Rebecca Mayes
Rebecca Mayes has been Business Development Manager at MC&I-RIDGLOK (www.MCI-RIDGLOK.com) for 20 years and is a Certified Insulation Energy Appraiser. She has a Bachelor of Arts Industrial/Organizational Psychology from the University of Southern Indiana, Magna Cum Laude. She can be reached at Rebecca@MCI-RIDGLOK.com.
March 1, 2020Insulation is a vital component in applications ranging from meat processing and candy manufacturing to wastewater storage tanks. This article focuses on insulation’s role in different segments of food storage/processing and agribusiness.
Insulating Tank and Storage Structures
The agriculture industry insulates a wide variety of tanks and silos for multiple uses, including:
- Silos for dry storage of fine materials (such as flour and sugar),
- Grain silos,
- Fire protection water storage tanks,
- Anaerobic digesters for creating bioenergy and reducing refuse costs,
- Wastewater tanks,
- Storage of fats and grease for recycling, and
- Fertilizer storage.
The benefits of insulation in these applications will sound familiar to those in the mechanical insulation industry: energy savings, better process efficiency, and a reduced total cost of ownership over the lifespan of the system. Insulation saves on monthly energy costs by conserving use of heating or cooling equipment. And in the case of vertical standing seam insulation (VSSI) panel systems, the design of the structures themselves aids in prolonging the insulation lifespan because the insulation itself is protected from exterior weather conditions and expansion/contraction from hot and cold fluctuations. In these systems there are several types of insulation that can be used including polyisocyanurate insulation board, mineral wool, fiber glass, foamglas, calcium silicate, expanded perlite, and aerogel insulation. The insulation system used can be applied to all types of tanks, including flat bolted, chimed bolted, glass lined, fiber glass, welded, stainless steel, and concrete; and the system can be used for both heated and cold storage applications, without the need to take the tank out of service.
In these applications, insulation is used to help control condensation, which helps minimize mold and mildew. It also minimizes freezing of products stored in the tank or silo, allowing for more even distribution of the product when it is unloaded. Insulation also saves on monthly energy costs by conserving any required heating or cooling of the product. Protecting the stored product from freezing or being heated by solar radiation also assists with process control. Thermal regulation also is crucial to many stored dry bulk products.
From a design standpoint, insulation panel systems used on vertical storage tanks exposed to the elements need to stand up to heavy wind loads. Consideration must be given to the attachments and to all structural connections to prevent the need to replace insulation frequently because of weather-related wear. In addition, different applications require compliance with their own relevant codes—e.g., fire protection water storage tanks that need to comply with National Fire Protection Association (NFPA) codes and standards, such as NFPA 22, Standard for Water Tanks for Private Fire Protection.
Design and material selection also may be affected by the customer’s goals in terms of appearance. Beyond standard form and function, some companies seek to create quasi-billboards out of storage tank structures, using color and the addition of logos or lighted signs to promote their business and reinforce their brand.
Installation considerations include whether the insulation system can be installed using aerial man-lift (which is standard for VSSI panel systems) or if scaffolding is required. The amount of system (and, if needed, scaffolding) assembly on site can affect the timeframe and staffing requirements for the job. Depending on the system type, attachment may require welding of support rings and insulation anchors on the shell. For the roof, conventional insulation systems require welding of steel structures and weld pins; while for VSSI panel systems, tack welding of the round bar is required only if a welded tank is used. As with all types of insulation applications, having experienced, qualified installers is critical to ensure the system will perform as specified.
Standard maintenance should be performed for all insulation systems. For these panel systems, it involves periodic caulking at the penetrations. If this simple maintenance is not performed, moisture can penetrate the insulation, causing extra weight, sagging, and failure of the entire system.
Anaerobic Digestion: Generating New Energy
Another segment of the agriculture industry where insulation plays a key role is anaerobic digestion—an emerging technology used in many food-processing facilities, as well as on farms and in other areas where large amounts of organic and food waste are produced. This waste is stored in an anaerobic digester storage tank, where it is introduced to a number of different microorganisms. Anaerobic digesters are specifically designed to facilitate the anaerobic digestion process under a controlled atmosphere process in a large, sealed tank which is void of oxygen. The bacteria and other organisms break down the waste, leaving very little behind. The method reduces the amount of waste the facility produces, removing any need to store or dispose of it.
