The other day I returned from a business trip in the late afternoon. I unpacked my suitcase and got a bite to eat, then decided to check my messages. That is when I realized I misplaced my cell phone. I knew I had it when I arrived home, so I retraced my steps: I checked my truck, my closet, my empty suitcase—I even checked inside the refrigerator. No luck. I could not find it anywhere. I had the feeling I was looking right at it; I just couldn’t see it. Fortunately, a friend stopped by and helped me search. Sure enough, she found it almost immediately (I had placed it on a dining room chair).
Think about how often you walk past something so familiar in your home or workplace that the item no longer registers in your brain. Or think about your morning commute—suddenly, you are at the office and you have no conscious recollection of how you got there. You were on autopilot. Have you ever gone into the break room at work and noticed something was missing—but you have no idea what—until a coworker says, “Oh, looks like we finally got rid of that extra water cooler taking up floor space for the past 2 years.”
We cannot always see what is right in front of us. Our brains are incredible acclimators of sensory stimuli. We are hardwired to notice anomalies, the unfamiliar. Often, we take the status quo for granted—for example, telling ourselves that the extra water cooler must be there for a reason, or someone would have gotten rid of it. After a while, we stop seeing the water cooler.
The “fresh eyes” approach to workplace safety involves inviting outsiders (whether external or internal to your company) to look at your jobsite. Soliciting constructive criticism requires many of us to step out of our comfort zone, but the benefits of a fresh set of eyes can be lifesaving. As the Director of Risk and Safety of a specialty contracting company, part of my job entails visiting our various, nationwide worksites and conducting safety audits. Our company performs these audits frequently and rigorously for this very reason.
In addition to ensuring physical safety for your workforce, performing regular safety audits makes good fiscal sense. Plus, an excellent experience modification rate (EMR) is appealing to both clients and insurers alike. Ideally, your organization has dedicated, properly trained safety personnel to conduct regular audits. If this is the case, you may consider switching up assigned worksites to prevent auditors from becoming overly familiar with any one site. But if your organization does not support full-time safety personnel, you still have several options to maximize the benefits of the fresh eyes approach.
Solicit an External Review
The fresh eyes approach provided by an external auditing firm can lift your company’s safety program to the next level. Knowledgeable, experienced safety professionals help mitigate workplace injuries while ensuring compliance with applicable standards and regulations. By using professionals outside your organization, you benefit from an objective, unbiased review. Safety experts will assess the current safety management protocol and help determine the use and effectiveness of corporate policies and procedures regarding compliance.
In addition to objectivity, using an outside auditor provides your business with an expert who can both identify potential hazards and share the best practices being used by similar companies in your industry. An external audit can help protect your greatest asset—your employees—as well as strengthen your standing with regulatory agencies.
Option 1: No-Cost Audits
The Occupational Safety and Health Administration (OSHA) offers no-cost audits to assist businesses in identifying safety and health hazards and risks at their worksites. These audits are performed separately and independently from a routine OSHA inspection.
This type of audit offers advantages beyond a free-of-charge service. Business owners benefit from the insights provided by highly trained inspectors without receiving citations or penalties, regardless of potential infractions. Furthermore, OSHA treats these inspections as confidential; no identifiable information is shared with OSHA’s standard inspection staff. What’s the catch? Before the auditor arrives on site, you are required to make a commitment that you will remedy any serious safety and health hazards noted by the inspector. Under certain circumstances, using this service may qualify your business for a 1-year exemption from standard OSHA inspections.1 Although this service is considered confidential, some organizations are hesitant to invite OSHA on site. For them, there are other options.
Option 2: Private, Third-Party Audits
Several independent consulting companies provide auditing services. The costs of using independent, outside agencies vary; and, as with any service, it is strongly suggested that you check references. Many states have safety councils, which may be able to recommend a reputable company.
Third-party consulting companies generally offer services beyond the initial audit, including training, providing a written safety policy, and offering corrective solutions to hazardous situations. The National Safety Council (NSC) offers both on-site assessments and an audit of your current safety program.2
When hiring an outside agency, expect that minor issues will be identified and addressed, but the focus of most audits should be identifying high-risk, high-impact issues. Your eyes may have picked all the low-hanging fruit. What are the high-impact items you missed?
Regardless of which third-party auditor you select, there are a number of clear benefits, as well as a few potential drawbacks.
The benefits include (but are not limited to) the following:
- Injury prevention. By identifying actual or potential hazards before an incident occurs, we create a safer environment for all employees.
