe, equipment, tanks, and ducts, especially those operating at temperatures below ambient.
Melamine
Flat Melamine Insulation
Melamine Pipe Insulation
Melamine insulation is a low density, semi-rigid, open-cell foam intended for use as thermal and sound absorbing insulation at temperatures between -40°F and +350°F. ASTM C 1410 covers this material and defines the following insulation types and grades:
Type I - flat slab
Grade 1 - Regular (core foam with no facing)
Grade 2 - Faced foam
Type II - pipe and tubing insulation
Grade 1 - Regular (core foam with no facing)
Grade 2 - Faced foam
Type III - special shapes
The specification defines requirements for oxygen index, optical smoke density, surface burning characteristics, density, tensile strength, % elongation, indentation force deflection, thermal conductivity, water vapor sorption, linear shrinkage, and smoke toxicity.
For comparison purposes, the maximum thermal conductivity at 75 F mean temperature is 0.30 Btu-in / h·ft²·F
Melamine insulations find application to a variety of industrial and process applications, including pharmaceutical, food-grade, and clean room applications. The product is available unfaced or with a number of different factory-applied jacketing systems.
Polyethylene/Polyolefin
Polyethylene and Polyolefin Insulation Products
Polyethylene/Polyolefin insulations are defined by ASTM C 1427. Type I (preformed tubes) and Type II (sheets). Note: the designations polyolefin and polyethylene refer to the same type of material and are considered synonymous.
Polyethylene/polyolefin are flexible, closed cell insulation products. The maximum water permeability values are 0.05 perm-inch and the maximum thermal conductivity is 0.35 BTU-in/hr sq ft°F at a mean temperature of 75°F.
The preformed tubular insulation is available in ID size range from 3/8" to 4 IPS and in wall thicknesses from 3/8" to 1". The tubular product is available with and without pre-applied adhesive. They are suitable for domestic plumbing applications where the maximum temperature is below 200°F. The polyethylene/polyolefin insulations are formulated to meet the flame spread index of less than 25 and smoke developed index of less than 50.
These materials are generally applied without additional vapor retarder facings. All seams including termination points must be sealed with manufacturer recommended contact adhesive. For outdoor applications a weatherable jacket must be applied to protect against UV and ozone.
Polyimide
Polyimide (PI) insulation is defined by ASTM as lightweight, flexible, open-cell foam for use as thermal and sound-absorbing insulation in commercial and industrial environments. PI is manufactured as large rectangular buns, typically 4 ft wide x 8 ft long x 5-30 inches tall, in a range of densities. Prior to actual installation, buns are fabricated into various shapes, including flat sheets and preformed pipe half-shells designed to fit over NPS pipe and tubing. Complex shapes can also be fabricated to fit tightly around fittings, elbows, and other equipment. ASTM material specification C 1482 covers PI insulation at service temperatures from -328°F to +572°F.
ASTM C 1482 defines the requirements for density, thermal conductivity, acoustic absorption, thermal stability, flammability, smoke density, smoke toxicity, chemical resistance, corrosiveness, and mechanical properties. This ASTM spec lists two grades and four types of PI foam, but the following three types are most commonly used for commercial and industrial applications.
Type | Maximum Density (lbs/ft³) | Maximum Thermal Conductivity at 75°F (Btu-in/hr-ft²-°F) |
Upper Temperature Limit |
---|---|---|---|
I, Grade 1 | 0.48 | 0.32 | 400°F |
IV | 0.37 | 0.34 | 400°F |
VI | 0.50 | 0.34 | 572°F |
Key applications for PI foam include thermal and acoustic insulation for HVAC and industrial equipment, acoustic duct liner, high temperature pipe insulation, and expansion joints for cryogenic facilities.
The use of an appropriate vapor retarder is required in all applications where condensation could occur. There are a wide variety of vapor retarders, both films and coatings, that can be specifie
Fibrous Insulations
Fiberglass Board and Blanket Insulation Products
Fiberglass Pipe Insulation Product
Fibrous insulations are composed of small diameter fibers that finely divide the air space. The fibers may be organic or inorganic and they are normally (but not always) held together by a binder. Typical inorganic fibers include glass, rock wool, slag wool, and alumina silica.
Mineral Fiber (Fiberglass and Mineral Wool)
Mineral Fiber insulations are defined by ASTM as insulations composed principally of fibers manufactured from rock, slag, or glass, with or without binders. Fiberglass and Mineral Wool products fall in this category. There is some confusion concerning the nomenclature used for these materials. Fiberglass products (sometimes called "fibrous glass" or "glass wool") and mineral wool products (sometimes called "rock wool" or "slag wool") are covered by the same ASTM "Mineral Fiber" specifications, and sometimes by the same type and grade. Specifiers are cautioned to call out both the specific material and the ASTM Type and Grade when specifying these products. For example "Fiberglass pipe insulation meeting the requirements of ASTM C 547 Type I, Grade A" or "Mineral Wool pipe insulation meeting the requirements of ASTM C 547 Type II, Grade A".
A number of ASTM material standards cover mineral fiber products.
Mineral Fiber Pipe
Mineral Fiber Pipe insulation is covered in ASTM C 547. The standard contains five types classified primarily by maximum use temperature.
Mineral Fiber Pipe Insulation Products
Type | Form | Maximum Use Temp, F |
---|---|---|
I | Molded | 850 F |
II | Molded | 1200 F |
III | Precision V-groove | 1200 F |
IV | Molded | 1000 F |
V | Molded | 1400 F |
The standard further classifies products by grade. Grade A products may be "slapped-on" at the maximum use temperature indicated, while Grade B products are designed to be used with a heat-up schedule.
The specified maximum thermal conductivity for all types is 0.25 Btu·in/(hr·ft²·°F) at a mean temperature of 100°F.
The standard also contains requirements for sag resistance, linear shrinkage, water-vapor sorption, surface-burning characteristics, hot surface performance, and non-fibrous (shot) content. Further, there is an optional requirement in ASTM C 547 for stress corrosion performance if the product is to be used in contact with austenitic stainless steel piping.
Mineral Wool Insulation Products
Fiberglass pipe insulation products will generally fall into either Type I or Type IV. Mineral wool products will comply with the higher temperature requirements for Types II, III, and V.
These pipe insulation products may be specified with various factory-applied facings, or they may be jacketed in the field. Mineral fiber pipe insulations systems are also available with "self-drying" wicking material that wraps continuously around pipes, valves, and fittings. These products are intended to keep the insulation material dry for chilled water piping in high-humidity locations.
Mineral fiber pipe insulation sections are typically supplied in lengths of 36 inch, and are available for most standard pipe and tubing sizes. Available thicknesses range from ½" to 6".
Mineral Fiber Blanket
Mineral Fiber Blanket Insulation for Commercial and Industrial Applications is covered in ASTM C 553. The standard contains seven types classified by maximum use temperature and thermal conductivity.
Type | Maximum Use Temperature, °F |
Maximum k at 75°F, Btu-in./(h ft² °F) |
Maximum k at 300°F, Btu·in/(hr·ft²·°F) |
---|---|---|---|
I | 450 | 0.36 | 0.76 |
II | 450 | 0.31 | 0.60 |
III | 450 | 0.26 | 0.46 |
IV | 850 | 0.25 | 0.43 |
V | 1000 | 0.31 | 0.60 |
VI | 1000 | 0.26 | 0.46 |
VII | 1200 | 0.25 | 0.43 |
The standard also contains requirements for flexibility, water-vapor sorption, odor emission, surface-burning characteristics, corrosiveness, and shot content.
These insulations are flexible and are normally supplied as batts or rolled blankets. Dimensions vary but thicknesses from 1" to 6" are typically available. The products may be specified with various factory-applied facings, or may be ordered unfaced.
Mineral Fiber Block and Board
Mineral Fiber Block and Board insulation is covered in ASTM C 612. This standard contains five types classified by maximum use temperature and thermal conductivity.
Type | Maximum Use Temperature, °F |
Maximum k at 75°F, Btu·in/(hr·ft²·°F)) |
Maximum k at 300°F, Btu·in/(hr·ft²·°F)) |
---|---|---|---|
IA | 450 | 0.26 | 0.46 |
IB | 450 | 0.26 | 0.42 |
II | 850 | 0.25 | 0.44 |
III | 1000 | 0.25 | 0.44 |
IVA | 1200 | 0.25 | 0.44 |
IVB | 1200 | 0.24 | 0.36 |
V | 1800 | 0.45 | 0.49 |
Mineral Fiber Block and Board Insulation Products
Each of these types is further classified by compressive resistance. Category 1 materials have no requirement for compressive resistance, while Category 2 materials require a minimum compressive resistance value be met. Density is not a performance measure and has been removed as a requirement in ASTM C 612.
The standard also contains requirements for linear shrinkage, water-vapor sorption, surface-burning characteristics, odor emission, corrosiveness to steel, rigidity, and shot (non-fibrous) content. Further, there is an optional requirement in ASTM C 612 for stress corrosion performance if the product is to be used in contact with austenitic stainless steel.
Fibrous glass boards will generally meet Types I, II, or III. Mineral wool products will generally comply with the higher temperature requirements for Types IVA, IVB.