While anaerobic digestion can occur naturally, the airtight and temperature-controlled environment in a storage tank accelerates the process, achieving maximum biogas production in a short period of time. The biomass is heated to around the temperature of blood, when it will react with the naturally occurring microorganisms and bacteria.
The tanks used in anaerobic digestion must be properly sealed to keep any air from entering and unbalancing the carefully controlled environment within, and to keep the bacteria and other gases from leaking out and potentially harming any people and animals nearby. Insulation systems protect the process and conserve energy by helping to regulate the interior temperature of the stored waste, keeping it within the optimal heated temperature range in order to promote bacteria growth to produce renewable energy sources.
Figure 4 shows an example of an agricultural anaerobic digester tank.
In addition to being used to reduce the overall amount of landfill gas in the air by degrading animal and food waste, anaerobic digestion also has applications in the renewable energy sector. It can be used to create a gas made up of carbon dioxide, methane, and several other gases. The resulting biogas has qualities that make it ideal for use as a fuel or a fertilizer, and for producing electricity that can be sold back to the power grid or used to power the facility. Overall, using waste to create fuel has the potential to lower costs and provide energy that requires very little investment.
In Summary…It Pays to Insulate!
From grain storage silos to anaerobic digesters, insulation provides the food processing and agribusiness industries all the benefits realized in its many other applications: improved process control, condensation and mold growth