Chilled-Water Piping Condensation Control For Energy Savings and Risk Avoidance
Proper mechanical insulation of chilled-water piping is critical. The life-cycle cost savings and risk avoidance made possible by insulating chilled-water piping is vital to the design of a high-functioning system. Chilled-water pipe insulation is the wrong place to attempt value engineering when designing new or replacement piping. Incorrect product selection or using untrained installers can cause a building owner’s life-cycle costs to increase by millions of dollars compared to the minor cost premium of correctly insulating the pipe. These mistakes can also create a liability for future chilled-water pipe replacement; in the worst-case scenario, this can even lead to a catastrophic failure of a system that will damage a building and possibly even affect its occupants.
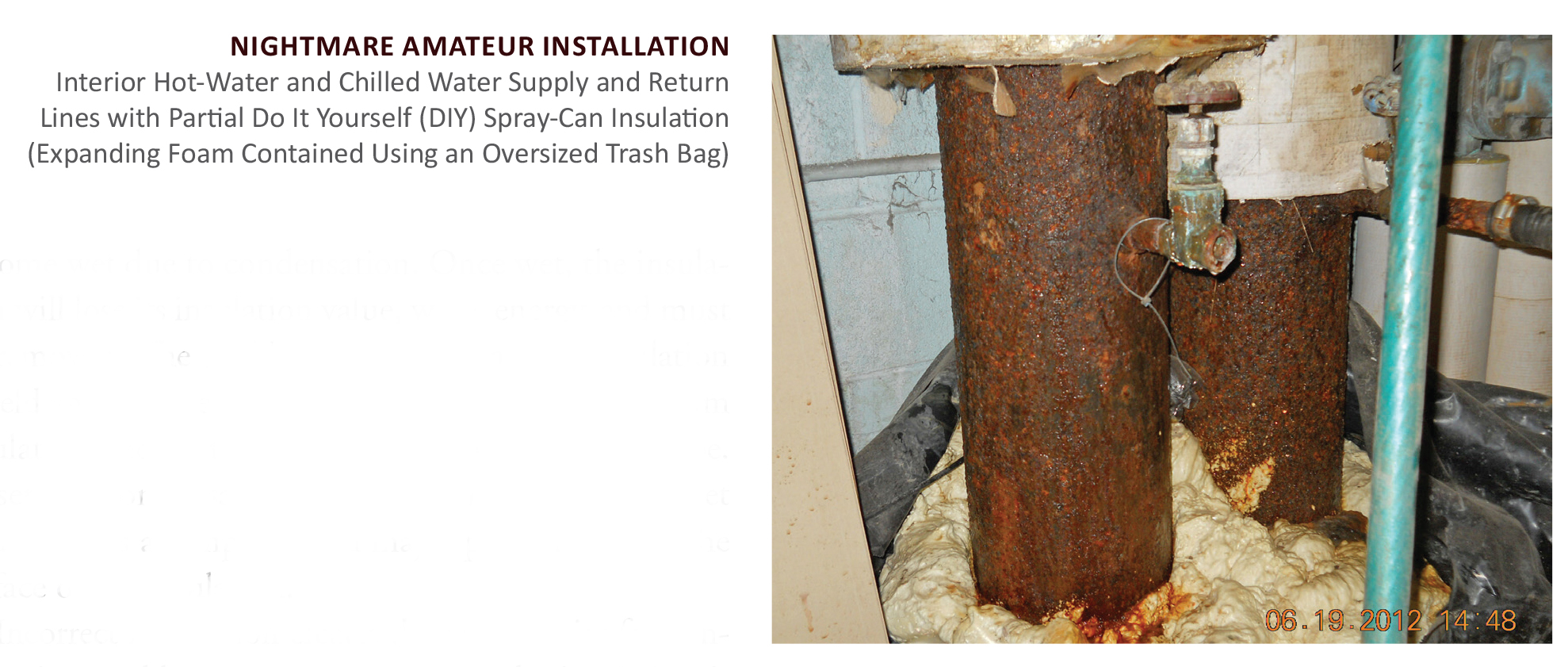
Chilled-water piping represents about 15% of all pipes installed in the United States. The selection of the correct pipe insulation can be critical to energy consumption and potential piping damage, especially in higher humidity areas near major bodies of water. What works in the dry desert southwest obviously will not work in major cities close to the oceans, lakes, and major rivers. If you look at the U.S. map, you will note that most of the country’s major cities are built near the water, for obvious reasons.
Mother Nature does not like differences in temperature, pressure, or humidity. Therefore, you can expect natural flow from an area of high humidity toward an area of low humidity. This effect is magnified if there is also a flow from medium temperature to extremely low temperature (i.e., 42°F chilled-water piping).
If the wrong insulation product is used, it can become wet due to condensation. Once wet, the insulation will lose its insulation value, waste energy, and must be removed. The problem gets worse as wet insulation is held against steel pipe. Due to gravity, the maximum insulation wetness tends to be on the bottom of the pipe. Observing ondensation leaking from insulation, or wet insulation, is a symptom of a major problem below the surface of the insulation.