These products are supplied in rigid and semi-rigid board form. Dimensions will vary, but typical available thicknesses range from 1" to 4". The products may be specified with various factory-applied facings, or may be ordered unfaced.
Textile Glass
Textile Glass (E-glass) fibrous thermal insulation is produced from textile glass fibers (e-glass) and is needled into insulation felts without the use of binders. The material is used as thermal insulation component in the fabrication of insulation systems for use on machinery and equipment at temperatures up to 1200 F. These products are covered in ASTM C 1086 and in MIL-I-16411F.
The standard contains requirements for thickness, mass per unit area, apparent thermal conductivity, hot surface performance, tensile strength, and combustibility. For comparison purposes, the thermal conductivity of the material is a maximum of 0.29 Btu·in/(hr·ft²·°F) at 75°F.
High Temperature Fiber
High Temperature Fiber insulations are fibrous insulations, varying in flexibility, density, and composition, with or without binders. These insulation products are available in flat sheets, rolls, boards, or loose fibers. The insulation products are used as the thermal insulation component in the fabrication of insulation systems for use at temperatures up to 3,000°F.
This category of products is comprised of Refractory Ceramic Fibers (RCF), including a recently developed class generally referred to as Alkaline Earth Silicates (AES). These AES fibers are designed to be bio-soluble (i.e. they have enhanced in-vitro solubility characteristics which enable these products to meet European regulatory requirements (Directive 97/69/EC) for man-made vitreous fibers).
The RCF products in mat and blanket form are covered in ASTM C 892. Products are classified into five types (by maximum use temperature) and five grades (by density).
Type | Maximum Use Temp, °F |
---|---|
I | 1350 F |
II | 1600 F |
III | 2400 F |
IV | 2600 F |
V | 3000 F |
Grade | Density, nominal, pcf |
---|---|
3 | 3 |
4 | 4 |
6 | 6 |
8 | 8 |
12 | 12 |
The standard contains requirements for thermal conductivity, density, maximum use temperature, non-fibrous (shot) content, linear shrinkage, and tensile strength. For comparison purposes, the maximum thermal conductivity of Grade 3 material is 0.66 Btu·in/(hr·ft²·°F) at 400°F. It should be noted that not all manufacturers of high temperature fiber products utilize the ASTM C 892 standard for their products.
High temperature insulation products are often used as an alternative to fire resistance rated shaft enclosures. Applications include kitchen exhaust grease ducts, ventilation ducts, stairwell pressurization ducts, smoke extraction, chemical fume exhaust ducts, and refuse and trash chutes. They may be used to cover plastic pipe and cables to limit flame spread and smoke generation in fire rated air plenums. These insulation systems are listed and labeled by nationally recognized laboratories.
Pneumatically applied high temperature fibers are typically used on applications where it would be difficult to adhere blankets to a surface. These typically are internal surfaces such as furnace interiors or outer surfaces that are convoluted and / or difficult to access, such as boiler tube walls on a coal fired furnace. While they are yet covered by an industry specification, an ASTM specification is in development.
The composition can be described as follows: The basic types of materials are loose inorganic fibers (either RCF or AES) combined with a liquid, water based chemical binder. The fibers are made from mineral substances such as silica, alumina, calcium, and magnesium processed from the molten state into fibrous form. The liquid binder is made from inorganic materials: water, colloidal silica and less than 2% of an organic foaming agent.
The pneumatically applied product is separated into three types based on the chemistry and upper use temperature use limit:
Type | Chemical Composition | Upper Use Temperature ,°F |
---|---|---|
I | Calcium Magnesium Silicate | 2012 |
II | Magnesium Silicate | 2300 |
III | Aluminum Silicate | 3000 |
The liquid binder consists of a mixture of both organic and inorganic (colloidal silica) materials and is typically added in sufficient quantity to provide the fibers with necessary adhesion to the applied surface, cohesion to one another, and the required physical properties of the installed, dry insulation. Also, this type of fiber insulation is typically dimensionally stable with exposure to the maximum rate temperature for the particular Type I, II, or III. When first heated above a temperature of about 500° F, most or all of the organic binder decomposes, leaving only the colloidal silica binder.
The surface to which pneumatically applied high temperature fiber insulation is typically prepared with weld pins and wire mesh, the latter being applied a distance off the surface 1 inch less than the finished thickness. The pins and wire mesh assure the insulation material is firmly applied and will resist the effects of vibration and external forces.
Granular Insulations
Calcium Silicate
Calcium Silicate thermal insulation is defined by ASTM as insulation composed principally of hydrous calcium silicate, and which usually contains reinforcing fibers.
Calcium Silicate Pipe and Block Insulation are covered in ASTM C 533. The standard contains three types classified primarily by maximum use temperature and density.
Type | Maximum Use Temp (°F) and Density |
---|---|
I | Max Temp 1200°F, Max Density 15 pcf |
IA | Max Temp 1200°F, Max Density 22 pcf |
II | Max Use Temp 1700°F |
The standard limits the operating temperature between 80° to 1700°F.
Calcium Silicate Insulation Products
Calcium Silicate pipe insulation is supplied as hollow cylinder shapes split in half lengthwise or as curved segments. Pipe insulation sections are typically supplied in lengths of 36 inch, and are available in sizes to fit most standard pipe sizes. Available thicknesses range from 1" to 3" in one layer. Thicker insulation is supplied as nested sections.
Calcium Silicate block insulation is supplied as flat sections in lengths of 36", widths of 6", 12", and 18" and thickness from 1" to 4". Grooved block is available for fitting block to large diameter curved surfaces.
Special shapes such as valve or fitting insulation can be fabricated from standard sections.
Calcium Silicate is normally finished with a metal or fabric jacket for appearance and weather protection.
The specified maximum thermal conductivity for Type 1 is 0.41 Btu-in/(h·ft²·°F) at a mean temperature of 100°F. The specified maximum thermal conductivity for Types 1A and Type 2 is 0.50 Btu-in/(h ft² °F) at a mean temperature of 100°F.
The standard also contains requirements for flexural (bending) strength, compressive strength, linear shrinkage, surface-burning characteristics, and maximum moisture content as shipped.
Typical applications include piping and equipment operating at temperatures above 250°F, tanks, vessels, heat exchangers, steam piping, valve and fitting insulation, boilers, vents and exhaust ducts.
Molded Expanded Perlite
Molded Expanded Perlite Insulation Products
Molded Expanded Perlite insulation is defined by ASTM as insulation composed principally of expanded perlite and silicate binders. It may also contain reinforcing fibers.
Perlite Pipe and Block Insulations are covered by ASTM C 610. The standard covers the material for operating temperature between 80° to 1200°F.
Perlite pipe insulation is supplied as hollow cylinder shapes split into half or quarter sections or as curved segments. Pipe insulation sections are typically supplied in lengths of 36 inch, and are available in sizes to fit most standard pipe sizes. Available thicknesses range from 1" to 4" in ½" increments. Thicker insulation is supplied as nested sections.
Perlite block insulation is supplied in lengths of 36" and 1 meter, widths from 24" and in thickness from 1–½" to 6" in increments of ½". Perlite molded fitting cover insulation is available for a wide variety of standard elbow and tees.
Scored and V-Groove sections are also available. Special shapes such as valve or fitting insulation can be fabricated from standard sections.
Perlite is normally finished with a metal or fabric jacket for appearance and weather protection.
The specified maximum thermal conductivity both block and pipe insulation is 0.48 Btu-in/(h ft² °F) at a mean temperature of 100°F.
The standard also contains requirements for flexural (bending) strength, compressive strength, weight loss by tumbling, moisture content, linear shrinkage, water absorption after heat aging, surface-burning characteristics, and hot surface performance. In addition, the standard requires compliance with the standard for insulation for use in contact with austenitic stainless steel.
Typical applications include piping and equipment operating at temperatures above 250°F, tanks, vessels, heat exchangers, steam piping, valve and fitting insulation, boilers, vents and exhaust ducts. Perlite insulation is often used where water entering an insulation system may cause corrosion problems or process problems. Examples of this would be wash down areas, deluge testing, pipes that cycle in temperature, stainless steels that are susceptible to stress corrosion cracking.
Microporous Insulation
Microporous insulation is defined as a composite material in the form of compacted powder or fibers with an average interconnecting pore size comparable to or below the mean free path of air molecules at standard atmospheric pressure. Microporous insulation may contain opacifiers to reduce the amount of radiant heat transmitted.
The resulting blend of materials and pore structure produces a thermal insulation with extremely low thermal conductivity across a broad temperature range. The Microporous core material is completely inorganic making it non-combustible and suitable for passive fire protection applications.
An ASTM specification for Microporous insulation is under development with the following Grades and types:
Grade | Temperature of use, °C (°F), max |
---|---|
1 | 900 (1652) |
2 | 1000 (1832) |
2 hydrophobic | 250 (482) |
3 | 1150 (2102) |
Type | Brief Definition |
---|---|
I | Rigid Board |
II | Flexible Panels |
III | Pipe Sections |
Grade 2 Hydrophobic has been chemically treated to make the insulation water repellant. The water repellency is maintained up to its grade operating temperature of 250°C. Above this temperature it performs as standard Grade 2.