control, protection from temperature variance (from freeze protection through heat loss), cost and energy savings, and more. On top of that, when you consider insulation’s role in optimizing the efficiency of anaerobic digestion, reducing the overall amount of landfill gas in the air and helping to create a source for renewable energy, its “green value” and benefits multiply exponentially.
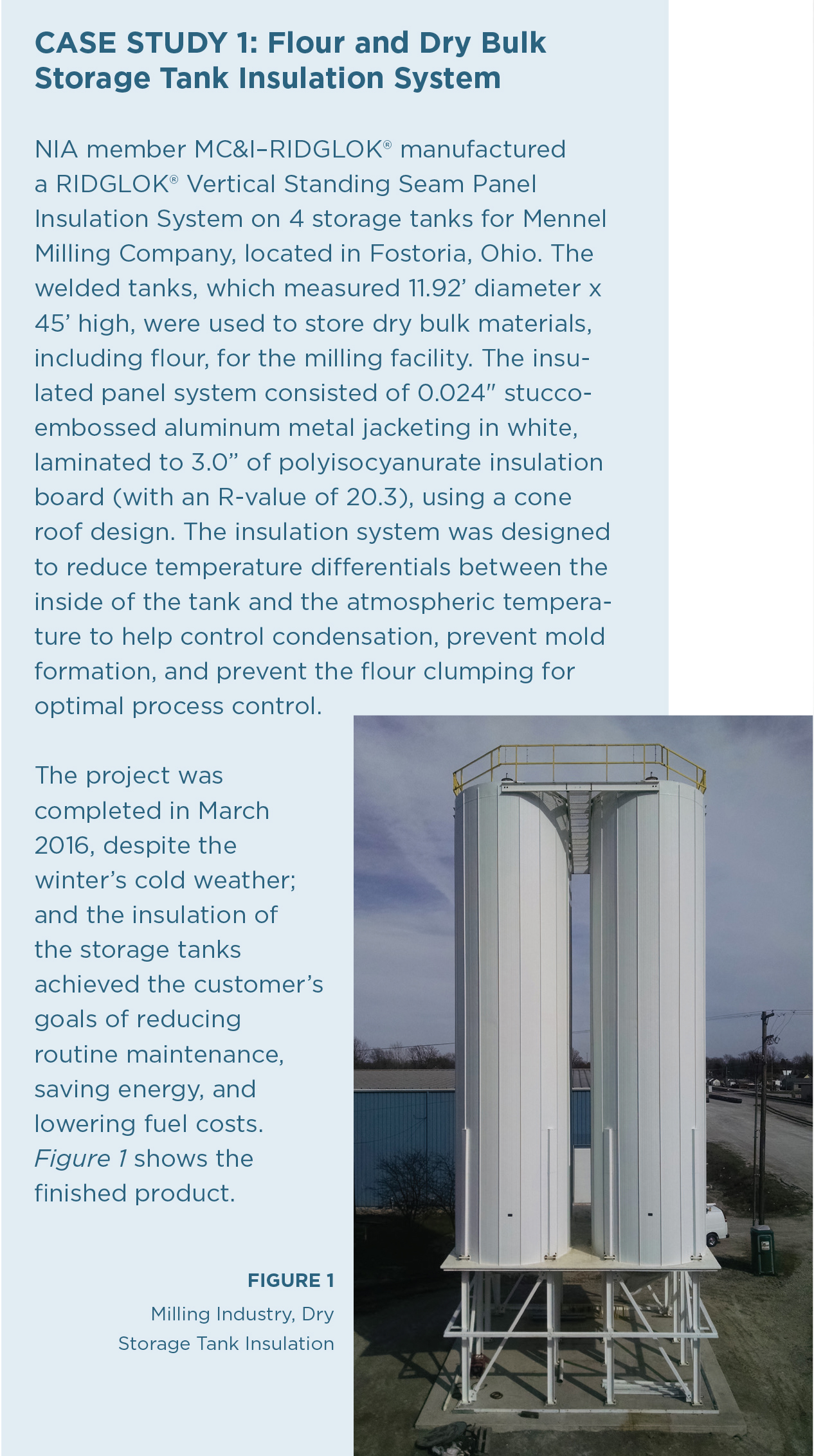
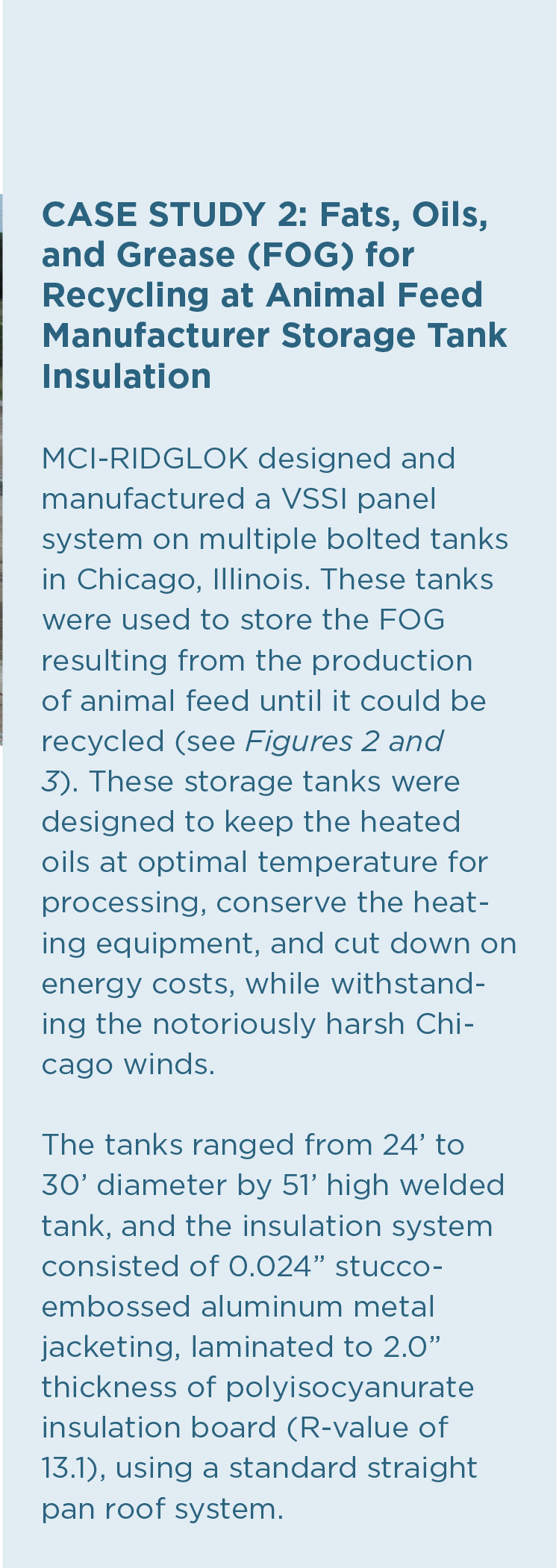
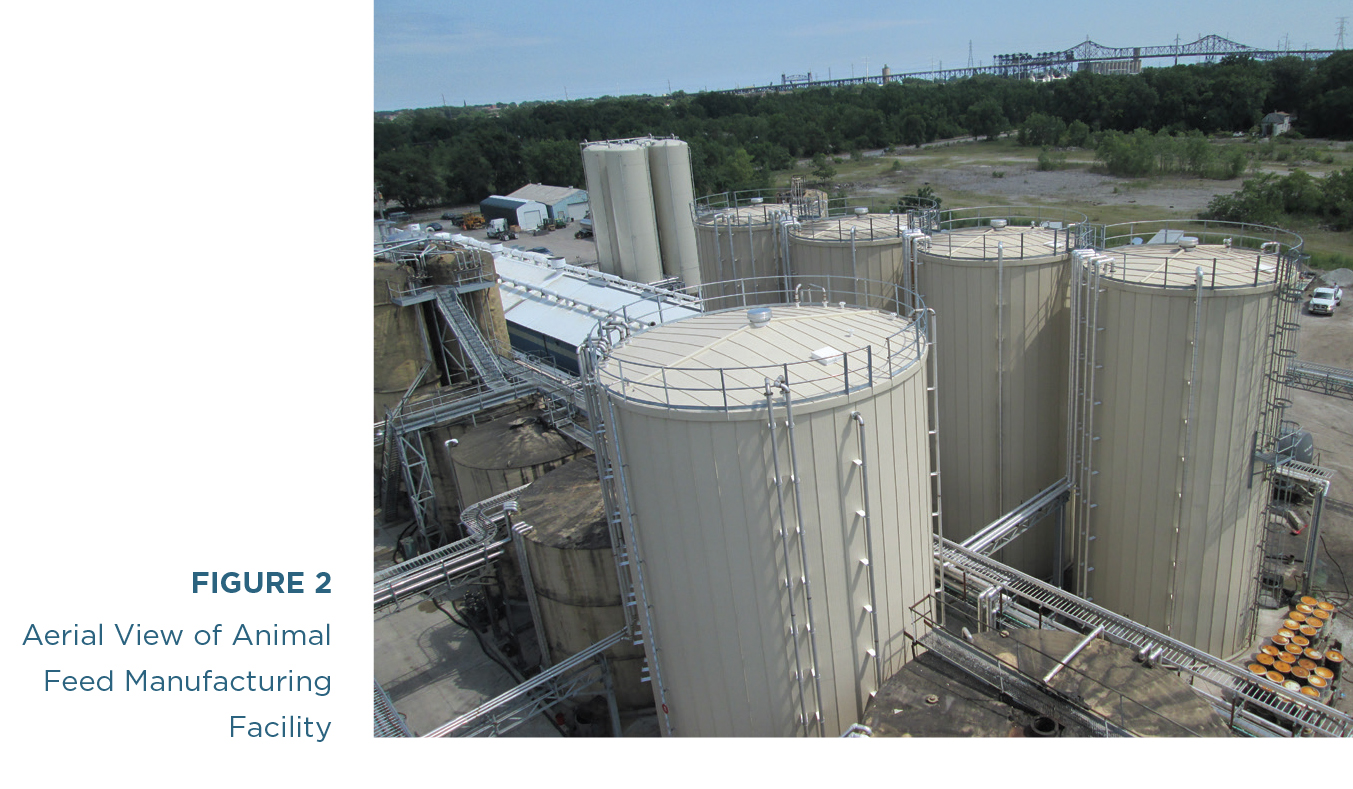
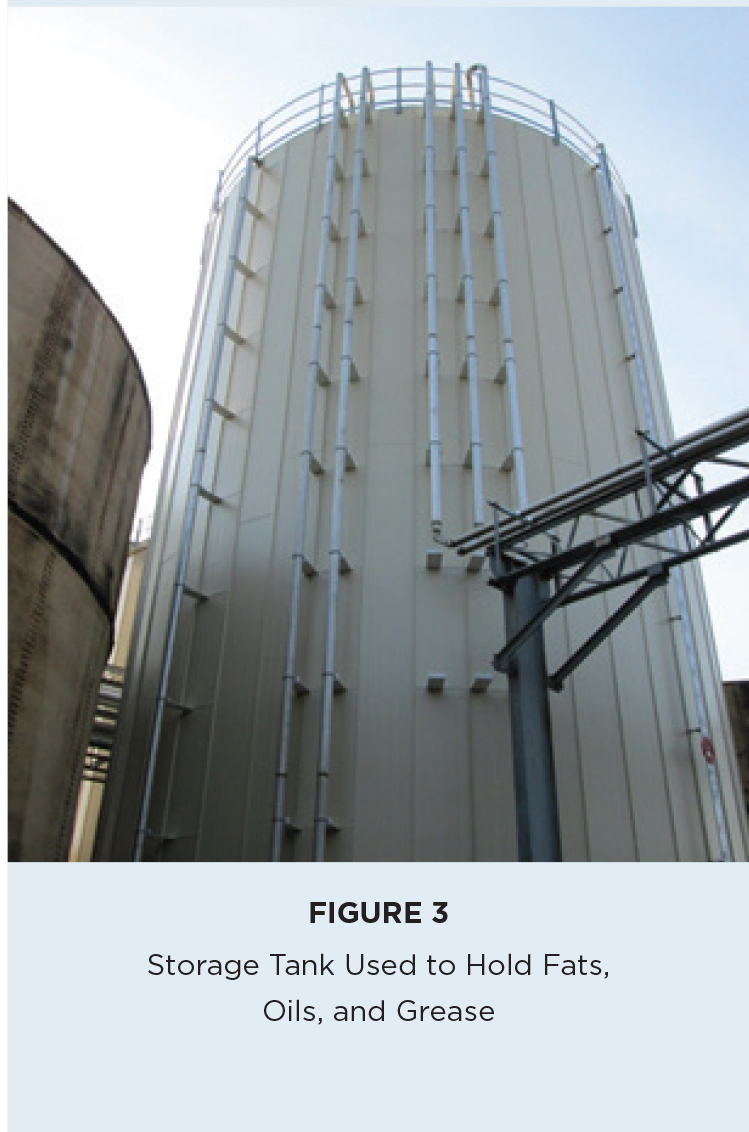
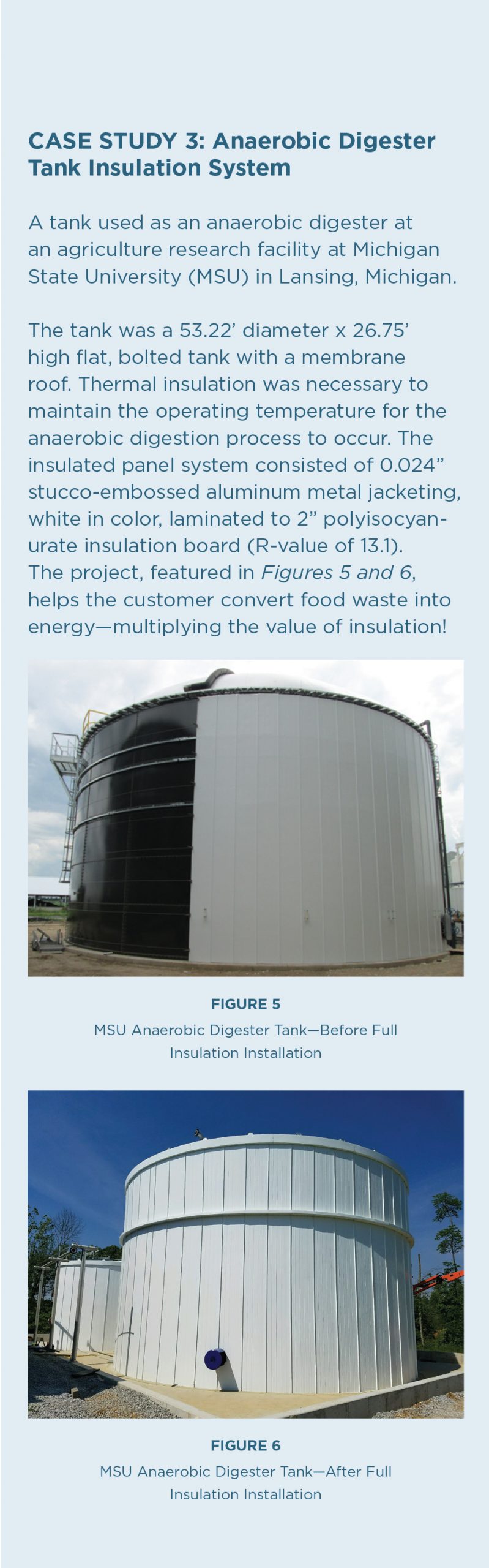