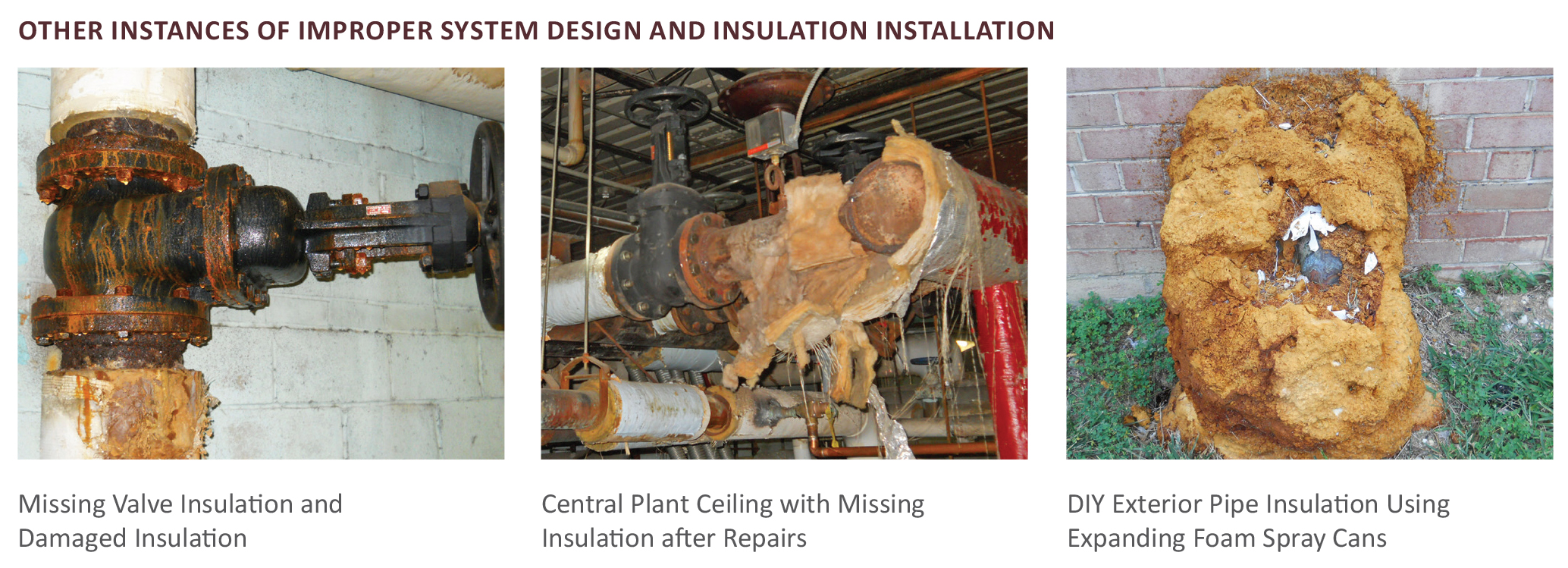
Incorrect installation creates the opportunity for condensation problems to start as soon as the insulation is installed, especially at the insulation joints. This problem is aggravated by building maintenance and mechanical contractors making “emergency repairs,” or by common repairs that leave pipe insulation missing or improperly reinstalled. Thousands, if not millions, of pipes and valves, are left uninsulated in many buildings. If a mechanical contractor fails to hire a professional insulation subcontractor, then the installation is often incomplete. End-user building engineers often focus on replacement chillers, or domestic water-heating systems, and therefore overlook the issue of uninsulated pipes for chilled water, domestic water heating, steam piping, etc.
Building owners and specifiers should be interested in avoiding the liability of increased energy costs, mold growth, and the possibility of catastrophic failure of a building’s piping systems. A relatively minor increase in the wetness of pipe insulation of, even 1%, can reduce the effectiveness of the insulation thermal efficiency by 7.5%. This statistic was confirmed by studies by ASHRAE, the Environmental Protection Agency, and the Department of Energy.
Water is a superior product for transmitting heat or cold, and transfers BTUs several times faster than air. Some engineering studies have shown that water will transmit heat or cold 10 to 30 times faster than room air. While water is a great delivery vehicle for heating and cooling buildings, it is often utilized based on the assumption that it is transported in properly insulated pipes. “Properly insulated” implies the selection of the right insulation product, installed per the manufacturer’s instructions, and then maintained by building engineers and contractors. If any one of these steps is not followed, then one cannot expect the HVAC system and its pipes to perform as expected over the life of the building. Since central HVAC systems are expected to perform for 20, 30, 40, and even 50 years, it becomes critical that the chilled-water pipe installation is properly selected, installed, and maintained.
Infrared cameras are useful tools to look for heat loss and to identify thermal differences due to wet insulation. Infrared camera fly-overs are sometimes used to find leaking underground pipes. Infrared cameras can show images in infrared, black-and-white, or combined (combined is referred to as fusion) wet insulation in roofs and pipe insulation. Advanced infrared camera software can also show the temperatures of the pipe and equipment photographed for inclusion in reports and recommendations.
Proper chilled-water pipe insulation in new construction is also cheaper to install initially than it is to replace after the building is built. A small increase in the cost of a properly specified and installed chilled-water pipe insulation (a capital investment) is nothing compared to spending 3 or 4 times the cost to replace the incorrect pipe insulation later (an operating expense).
Another important design consideration is allowing enough space for the chilled-water pipes with the proper insulation thickness. This allowance of pipe space is important for new construction and even more important later if the pipe and insulation needs to be replaced or installed after the building is built and operating. A little extra consideration on the design makes the installed cost and life-cycle cost lower for a chilled-water piping system.
Proper specification and installation of chilled-water pipe insulation is a solid investment in a building to reduce its lifetime energy costs, reduce operation and maintenance costs, and avoid future risks and even liability for all parties involved. Proper pipe insulation reduces the total cost of ownership of mechanical systems, and thereby reduces their life-cycle costs.