Microporous Board Insulation
Microporous Rigid Boards (Type I) are supplied in two primary forms. The first, typically identified as block or board, is an un-faced flat section of Microporous insulation compressed to a density of typically 18-25 pcf. The second type, identified as panel, is a flat section of Microporous insulation which has been encapsulated with a high temperature glass facing to minimize dust and improve handling. Normal densities are 14-18 pcf. Rigid Boards have superior compressive strength but normally cannot be flexed without cracking or breaking the material. Boards are produced in thicknesses from 1/8" to 4" depending on the specific type.
Microporous Flexible Panel Insulation
Flexible Microporous Panels (Type II) are manufactured at a lower density of approximately 8-16 pcf. They are also faced with a high temperature glass facing but also are often stitched through, in 1 or 2 directions, using a high temperature thread. The lower density and the segregation caused by the stitching allows the material to be flexed to cylindrical or contoured surfaces. Thicknesses range from 1/8" to ¾".
Microporous Pipe Sections (Type III) are supplied as hollow cylinder shapes split in half lengthwise or as curved segments. Pipe insulation sections are typically supplied in lengths of 19.7" (½ meter), and are available in sizes to fit most standard pipe sizes. Microporous Pipe Sections are faced with a high temperature glass facing to improve handling. The thickness is always 1" nominally (25mm). Thicker insulation can normally be supplied as nested sections for most pipe sizes. Pipe sections can also be used in combination with Type II Flexible Panels to meet specific thickness requirements.
With the exception of Hydrophobic Grade, all Microporous Insulation is permanently damaged by liquid water. Therefore protective jacketing must be used when the application is subjected to potential environmental conditions or water spray. Likewise, care must be taken during transportation, storage, and installation to prevent contact. Humidity does not degrade Microporous Insulation.
The standard facings for most Microporous Insulations are high temperature glass fabrics which have a use temperature which is below the maximum use temperature of the core. In the majority of applications, the Microporous Insulation is further jacketed, encapsulated, or sandwiched with other materials in a static environment. In these environments the facing provides mainly a handling and installation benefit. In applications where the product must function dynamically at temperatures above 800°F the product should be encapsulated in materials appropriate for the environment.
Typical values for thermal conductivity in Btu·in/(hr·ft²·°F) are 0.15 at 392°F, 0.17 at 752°F, and 0.19 at 1112°F. Microporous Insulation has compressive strength of 80 psi for a 10% deflection in a typical board product.
Microporous Insulation is most often used where a maximum amount of thermal resistance is needed with minimal thickness and weight. Typical applications include piping and equipment operating at temperatures above 250°F, tanks, vessels, heat exchangers, valve and fitting insulation, exhaust ducts, electronic instruments, and fire protection.
Flexible Aerogel Insulation
Silica Aerogel Insulation
Flexible aerogel insulation is a composite of an amorphous silica-based aerogel cast into a fiber reinforcement. The fiber reinforcement may consist of a batt, a needled felt blanket, or other configurations of fibers. The fibers themselves may be inorganic, such as glass fibers, or organic, such as polyethylene. The flexible aerogel insulation typically contains hydrophobic agents and may also contain opacifiers.
Flexible Aerogel insulation is covered by ASTM C 1728. The standard covers material for operating temperatures between -321°F and 1200°F. Materials are classified by use temperature and by thermal conductivity as follows:
Type | Grade | Category | Max Use Temperature, °F | Max k @75°F, Btu-in/(h ft² °F) |
---|---|---|---|---|
I | 1 | A | 257 | 0.17 |
I | 1 | B | 257 | 0.12 |
II | 1 | A | 390 | 0.13 |
II | 1 | B | 390 | 0.12 |
III | 1 | A | 1200 | 0.14 |
III | 2 | A | 1200 | 0.16 |
Type III, Grade 2 conductivities are tested in pipe configuration.
The standard also contains requirements for density, compressive resistance, surface burning characteristics, exothermic temperature rise, linear shrinkage, sag resistance, water retention, water vapor sorption, flexibility, corrosiveness to steel, and fungi resistance.
Flexible aerogel insulations are typically supplied in sheets ranging in thickness from 0.2 to 0.4 inches. Key applications include original equipment manufacturer (OEM), pipeline, vessels, and equipment in commercial and industrial applications.
Poured-In-Place
Granular Poured-In-Place insulation for underground piping, ducts, and tanks is available. These are granular materials generally made from engineered blends of inorganic materials or calcium carbonate and require no mixing or curing. The hydrophobic materials provide thermal insulation, corrosion protection, and load bearing properties. Product is sold by the cubic foot and is available in a variety of packaging options. The material is installed around underground pipes, ducts, or tanks before backfilling. Currently no ASTM Standard material specifications have been developed for these products.
Reflective Insulations
Reflective insulations are defined by ASTM as insulation depending for its performance upon reduction of radiant heat transfer across air spaces by use of one or more surfaces of high reflectance and low emittance. Reflective insulations utilize low-emittance foil (usually aluminum) or foil coated facings to reduce the amount of radiant heat flux occurring at the surface.
While reflective insulations obey the same laws of physics as any insulation system, they are typically relatively thin (usually less than ½"). Thus they present little resistance to conduction heat transfer through the material. They operate primarily by reducing the radiant heat flux to and from the surface of the insulation. Reflective foils are often used as facing on other more conventional insulations to provide additional thermal resistance. The Reflective Insulation Manufacturers Association (www.rima.net) is a source of additional technical information on reflective insulation products.
ASTM C 667 Standard Specification for Prefabricated Reflective Insulation Systems for Equipment and Pipe Operating at Temperatures Above Ambient Air covers prefabricated, multi-layer reflective insulation systems for equipment and piping.
Categories of Weather Barriers, Vapor Retarders, and Finishes
Most mechanical insulation systems require a covering or finish material. The primary reason is to protect the insulation from damage. Weather, mechanical abuse, water vapor condensation, chemical attack, and fire are all potential sources of damage. Additionally, appearance coverings are utilized to provide the desired aesthetics. Depending on the location and application, various terms have been used to describe these functions:
Weather Barriers are materials which, when installed on the outer surface of thermal insulation, protects the insulation from the weather such as rain, snow, sleet, dew, wind, solar radiation, atmospheric contamination, and mechanical damage.
Vapor Retarders are materials which retard the passage of water vapor into the insulation.
Mechanical Abuse Coverings are materials that protect the insulation from damage by personnel, machinery, etc.
Condensate Barriers (sometimes called moisture retarders) are materials, normally used as an inner lining for metal weather barriers, which will bar the condensate which tends to form on the inner surface of the metal jacket from contacting the metal portion of the jacket.
Appearance Coverings are materials used over insulation systems to provide the desired color or appearance.
Hygienic Coverings are materials used to provide a smooth, cleanable, surface for use in food processing, beverage, or pharmaceutical facilities.
These functions are performed by a number of different materials or material systems. In many cases, a single material can provide multiple functions (for example, a metallic jacketing often serves as protection from both the weather and from mechanical abuse).
There is some inconsistency in the nomenclature used for these materials. The terms jacketing, lagging, and facings are sometimes used interchangeably to describe the outer covering of an insulation system.
Adding to the confusion, the term vapor retarder has evolved. Historically, the term vapor barrier was used, but this has been generally replaced with the term vapor retarder in recognition of the fact that an absolute barrier to water vapor flow is difficult if not impossible to achieve. There is also movement toward the use of the term vapor diffusion retarder (VDR) to generically describe these materials.
Physical Properties of Weather Barriers, Vapor Retarders, and Finishes
Depending on the application, weather barriers, vapor retarders, and finishes are subject to certain requirements that must be considered when selecting a system:
Internal Mechanical Forces - Expansion and contraction of the pipe or vessel must be considered because the resulting forces are transferred to the external surface of the weather barrier. An ability to slide, elongate or contract must be accommodated for.
External Mechanical Forces - If a pipe, vessel or a specific area thereof is subject to mechanical abuse i.e. tools being dropped, abrasion from wind driven sand or personnel walking on the system, then these need to be considered in the design. This may impact insulation type used, as well as the weather barrier jacketing type.
Chemical Resistance - Some industrial environments may have airborne or spilled corrosive agents that accumulate on the weather barrier and cause chemical attack of the pipe or vessel jacketing selected. Elements that create corrosive issues must be well understood and accounted for. Insulation design of coastal facilities of course should account for chloride attack.
Galvanic Corrosion - The use of one metal in contact with a different metal must be considered for galvanic corrosion potential. Similarly water can act as an electrolyte and galvanic corrosion can happen due to the different potential of the pipe and vessel and a metal jacketing.
Insulation Corrosivity - Some insulation materials can cause metal jacket corrosion. Some insulation materials can chemically attack some polymer films. Both of these situations shorten service life.
Thermal Degradation - Hot systems are typically designed so that the surface temperature of the insulation and jacketing material do not exceed 140 degrees F. The long term effect of 140 degrees F on the jacketing material must be considered. Additionally, there may be solar radiation load and perhaps parallel heat loss from an adjacent pipe. This is a critical design consideration, particularly if a non-metal jacket is being considered.