- Promoting a culture of safety. Soliciting external advice demonstrates that we value our safety program. It signals to our employees that we are willing to learn and grow.
- Cost savings. The time and money invested in conducting a thorough audit pales in comparison to non-compliance fines, increased insurance rates, or treating a workplace injury.
- Public perception. Not only do audits keep your worksite prepped and ready for regulatory compliance inspections by federal or state agencies, but adhering to a clear safety, risk, and environmental health policy is also good public relations.
Potential drawbacks of a third-party audit may include:
- Initial cost. Depending on the size and complexity of your worksite, an audit can take several days and may require more than one on-site inspector.
- Follow-up cost. Resources must be allocated to remedy any findings. Again, however, this likely will be far less expensive than correcting an issue after an incident occurs. In addition, from the regulatory agency perspective, leaving a documented issue uncorrected is far worse than being unaware of that issue.
Simply stated, the fresh eyes process is designed to identify and correct compliance issues before something bad happens. When it comes to workplace safety, ignorance is not bliss.
Internal Safety Reviews
For those reticent to invite OSHA to their worksites, or those who do not have the budget to hire a third party, there is another option.
Companies with full-time safety specialists have the advantage of familiarity with company policy and organization. A thorough knowledge of your company’s procedures goes a long way in assessing a site’s safety. Additionally, an internal auditor has the authority to take immediate action if an imminent hazard is identified. Internal audits, however, include the potential pitfall of overfamiliarity—the danger that we no longer notice what we see every day.
How to Benefit from the Fresh Eyes Approach
One of the simplest ways to overcome the obstacle of overfamiliarity involves rotating safety personnel from site to site. Alternatively, if your company works on one site at a time, rotate your internal inspectors so that the same person is not always looking at the same thing. Often, a simple change of perspective is enough to identify previously unnoticed issues. If you are the sole safety expert at your company, start your next inspection at the back of the worksite. Try to imagine you are seeing the site for the first time.
Internal audits do not require the additional expense of a third-party company and, when properly conducted, can lead to team building among employees. Our company makes an effort to publicly commend any workers and safety practices that go above and beyond. By acknowledging the efforts of others—and by admitting when we have fallen short or made a mistake—we encourage a culture of communication and safety.
We recently had the experience of reassigning several employees to alternate locations. These temporary transfers immediately paid off. By providing fresh eyes, we were able to enjoy the benefits of outside knowledge and observation to enhance workplace safety at both jobsites.
In the first instance, a site superintendent who normally manages projects at electronic and microprocessor facilities discovered a potentially hazardous—although regulation-compliant—chemical containment issue. We had conducted inspections of this area several times but had not identified the potential issue. The superintendent’s experience in the world of microprocessors drew his eye to a situation that was considered normal and acceptable elsewhere. While the normal practice was fully in compliance with regulations, investigation by the job’s Project Manager uncovered that the newly suggested storage method was, in fact, a better way. Not only were the fresh eyes valuable, but the Project Manager accepted the suggestion and looked into the situation further. This willingness to say, “There might be a better way,” is what makes a company’s safety policy exemplary. When the owner noticed the better practices in place, he researched the situation, discovered the added safety benefits of the secondary containment recommendation, and quickly implemented the method company wide, as it proved to be a safer, more cost-effective means to protecting employees and the environment.
In the second example, during a routine jobsite hazard analysis, an employee from our corporate office noticed people working on a grated, elevated deck (Figure 1). The industrial power-generation setting was atypical to the employee’s day-to-day work environment, thus providing a fresh point of view.
Watching the workers on the elevated deck reminded him of something that had occurred a few weeks earlier when he was leaving church. He had been standing on a grated catwalk, and as he reached into his pocket to retrieve his keys, a small item slipped out and fell through the grate. His slender pocketknife fell 15 feet to the walkway below. Luckily, the knife blade was securely locked within the handle and no one was hit, but the knife landed 3 feet from a pedestrian walking beneath the catwalk. Blade or no blade, this could have caused a serious injury had the passerby been struck.
Recalling this incident at the jobsite, the employee noticed both machinery and access and egress points on the deck underneath the elevated platform. The employee remembered a solution he had seen at another construction site for protection against falling objects. He discussed falling object protection with the crew at the power production facility (Figure 2). The process was well received and immediately implemented. It has been so successful that it may become standard operating procedure on the jobsite. The employee’s suggestion was to line the grate with plywood prior to erecting scaffolds above it.