Installation and Application Logistics - A common occurrence is that the insulation contractor installs more insulation in a day, than can be protected with jacket. If it rains, the exposed portion of insulation gets saturated and the next day the jacket is installed over the wet insulation. This creates an obvious potential corrosion issue before the installation is operational. If this occurs it must be corrected immediately. It should also be understood that the size, shape and adjacent space available to work may dictate the type of weather barrier specified. It is possible that constraints dictate that a less than desirable weather barrier option must be utilized. If this is the case, the maintenance schedule must recognize and accommodate for this.
Maintainability - The importance of a maintenance and inspection plan cannot be over emphasized to achieve the service life expected of the design.
The physical properties of importance to jacketings and facings are summarized below:
Water Vapor Permeance is defined by ASTM C 168 as the time rate of water vapor transmission through unit area of flat material or construction induced by unit vapor-pressure difference between two specific surfaces, under specified temperature and humidity conditions. For facing materials, water vapor permeance is commonly expressed in units of perms. In below ambient applications, it is important to minimize the rate of water vapor flow to the cold surface. This is normally accomplished by using vapor retarders with low permeance, insulation materials with low permeability, or both in combination. In above ambient applications, it is often desirable to have a "breather" facing that allows water vapor to escape without condensing. In either case, it is important to know the permeance of the facing materials. ASTM Test Method E 96 is used to measure the water vapor transmission properties of insulation materials.
Emittance of a surface is the ratio of the radiant flux emitted by a specimen to that emitted by a blackbody at the same temperature. For personnel protection and condensation control applications, a high emittance is desirable. For minimizing heat flow, a lower emittance surface is generally desirable.
Surface Burning Characteristics are generally determined by ASTM Standard Test Method E 84 which measures the relative burning behavior of materials by observing the horizontal flame spread along the specimen surface. Flame spread and smoke developed index are reported. However, there is not necessarily a relationship between these two measurements. Many other fire test are also used to characterize these materials. For example, textile products utilize ASTM D 6413 (Standard Test Method for Flame Resistance of Textiles) and NFPA 701 (Standard Methods of Fire Tests for Flame Propagation of Textiles and Films).
Tensile Strength of facings and jacketing materials is a measure of the damage resistance of the facing. For facing materials, tensile strength is typically measured per ASTM D 828 or D 882 with results reported in units of lbs/in of width. ASTM D 828 is designed for paper while ASTM D 882 is designed for thin plastic sheeting. For woven fabrics, ASTM D 5035 is the predominate test. Some specifications require testing in both machine direction and cross machine direction.
Dimensional Stability at elevated temperatures is measured in % using ASTM Standard Test Method D 1204. Specimens are exposed to temperatures of 150 F for 24 hrs.
Fungi Resistance of insulation facing materials is typically evaluated using ASTM C 1338, which calls for inoculating specimens with 5 different strains of fungi spores and then incubating them at 86 F, 95% RH for 28 days. The growth is then evaluated relative to a comparative material to assess the fungi resistance of the sample.
Thermal Integrity of the facing materials must match the application requirement. Flexible vapor-retarder facings are generally evaluated per ASTM C 1263, which subjects specimens to temperature extremes of -20 F to + 150 F, bends the specimens around a 1 in. OD mandrel, and then evaluates for any cracking or delamination.
Bursting Strength is a measure of the force required to rupture the facing in psi. It is measured in accordance with ASTM D 774 (up to 200 psi) or ASTM D 3786 (up to 500 psi).
Product Characteristics of Weather Barriers, Vapor Retarders, and Finishes
Metal Rolls or Sheets
Metal Rolls or Sheets at various thicknesses are commonly used for weather protection and abuse resistance. They are available with embossing, corrugation, moisture barriers and different banding and closure methods. Elbows, tees, valve and flange covers, beveled collars and end caps, wire, straps and screws are also available from manufacturers and fabricators.
In North America, the most common metal jacketing materials are:
- Bare aluminum
- Coated aluminum
- Stainless steel
Additional metal jacketings include:
- Painted steel
- Galvanized steel
- Aluminum-zinc coated steel
Common metal jacket thicknesses available in aluminum include 0.016, 0.020, 0.024, 0.032 and 0.040 inch. Those available in stainless steel include 0.010, 0.016 and 0.020 inch. Not all thicknesses are available in all material offerings from all manufacturers. The minimum thickness recommended for aluminum installed indoors is 0.016 inches; for stainless steel installed indoors, 0.010 inches. For outdoor installations, increase thickness on non-rigid insulations to at least 0.024 for aluminum and to 0.16 inch for stainless steel. Consult manufacturer's product data for available offerings.
Aluminum is weather resistant but susceptible to corrosive chemicals. Coated aluminum can be used to provide additional corrosion protection and to provide higher values of surface emittance where needed. Stainless steel offers the best chemical resistance and is commonly offered as Type 304 and 316. Type 316 offers greater chemical resistance than Type 304. Corrugated and stucco-embossed materials are better suited for applications exposed to physical abuse because they disguise surface imperfections.
For unprotected insulation exposed to severe weather, jackets are available with continuous longitudinal Z-shaped locking seams and weather resistant butt straps that offer the ultimate in weather protection.
Metal jackets should be specified with a moisture retarder on the inside surface to provide 100% coverage and resist galvanic corrosion. Common offerings include a 3-mil thick combination of polyethylene and Surlyn® coating (which is most suited for below ambient and cyclical operating temperatures), kraft paper coated with a 1-mil thick polyethylene film, and kraft paper coated with 3- mil thick polyethylene film.
For vertical tanks and vessels greater than 48 inches (1200 mm) in diameter, consider using either nominal 1–¼ or 2–½ inch (31 or 63 mm) deep, corrugated sheets or 4 by 1 inch (100 by 25 mm) box rib sheets for improved durability.
A number of ASTM Standards cover the selection and specification of metal jacketing materials:
- ASTM C 1423 "Standard Guide for Selecting Jacketing Materials for Thermal Insulation"
- ASTM C 1729 "Standard Specification for Aluminum Jacketing for Insulation"
- ASTM C 1767 "Standard Specification for Stainless Steel Jacketing for Insulation"
These Standards should be reviewed for additional information.
Polymeric (Plastic) Rolls or Sheets
Polymeric (plastic) rolls or sheets are available at various thicknesses. These materials are glued, solvent welded, or taped depending on the polymer. Elbows and tees are also available for piping for some type of polymers. Typical polymeric (plastic) jacketing materials are:
- Polyvinyl Chloride (PVC)
- Polyvinyliedene Chloride (PVDC)
- Polyethylene Terephthalate (PET)
- Polyvinyl Flouride (PVF)
PVC Jackets
PVC jackets are durable, attractive, and an easy-to-clean material that is typically field-applied over unfaced insulation and most factory-applied jackets where additional protection is necessary. PVC jackets are covered by ASTM Standard Practice C 921-10, Types I and II, Grade 4.
PVC jackets are available in several thicknesses and colors. Standard thicknesses are 10, 15, 20, 30, and 40 mils, with 20 and 30 mils being the most common thicknesses. Thicknesses of 30 mils are recommended for outdoor applications. Jacketing for outdoor use should be UV stabilized. White is the predominant color used; however PVC jackets are available in a variety of colors (colored jacketing is normally not available with UV stabilization).
Several manufacturers and fabricators offer PVC "cut and curl" jacketing products. Fitting covers are also available for covering elbows, tees, valves, flanges, mechanical couplings, drain bodies, strainers, end caps, and other common piping products. Accessory products (solvent adhesive, tapes, stainless steel thumbtacks, etc) are also available from manufacturers.
PVC jacketing up to 30 mil thicknesses generally meet 25/50 flame-spread and smoke-developed indexes. Jacketing temperatures should be kept below 150°F for hot services. PVC jackets can be used in areas requiring frequent washdown and are used extensively for applications requiring USDA and FDA approval. To achieve USDA and FDA approval, PVC jackets should be installed with continuous solvent welded joints and seams. PVC jackets and fittings, when applied over an intermediate vapor retarder and properly sealed, can be used on cold systems.
PVDC Film
PVDC Film is a flexible and tough vapor-retarder facing that is applied to the exterior of pipe, vessel, and equipment insulation systems. This vapor retarder consists of a biaxially oriented homogeneous opaque white polymer film. It can be factory or field applied to the surface of the insulation and is available in two thicknesses, 4 and 6 mils, both at 35.5" wide and more than 250 ft long. When factory applied to insulation, the lap joint of the vapor retarder is sealed in the field using a self-sealing lap (SSL). The PVDC tape is the same type of homogeneous white film to which an adhesive backing that does not require release paper has been applied. The tape is available at 2 and 6 mil thicknesses, widths of 1, 2, and 3 inches, and 150 ft length. PVDC films are not intended for exterior applications unless protected by a suitable weather barrier.
ASTM Standard Specification C 1136-10, Type VII and VIII covers this type of vapor-retarder facing for use where insulation outer surface temperatures are -20 to 150°F. This ASTM standard specification establishes requirements for permeance, burst strength, tensile strength, dimensional stability, flame/smoke performance, zero fungal growth, and lack of cracking or delamination.
ASTM Standard Practice C 921-10, Type II, Grade 4 covers this type of film for use as a vapor retarding outer jacket on thermal insulation over mechanical equipment such as tanks, pipe, and vessels. The 6 mil PVDC film meets the permeance requirements of Class A, "Extremely low permeance" or 0.01 perms maximum. The 4 mil PVDC film meets the permeance requirements of Class B, "Very low permeance" or 0.02 perms maximum.
Key applications for PVDC vapor retarder is in insulation systems for pipe, equipment, tanks, and ducts, especially those operating at temperatures below ambient such as food and beverage lines, refrigeration, ammonia refrigeration, and LNG pipe. PVDC film is applied to the insulation on straight sections of pipe or to large surfaces like tank or duct walls. PVDC tape is used to seal joints in the film, at vapor retarder butt joints on pipe insulation, can be wrapped around complex insulation shapes such as fittings and elbows, and can be used to repair physical damage to the vapor retarder film.
Laminates
Laminates are, in general terms, materials made by bonding (through the use of heat, pressure, adhesives or any combination thereof) two or more layers of materials. The layers can be comprised of similar or dissimilar materials. Laminates used for protective jacketing may be comprised of metal foils, plastic films, papers, nonwovens, scrims, etc. and may or may not contain a topcoat of some kind for coloration, UV resistance, contain varying degrees of configurations, etc.
For vapor retarder applications, at least one component must be a material that offers significant resistance to vapor passage. Laminates may be classified into three categories:
- Laminated Foil Jacketing (ASJ/ASJ+/FSK/PSP/FSP)
- Synthetic Rubber Laminates
- Multi-ply Laminates
Laminated Foil Jacketing (ASJ/ASJ+/FSK/PSP/FSP)
A commonly used pre-formed jacket for pipe, tank, and equipment vapor retarder applications is the lamination of white paper, reinforcing fiberglass scrim, and aluminum foil. Of secondary prominence is the same basic structure, with substitution of metallized polyester film for the foil component and/or a polymer film for the white paper component. These products are generally referred to as ASJ or ASJ+ (for all-service-jacket), and meet the requirements of ASTM C1136, Standard Specification for Flexible, Low Permeance Vapor Retarders for Thermal Insulation. These ASJ or ASJ+ facings are commonly used as the outer finish in low abuse, indoor areas; elsewhere, they are covered by a protective metal or plastic jacket. A similar facing material (FSK, for foil-scrim-kraft) has the same basic structure except with the aluminum foil layer facing outward. Numerous variations (e.g. FSP for Foil-Scrim-Poly, PSP for Poly-Scrim-Poly, and PSK for Poly-Scrim-Kraft, etc.) are available. Many types of insulation products are supplied with factory-applied ASJ, FSK, or FSP vapor retarders.
Synthetic Rubber Laminates
Synthetic rubber based laminates typically consist of aluminum facing laminated to a synthetic rubber membrane and a peel-and-stick application. These laminates are used on pipes, ducts, and tanks for both interior and exterior applications and may be used in direct burial applications. A variety of weights are available. Perm values of less than 0.02 are reported and the materials are generally considered to be "self-healing" in that small punctures and penetrations will re-seal.
Multi-ply Laminates
Multi-ply laminates consist of multiple layers of aluminum with alternating layers of polyester or polyethylene film with a peel-and-stick adhesive system. These laminates are used on pipes, ducts, and tanks for both interior and exterior applications. They cut easily and install easily in the field. Perm values of zero or near zero are reported. They are available in smooth or embossed surface finish in a variety of thicknesses. Several colors and chemical resistant films are also available.
Fabrics
Fabrics are often coated and used as insulation jacketing materials, particularly for removable/reusable insulation covers. The fabrics are woven from a wide variety of textile fibers including but not limited to:
- Canvas
- Fiberglass (Type E)
- Amorphous Silica fibers
- Ceramic fibers
- Aramid fibers
- Stainless Steel
- Inconel
Coatings and laminate membranes are usually applied to these fabrics to provide increased protection and abrasion resistance. Coatings used include but are not limited to:
- Acrylic
- Silicone
- Polytetrafluoroethylene (PTFE)
- Polychloroprene
- Vermiculite
The selection of the fabric/coating combination for a particular application depends on the temperature, abuse, chemical compatibility, and combustibility requirements. Click here to view additional information on fabrics or consult manufactures of fabrics or removable/reusable covers for guidance.
Mastics and Coatings
Mastics are available in numerous formulations designed to provide protection of the insulation from physical, chemical, water and weather damage. They can be broken-up into special use classes as described below, and the selection of the proper mastic will depend on the insulation type, equipment, piping or duct operating temperature, fire hazard classification required, expected service life and other conditions. Mastics can be applied to protect the entire insulation system surface, facing materials over insulation or over irregular insulation surfaces such as sprayed polyurethane foam systems, bends and elbows, protrusions such as flanges, valves, supports or insulation terminations where sheet materials can not be effectively applied. They are most often applied by brush, trowel or spray in two coats at the manufactures recommended application rate with a reinforcing mesh embedded between the first two coats. Typical reinforcing meshes are made of synthetic fibers, fiberglass scrim or cloth and canvas cloth. The mastic manufacturers application guide should be consulted for selection of the proper reinforcement to use with the mastic chosen.
Properties and tests commonly considered in the selection of a mastic are given in ASTM C 647, Standard Guide to Properties and Tests of Mastics and Coating Finishes for Thermal Insulation.
Mastics are broken-up into the following types and sub-types:
- Vapor Retarder (vapor barrier) Mastics and Coatings
- Solvent based thermoplastic rubber/resin types
- Common uses
- Cryogenic applications (below -40°F)
- Severe chemical environments
- Other benefits
- Fire resistive - meet Class A flame and smoke
- Highest performance of vapor retarders
- Lowest permeance
- Common uses
- Water based synthetic polymers types
- Common uses
- Low temperature piping and equipment (-40°F to Ambient)
- Sealing seams, punctures and terminations of vapor retarder facings
- Chilled water, air conditioning duct, brines
- Other benefits
- Fire resistive - meet Class A flame and smoke
- Low Hazards during application and shipment - low toxicity and no fire hazard
- Permeance: dependent on type - below 0.5 perms
- Common uses
- Solvent based asphaltic types
- Common uses
- Buried pipes
- Exterior low service temperature piping
- Other properties
- Chemical resistant
- Poor fire resistivity
- Common uses
- Solvent based thermoplastic rubber/resin types
- Weather Barrier (Breather) Mastics and Coatings
- Water based synthetic polymer type
- Most common type on the market
- Provide weather protection
- Keep liquid water out
- Allow water vapor to pass through over hot equipment
- UV resistance
- Protect vapor retarder facings (FSK, ASJ)
- Exterior ductwork and piping
- Weather protection
- Physical protection against puncture
- Water based asphalt emulsions
- Older technology
- Low material cost, but high labor cost
- Water based synthetic polymer type
Mastic Characteristics: When selecting the mastic to be used the following general characteristics and uses should be considered:
Vapor Retarder Mastics are designed to prevent the ingress of water vapor into cold insulation systems in addition to protection against mechanical abuse, liquid water intrusion and weather. Permeance of vapor retarder mastics will vary greatly ranging from 0.5 perms to <0.01 perms depending on the mastic type and performance requirements. Most manufacturers will provide information on the mastic's permeance on their product data sheets. When comparing permeance of a mastic the test temperature, test relative humidity and film thickness must be considered. Changes in any of these properties will affect the permeance of any mastic.
Cold insulation systems with respect to mastics can be further defined by:
- cryogenic service (operating below -40°F)
- low temperature service (-40°F to 32°F)
- cool/cold service (33°F to ambient).
Cryogenic insulation systems require specialized engineering beyond the scope of this document. Mastics and coatings for these uses have very low permeability (<0.02 perms) and include specialized vapor stop coatings with extremely low service temperature limits (down to -320°F) and solvent based thermoplastic rubber (Hypalon) mastics. Contact the mastic manufacturer for assistance in selecting these materials.
Low temperature service mastics should have permeance of <0.02 perms. These products include solvent-based thermoplastic rubber and water based synthetic rubber mastics. The solvent based mastics will typically have the lowest permeance, highest chemical resistance and longest service life, however, they may be restricted for use in some regions, are combustible during application and require solvents for clean-up. Some water based mastics have permeance values below 0.02 perms, can be used in all regions and have the added advantage of being non-flammable during application and easy water clean up.
Cool or cold service insulation includes insulation of chilled water piping, air conditioning ductwork and other systems operating between 33°F and ambient. The proper mastic and permeance requirements for these systems will depend on whether or not the system is interior or exterior, the facing on the insulation, the likelihood of physical or mechanical abuse, the climate (high vs. low humidity environment) and insulation type. There are still some solvent-based mastics used for these applications however in most cases water based mastics will meet the required performance and are preferable. The vapor retarder system, including any sheet facing materials and mastics, should have permeance <0.05 perms per ASTM C 755.