A third instance of fresh eyes providing solutions involved an office administrator. For record-keeping reasons, she is occasionally copied on internal safety audits. After reviewing an audit, she noticed potential ergonomic issues for employees who were required to move small tools, pieces of material, and other items. After considering the number of repetitive bends, twists, and lifts being done by her coworkers in the field, she retrieved a light-duty utility cart from the storeroom and brought it to the attention of a company executive. She suggested that the utility cart could be used just as easily in the field as in the office (Figure 3). We implemented the suggestions, and the number of biomechanical movements associated with that task reduced significantly.
In some cases, field personnel do not want to hear about how to improve their work habits from an office worker. By encouraging fresh eyes communications, we hope to eliminate that attitude. Promoting a culture of innovative solutions helps mitigate the fear that managers and workers might have about accepting suggestions from outside personnel. As a result, the work becomes safer and more efficient as new solutions are added to our toolbox.
Facing Resistance
It is difficult to invite criticism—especially from a third party. Asking an outsider to judge your safety program is not easy. But the alternative—believing we and our coworkers are always in a safe space—can be catastrophic. Rather than fear the judgment or ramifications of a thorough safety audit, consider it for what it is: a fact-finding and fact-facing mission. Once we identify workplace hazards, we can remediate them. There is no shame in not knowing what we don’t know.
According to Jim Kerr, Global Chair at N2Growth, soliciting an outside opinion leads to better decisions and provides a strategic advantage over the competition. Mr. Kerr believes that additional perspectives uncover previously unseen opportunities, provided we listen to feedback and demonstrate a willingness to adapt.3
Regardless of the method you choose, conducting thorough health and safety inspections will eventually reflect positively on your company’s bottom line. The temporary cost is easily offset by the benefits: maintaining the safety and morale of employees, improving insurance rates, instilling confidence with vendors and clients, and winning outstanding inspection marks from regulatory agencies.
Sources:
1. “OSHA’s On-Site Consultation: Process and Benefits,” United States Department of Labor: Occupational Safety and Health Administration, accessed July 13, 2019, www.osha.gov/dcsp/smallbusiness/program_info.html.
2. “NSC Assessments Identify Gaps in Your Safety Program,” National Safety Council, accessed July 14, 2019, www.nsc.org/work-safety/services/consulting/onsite-assessments.
3. Kerr, James, “Want to Make Smarter Decisions and Be a Better Leader? Get an Outside Opinion,” Inc.com, July 23, 2018, www.inc.com/james-kerr/seeking-outside-perspectives-isnt-a-sign-of-weakness-its-smart-leadership-heres-why.html.
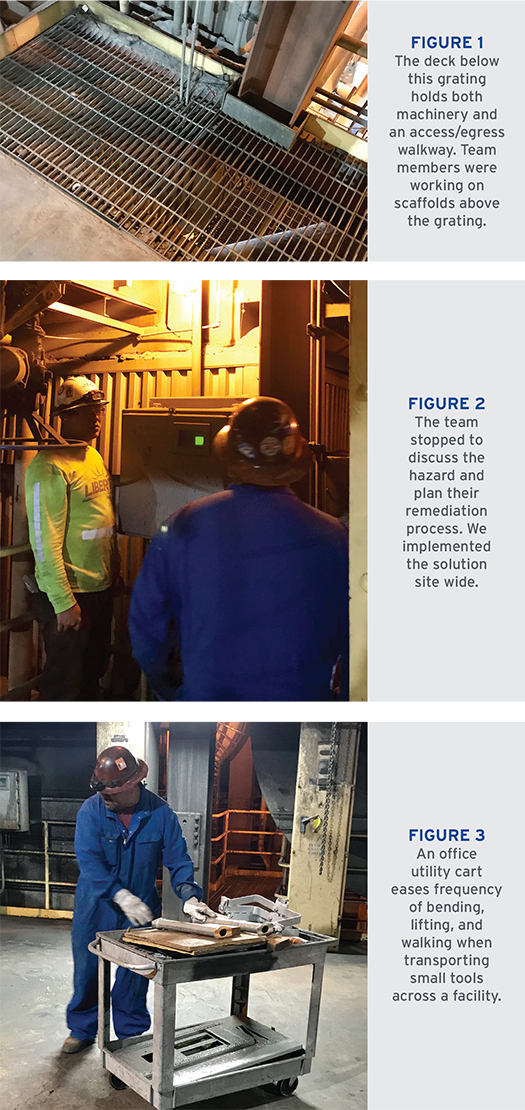