In many cases insulation for duct systems or piping in warm humid climates will be faced with a FSK, ASJ or other vapor retarder jacket. In this case a water based mastics with permeance <0.5 perms are typically acceptable for vapor sealing punctures (from hangars or pins) and seams in the facing on interior applications. These mastics can also be applied over the entire facing surface to provide additional physical protection if required or physical and weather protection of the facing on outdoor insulation. If the insulation is not faced with a vapor retarder jacket or at insulation terminations or over bare insulation the mastic should have a permeance less than 0.05 perms. Reinforcing mesh embedded in the mastic is typically required per manufacturers guidelines.
Weather barrier mastics and coatings are also commonly referred to as "breather" coatings. They are specifically designed to provide protection of the insulation from physical abuse and/or weathering. They are normally water based synthetic polymer coatings. These mastics have higher permeance, > 1.0 perm, than vapor retarders and will allow water vapor to pass through them while repelling liquid water. This is particularly important when used over hot equipment or piping where trapped moisture must be allowed to pass through the mastic to avoid blistering of the coating. Weather barrier coatings also find use on dual temperature systems; such as rooftop HVAC ductwork used for cooling and heating or dual temperature water piping, where the insulation contains a vapor retarder facing that requires weather protection. On exterior applications the insulation should always be sloped to avoiding ponding water.
On interior applications on hot pipes specialized lagging adhesives and coatings may be used with fiberglass cloth or canvas cloth to create an insulation cover. The lagging adhesive is used to both bond the cloth to the insulation as well as to provide a protective finish.
Inspection, Maintenance and Repair of Mastic Systems
Mastics are a key component in the protection of many insulation systems and need to be inspected, maintained and quickly repaired to function properly. Regular inspection of the mastic, as part of an overall insulation system maintenance program, should be conducted. Inspection should include visual observation for any cuts, tears, punctures, chemical breakdown, embrittelment from chemical attack or other damage to the mastic or reinforcement. Any build up of dirt or other chemical contaminants should be removed to ensure that underlying damage has not occurred and to prevent deterioration of the mastic. Surface wear should be repaired by thoroughly cleaning the surface before applying a new finish coat of mastic. The use of reinforcing mesh may be required if there was damage or exposure of the previous reinforcement. If damage includes a breach of the mastic such as a puncture, tear or through cut the insulation system should be closely examined to ensure that water or contaminants have not entered the insulation system. If the insulation is wet or damaged it must be removed and replaced prior to re-applying any mastic. Any newly applied mastic should be reinforced per the manufacturers recommendations and extend at least three inches over the previously sealed and cleaned surface.
Coatings generally need to be re-coated every 2—3 years. If applied to flexible insulation products or insulation materials that will expand and contract during service, they may "egg shell / crack" but will not flake or peel off. This egg shelling effect may detract from the appearance of the application; it will not generally affect the UV performance of the product. It can be re-coated for extended service life.
Insulating and Finishing Cements
Insulating and Finishing Cements are mixtures of various fibers, powders and binders sometimes used to insulate and finish irregular surfaces. ASTM C 195 covers Mineral Fiber Thermal Insulating Cement (for use up to 1900 F), ASTM C 196 covers Expanded Vermiculite Thermal Insulating Cement (for use up to 1800 F), and ASTM C 449 covers Mineral Fiber Hydraulic Setting Thermal Insulating and Finishing Cement. (for use up to 1200 F).
These materials are typically mixed with water to the consistency of a paste and then troweled on to the surface to be covered.
Fabrications of Insulation Products
Most mechanical insulation systems require some degree of fabrication. The degree required will vary depending on the complexity of the job and the materials used. Some mechanical insulation products can be ordered directly from insulation manufacturers in standard sizes with factory-applied facings. These products still require some fabrication in the field to accommodate valves and fittings, etc. Other insulation materials (i.e. cellular glass, phenolic, polyisocyanurate, and polystyrene) are manufactured in relatively large size blocks or buns, and must be cut into the appropriate size and shape. While this fabrication is sometimes done in the field, the work is more often done by insulation fabricators and/or distributor/fabricators that specialize in this work.
Insulation Fabrication Standards
Insulation Fabrication Standards and guidelines are generally developed by the insulation manufacturers based on experience with their products. These standards provide specifics on the dimensions to be used and the allowable tolerances. In some cases, industry standard specifications are available. They are:
- ASTM C 585 Standard Practice for Inner and Outer Diameters of Rigid Thermal Insulation for Nominal Sizes of Pipe and Tubing
- ASTM C 450 Standard Practice for Fabrication of Thermal Insulating Fitting Covers for NPS Piping, and Vessel Lagging
- ASTM C 1639-07 Standard Specification for Fabrication of Cellular Glass Pipe and Tubing Insulation
Specifiers are encouraged to utilize these standards when specifying fabricated products, or to specify fabrication to the insulation manufacturers' instructions. This can be particularly important in regards to the type of adhesives used.
Removable and Reusable Insulation Covers
Removable and reusable insulation covers are fabricated insulation products used in industrial and commercial applications where insulation must be periodically removed for inspection and maintenance. Equipment with irregular or complex surfaces such as turbines, pumps, and valves can be insulated with removable covers. The covers are generally fabricated from flexible insulation materials enclosed in fabric or metal mesh containment. The seams are sewn (usually machine) with thread, staples, or metal rings. The covers are designed to fit closely with tight joints on the valves, piping, or equipment. A suitable attachment system is incorporated and the covers are easily removed and replaced. Requirements will vary with the application, with commercial applications generally less demanding than industrial sections.
Removable covers should be designed for acceptable thermal performance, compatibility with operating temperature, weather and atmospheric conditions, fire endurance, and sound attenuation. Covers can be classified into the following categories:
- Flexible insulation blankets or pads
- Formed and shaped insulation covers
- Fabric finish
- Metal encased
- Metal canning and framing
- Removable elastomeric insulation covers
Flexible insulation blankets or pads are made in flat form, designed to wrap on specific contour with slots or notches provided for nozzles or interference points. The blankets can be provided with flaps or overlap edges to prevent wind and rain penetration. Blankets can be made in any thickness but thicknesses over 2 inches are usually made in two or more layers.
Formed or shaped insulation covers are made to conform to the shape of the fitting, valve, or equipment, having the same curvature built into the insulation and fabric or metal canning.
Metal canning and framing covers are used where physically strong removable insulation enclosures are required. Canning consists of metal sheets formed to shape, and lined with insulation. An inside metal lining may be required.
Removable Elastomeric insulation covers are constructed from insulation materials, adhesives, bands, and light metal frames.
The materials used to make removable covers are generally standard products and can be classified into the following:
- Insulation materials
- Encasement materials
- Stitching materials
- Attachment system
- Identification system
Click here to view a glossary of frequently used terms for removable/reusable insulation covers and example bills of material for these products.
ASTM C 1695 Standard Specification for Flexible Removable and Reusable Blanket Insulation for Hot Service provides guidance in specifying removable insulation covers for surfaces operating in air at temperatures above ambient.
Accessory Products
Adhesives
A variety of adhesives types are available for many different applications including insulation attachment, insulation fitting fabrication and facing. Adhesives are available in water based, solvent based, hot melts, reactive cure, pressure sensitive adhesives and aerosol formulations for application by numerous methods including brush, spray, trowel and roll coater. When selecting an adhesive the insulation type, service temperature limits, application method and required adhesive strength should all be considered. Refer to the adhesive manufacturer's product selection guides for assistance in choosing adhesives for specific uses. In all cases, regardless of the type of adhesive used to secure the insulation, it is important to prepare the surface being adhered to. It must be free of dirt, rust, loose particles, and oil. Wiping the surface with denatured alcohol is often recommended. Ambient and surface temperature are also important factors in selecting an adhesive. When considering ambient temperatures, it is important to factor in the temperature over the entire curing time. The surface being bonded to must also be considered. Steel (coated or painted), plastic (such as polypropylene) or others may require special preparation work or special adhesives.
For attachment and fabrication, in general, rigid insulations will require thicker, high-bodied adhesive capable of filling small gaps while flexible insulations such as fiberglass, mineral wool, or elastomeric use thinner higher coverage rate adhesives. Attachment or fabrication of impermeable insulations will require contact adhesives, pressure sensitive, or reactive cure adhesives to avoid trapping vapors. Water based adhesives are not recommended. When using contact adhesives, it is important to coat both surfaces with a thin coat of adhesive (a thin coat is better than a thick coat) and to allow the solvents to evaporate before combining the two surfaces. This may vary with installation conditions (temperature and humidity). When using pressure sensitive adhesives, it is important to apply pressure to insure the adhesive is wetted out between the two surfaces being adhered. As the installation temperature gets colder, the amount of pressure to wet out the adhesive increases.
Other specialty adhesive includes cryogenic adhesives for very cold operating systems (down to -320°F) and high temperature inorganic adhesives for hot work (up to 800°F). When used for attachment most adhesives are used in conjunction with mechanical fasteners.
Duct liner adhesives include water and solvent types as well as pressure sensitive adhesive and hot melts. They can be applied in a sheet metal shop either as part of a coil line or on fabrication tables. Typical duct liner specifications require two forms of attachment that generally are weld or stick pins and an adhesive. On coil lines the adhesives is often water based to allow for immediate weld pin placement without concern for flash fire. Water based adhesives do not work well with closed cell foam duct liner materials because the water can't evaporate. Hot melt, spray adhesives or pressure sensitive adhesives are often used on these products.
Reinforcements for Cements and Mastics
Reinforcing fabrics for cements and mastics are critical to prevent cracking over seams or areas of movement and to improve the overall strength of the finish. They come in a variety of types and sizes. The reinforcement chosen must be of the correct type and size and be compatible with the mastic or cement to ensure proper function. Refer to the mastic or cement manufacturers product data sheet for compatible reinforcements. Fiber fabrics include open weave fiberglass and synthetic fiber meshes and woven canvas and fiberglass cloth. Mastics are typically reinforced with "10x10" open weave cloths for most applications. Heavier duty, 5x5 mesh, cloths are sometimes used with heavier coats of mastics. Reinforcements should always be embedded within the wet mastic or cement and be fully covered. All seams in the fabric should be overlapped by a minimum of two inches to avoid potential for cracking.
Sealants
Sealants can be broken up into the following general categories:
- Duct Sealants
- Sheet metal sealants
- Duct board sealants
- Flashing Sealants
- Joint Sealants
Duct sealants come in a variety of formulations. Typically the sealant is a high-bodied water or solvent-based formulation applied by brush or cartridge gun. UL-181 A-M for duct board and UL-181 B-M for flexible and rigid metal duct give standard requirements for duct sealants that may be used to specify them. In addition for metal duct they should meet the SMACNA pressure class for the duct system being sealed. Refer to the duct sealant manufacturers product data sheets and material selection guides for more information.
Flashing sealants are used to seal insulation terminations, penetrations and protrusions such as around valves, gauges and other areas where the insulation is broken. They may also be used to seal metal jacketing seams. Flashing sealants protect the exterior of the insulation system from the ingress of liquids and/or vapors. The flashing sealant must be compatible with all surface in comes in contact with including the insulations and insulation finishes. It should be applied per the manufacturers instruction such that it forms a complete watertight seal.
Joint sealants are used to seal the longitudinal and circumferential butt joints of rigid insulation against moisture penetration. Joint sealants are of particular importance in cold temperature systems to lock out water vapor penetration between blocks of insulation. Formulations are of high solids and are available in a variety of types. The joint sealant should remain flexible after application to allow for movement in the insulation system without cracking or splitting. Selection of the proper joint sealant will depend on the operating temperature at the point where the sealant is applied, the insulation type being sealed and the finishes being applied over the top of the insulation. Refer to the manufacturers product data sheets and product selection guides for more information on selection and application of joint sealants.
Other Accessory Products
There are a wide variety of additional accessory products required for successful installations of mechanical insulation, including:
- Securments
- Studs and Pins
- Staples, rivets, and screws
- Clips
- Wire or Straps
- Self-adhering laps
- Tape
- Flashing
- Stiffening
- Supports
- Heavy density insulation inserts
- Pipe support saddles and shoes
- Wood blocks and dowels
- Pre-insulated pipe supports
- Caulking
- Expansion/contraction devices
These accessory products are readily available from a number of vendors. (see Product Data Sheets below)
Glossary of Terms
For Removable/Replaceable Insulation Covers
Hot Face - The inside surface area of a removable/reusable insulation cover. The materials in direct contact with the item being covered.
Cold Face - The outside surface area of a removable/reusable insulation cover. The materials exposed to atmospheric and ambient temperature conditions.
One Piece Construction - A removable/reusable insulation cover designed and fabricated to be installed as one unit, rather than two or more components requiring separate installations to comprise the finished cover.
Inside Seam - A sewn seam which is turned to the inside of a cover shell, so as not to show on the outside.
Outside Seam - A sewn seam which is not turned to the inside of a cover shell, but remains exposed to the outside.
Closing Seam - The final seam sewn on a cover after the shell has been filled with the core insulation.
Parting Faces - The edges of a removable/reusable insulation cover which butt together when the cover is installed and secured.
Terminal Ends - The ends or tops of a removable/reusable insulation cover which are drawn down around adjacent insulation, valve packing stems, pump flange nozzles, etc.
Gusset Construction - Fabricatio of a removable/reusable insulation cover using inside seams to achieve square edges on the cover rather than rounded edges.
Core Unit - The insulating material(s) inside a removable/reusable insulation cover.
Tie-Down/Anchor Straps - Straps used in conjunction with buckles to secure removable/reusable insulation covers in place when they are installed on the items being insulated.
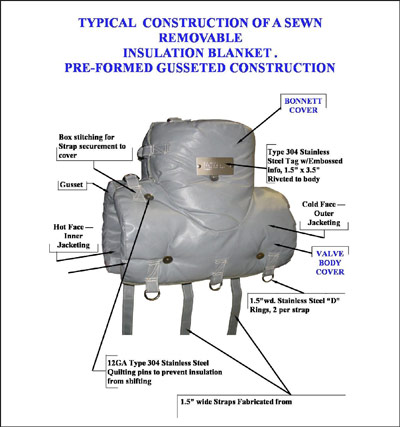
Example Bills of Materials
For Removable/Reusable Insulation Covers
BILL OF MATERIALS #1 | |
---|---|
For insulation of fittings, valves and equipment operating indoors or outdoors with operating temperatures of up to 500°F | |
Inner Jacketing | 17oz./cu.ft PTFE Coated Fiberglass cloth, |
Outer Jacketing | 17oz./cu.ft PTFE Coated Fiberglass cloth, |
Side Gussets | 17oz./cu.ft PTFE Coated Fiberglass cloth, |
Insulation Core | 2" Thk.—6#/Cu.Ft. Density "ET" blanket |
Seam Closure | PTFE coated fiberglass thread |
Seam Fasteners | PTFE cloth straps with stainless steel double D-rings and Type 304 Lacing hooks & 16Ga S.S. tie wire |
I.D. Tags | Type 304 Stainless steel with embossed lettering |
(*) — for service temperatures up to 350°F — 1"thk. — (3" to 1") should be used |
BILL OF MATERIALS #2 | |
---|---|
For insulation of fittings, valves and equipment operating indoors or outdoors with operating temperatures from 501°F to 750°F | |
Inner Casing | 0.008" x 60# Dens. Type 304 Stainless Steel wire mesh |
Inner Jacketing | Hi-temperature/Pure Fiberglass Cloth |
Outer Jacketing | 17oz./cu.ft PTFE Coated Fiberglass cloth |
Side Gussets | Hi-temperature/Pure Fiberglass Cloth & 011" x 60# Dens Type 304 Stainless Steel wire mesh |
Insulation Core | 2" Thk.—9-11#/cu.ft Dens Needled Mat |
Seam Closure | 10-ply type 304 Stainless steel thread |
Seam Fasteners | PTFE cloth straps with stainless steel double D-rings and Type 304 Lacing hooks & 16Ga S.S. tie wire |
I.D. Tags | Type 304 Stainless steel with embossed lettering |
BILL OF MATERIALS #3 | |
---|---|
For chilled water applications | |
Inner Jacketing | 17 oz./sq. yd. PTFE Coated Fiberglass Cloth. |
Outer Jacketing | 7 oz./sq. yd. PTFE Coated Fiberglass Cloth. |
Insulation Core | 2" Thick, 6# Density Blanket Fiberglass. |
Seam Closure | Pure PTFE Thread |
Seam Fasteners | Both Straps and Hook and Loop Fasteners Shall be used for securing the blankets. Hook & Loop Fasteners shall be Fire Retardant |
Quilting | To Prevent Insulation from Shifting within The cover, Quilt Pins of 12 GA stainless steel shall be used. The pins shall not Penetrate the inner face of the covers. |
I.D. Tags | Type 304 Stainless steel with embossed lettering |
BILL OF MATERIALS #4 | |
---|---|
Turbines and hi-temperature equipment | |
1ST LAYER — HOT SIDE | |
Inner Jacketing Outer Jacketing & Gusset | Inconel type Wire Mesh |
Insulation Core | 2" Thick – 8# Density Ceramic Wool |
Seam Closures | ½" Stainless Steel Hog-Rings, 1" O.C. |
Seam Fasteners | Type 304 Stainless Steel 12 Gauge T-type Lacing Anchors with Self-Locking Washers and 12" Stainless Steel Annealed Tie Wire. |
I.D. Tags | Type 304 Stainless Steel with Embossed Lettering |
2ND LAYER — COLD SIDE | |
Inner Casing & Gusset | Hi-temperature/Ceramic type Cloth |
Outer Jacketing | 17 oz./sq. yd. PTFE coated Fiberglass Cloth |
Insulation Core | 2" Thick – 9-11# Density, Type "E" Needled Glass Mat |
Sewing Thread | Type 304 Stainless Steel, 10 Strand Thread |
Fasteners | Type 304 Stainless Steel, 12 Gauge J-type Lacing Anchors with Self-Locking Washers and 16 Gauge Annealed Stainless Steel Tie Wire |
I.D. Tags | Type 304 Stainless Steel with Embossed Lettering |
Fabrication Requirements
Removable/Reusable covers shall meet the following requirements:
- All covers for all piping, fittings and equipment shall be manufactured pre-formed creating a close contour fit and conform to the configuration of the items being insulated, utilizing a "separate inner and outer skin" method of design to create a finished pre-shaped cover.
- All valve covers shall be designed and manufactures with sewn-in bonnets with proper allowances for packing gland opening.
- All covers shall utilize gussets to provide a full extent of insulation thickness throughout the cover. Gussets shall be made of the same materials as the inner skin fabric and be a separate piece of fabric joining the inner and outer skins. All covers shall be manufactured inside-out, then turned correct side out before inserting the insulation.
- All seams shall be machine sewn, double lock-stitched with 8-10 stitches per inch from 1/8" to 1/2" apart.
- The insulation core should be secured within the jackets with 12 GA stainless steel quilting pins, backed with 12 GA stainless steel self-locking washers. Hand tufting with cross type stitch thru the entire thickness through the blanket using 10 strand stainless steel thread can be used instead of pin quilting.
- No substitution of specified materials shall be made without written permission from the Engineers and Purchasers of the client.
Construction Specifics for the Turbine on Double Layer Blankets
- All covers shall repeat the shape of the turbine as close as possible.
- The outer, 2nd layer covers shall be staggered over the inner layer covers by a minimum of 6" for the ultimate in thermal performance.
- Detailed installation drawings on CD-ROM's along with installation instructions, (3 sets), must be supplied with shipments of blankets. The drawings shall show the shape of each blanket in both layers and their exact location on the turbine.
Insulation Textiles
Applications
Insulation textiles are used in a variety of applications including:
- Removable/Reusable insulation jackets or blankets to insulate high maintenance/high temperature equipment
- Removable/Reusable fireproofing jackets and blankets
- Lagging fabrics and tapes to insulate for freeze and personal protection or reinforce insulation jacketing
- Tapes and tubing to insulate electrical, hydraulic and air hoses and tubing
- Welding blankets to protect personal or valuables from sparks, spatter or slag
- Fire blankets to help extinguish fires
- Apparel for hot work and radiant heat protection
Textile Materials for Insulation
Insulation textiles, fabrics, threads, tapes, tubing and blanket are available untreated, treated, coated, impregnated or laminated. Aramids, fiberglass, high purity silica, ceramic fiber and stainless steel are the primary base materials from which textile materials are manufactured. There are a variety of coatings and laminate materials to apply to these textiles. Coating and laminate membranes are usually applied to these textiles to create a process, weather or moisture barrier and abrasion resistance at low or elevated temperatures. These textiles are available in a variety of widths, thickness and densities. In addition, these textiles are available with various thermal conductivity, temperature and chemical compatibility limits.
Temperature Limits | ||
---|---|---|
Continuous | Maximum | |
Untreated Fabrics, Threads, Tapes, Tubing, Blanket | ||
1) Aramids | 600 F | 850 F |
2) Fiberglass (Type E) | 800 F | 1200 F |
3) Fiberglass w/ SS wire insert | 1000 F | 1200 F |
4) High Purity Silica Glass (96+%) | 1400 F | 1800 F |
5) Ceramic Fiber w/ E glass insert | 1000 F | 2300 F |
6) Ceramic Fiber w/ SS wire insert | 1800 F | 2300 F |
7) Stainless Steel ( 304 ) | 1500 F | 2300 F |
8) Inconel | 1800 F | 2300 F |
Coatings | ||
1) Acrylic | 250 F | 250 F |
2) Silicone | 500 F | 500 F |
3) PTFE | 550 F | 700 F |
4) Neoprene | 400 F | 400 F |
5) Vermiculite | 2000 F | 2300 F |
Fabric Laminates | ||
1) Polyester/Mylar | 350 F | 350 F |
2) Aluminum Foil | 750 F | 900 F |
3) 304 SS Foil | 1500 F | 2300 F |
4) Inconel Foil | 1800 F | 2300 F |
Untreated Fabrics, Threads, Tapes, Tubing and Blanket
Aramids
Arimids were developed in the 1960s and 1970s as a high heat resistant fiber that does not melt, has good solvent resistance, very low flammability, is non conductive, has a good thermal conductivity and a high temperature limit of 850 degrees F. This product is sensitive to acids, salts and ultraviolet radiation.
Fiberglass (Type E)
Fabrics, Threads and Tapes - See Mil C 20079 H
Fabrics, Tapes and Tubing - See Mil Y 1140
Blanket or Felt - See Mil I 16411 F
Incombustibility - See USCG 164.009
Corrosion Potential - See Mil I 24244 or NRC 1.36
Type E fiberglass is the primary yarn used to produce textile grade fabrics, threads, tapes tubing and blanket. This material is incombustible and has good strength to 800 F., where it still retains 60% of its tensile strength. At 1200 F., the strength retained is 20% and the melt point is 1530 F. When used with a SS insert, the yarn retains much of its strength to 1000 F. Type E fiberglass yarn has a low thermal conductivity and is resistant to many solvents and acids. This product is sensitive to high alkalinity and bases.
High Purity Silica Glass (96+%)
Fabrics - See Mil C 24776A (SH)
Incombustibility - See USCG 164.009
Corrosion Potential - See Mil I 24244 or NRC 1.36
High purity silica yarn made into fabrics, tapes, tubing and blanket is a very good high temperature alternative to refractory ceramic fiber applications. These products have relatively low strength and abrasion resistance. Silica textiles have good fabrication properties when coated with silicone (for temperatures to 500 F) and vermiculite (for temperatures to 1400 F). The maximum use temperature is 1800 F. High purity silica has a low thermal conductivity. Silica textiles are sensitive to high alkalinity and bases.
Ceramic Fiber w/ E glass and SS inserts
Ceramic fiber yarn is produced with Type E fiberglass and SS inserts into each yarn strand. This yarn is then woven, knitted, braided into fabrics, tapes, or tubing. Ceramic fiber blanket is made by spun or blown fiber which is then directly needled or felted into various thickness and densities of blanket. Ceramic fiber textiles have use temperatures of 1000 F for glass inserted yarn; 1800 F. for SS inserted yarn; and 2300 F., 2600F and 2800 F. for various chemistries of ceramic fiber blanket. Ceramic fiber is sensitive to high alkalinity and bases.
Stainless Steel or Inconel Knitted and Woven Fabrics
Stainless steel wire of various diameters are woven, knitted and braided into flat fabrics and sleeves of various widths and thicknesses for high temperature applications. These products are used as the hot face in composites and coverings to reinforce the tensile strength losses at high temperature. The wire type used should be specified to match the application.
Coatings
Acrylic
Acrylic coatings are applied as a weave set or light coating to allow the textiles to stay together during and after fabrication. This light coating will also keep potential air born fiber to a minimum. Acrylic is inherently flammable, so a good flame inhibitor is needed in many applications. Acrylic is a low temperature coating that melts at 250 F.
Neoprene (Synthetic Rubber)
Neoprene rubber makes an excellent water proof and fire resistant coating for high temperature textiles. In addition, due to neoprene's non-flammability characteristics, it is widely used to coat high temperature textiles to weather proof and for welding or fireblanket applications. Neoprene has a maximum use temperature of 400 F and is resistant to many acids, bases and solvents.
Silicone (Synthetic Rubber)
Silicone is a widely used high temperature rubber coating that is applied to fiberglass fabrics to create a weather proofing and used as the cold face and hot face liners for making removable reusable insulation jackets or blankets. Silicone is also applied to tapes and tubing to waterproof and protect these textile products from abrasion and chemical spills. Silicone has a maximum used temperature of 500 F. and is chemically resistant to most acids, bases and solvents.
PTFE
PTFE is a high temperature thermoplastic that is applied to fiberglass and other high temperature textiles for protection against weathering and hostile chemical attack. PTFE coatings do not melt however soften at a temperature of 630 F. and starts decomposing at above 800 degrees F. PTFE is the most chemically inert liquid or vapor proof coating that man has ever made which is why this coating is used in chemically hostile applications. Since PTFE is a thermoplastic, this film can also be heat patched or sealed with another PFA appropriate film. As with frying pans, since nothing sticks to PTFE , the surface can also be easily cleaned.
Vermiculite
Vermiculite is a mineral that is emulsified into a high temperature coating. Vermiculite coatings are used on high temperature textiles to help spread heat energy throughout the coating minimizing the localization of heat and the temperature rise in localized areas.
Vermiculite is also an excellent binder and weave set for high temperature textiles. The maximum use temperature is 2000 F.
Fabric Laminates
Fabric laminates play an important role in the use of insulation textiles in industry. The three major film materials used are polyester, aluminum foil and 304 SS foils. A 1-2 mil, aluminized polyester is a popular reflective film that is laminated to a variety of fabric materials for radiant heat reflection applications such as fire entry suits or other hot applications where radiant heat protection is needed. Mylar has a max temperature of 350-400 degrees F., however the films reflective property help to keep the film below this temperature.
Aluminum and 304 SS foils are also used mostly as a vapor or moisture barrier with the fabrics acting as reinforcement for strength purposes. The maximum use temperature is usually determined by the adhesive if not sandwiched between another membrane.