Corrosion Under Insulation: Differences in Gel-Coating Technology
Corrosion under insulation (CUI) of steel operating equipment and piping is a significant issue in the ammonia refrigeration, chilled water, chemical, and petroleum industries. A systems approach to CUI includes the correct material selection and design of the jacketing, insulation, and coating. This approach will help prevent CUI, but many corrosion engineers would agree that electrolytes will eventually find their way into even the best system. Selecting the right coating is extremely important, as the CUI coating is the last line of defense for keeping the electrolyte from the metal surface, which would cause corrosion.
Historically, many different types of products have been used to prevent CUI. One of the most common is a synthetic fabric impregnated with petroleum jelly, which is spiral wrapped around bare piping prior to the installation of the insulation. Known as “grease tapes,” these products do not typically offer long-term performance and can add to the overall insulation system cost by requiring insulation with a larger inside diameter to cover the tape. These tapes are inexpensive and fairly easy to apply, but do not provide long-term performance (See Figure 1).
There are numerous paints and coatings available using silicon and epoxy technologies. Some are available on new pipe and some require multiple coatings. When used in retrofit applications, they require a degree of surface preparation of the existing pipe, which adds significant cost and time to project completion. Although more effective than grease tapes, paints and epoxies must be installed with great care to prevent damage to the surface; in retrofit applications, they often require the system to be shut down to be installed.
Another option is gel-type pipe coatings, which have gained in popularity over the last few years in the food process industry due to their high-quality performance and ease of application.
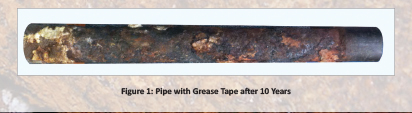
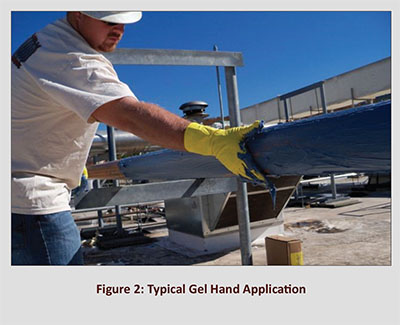
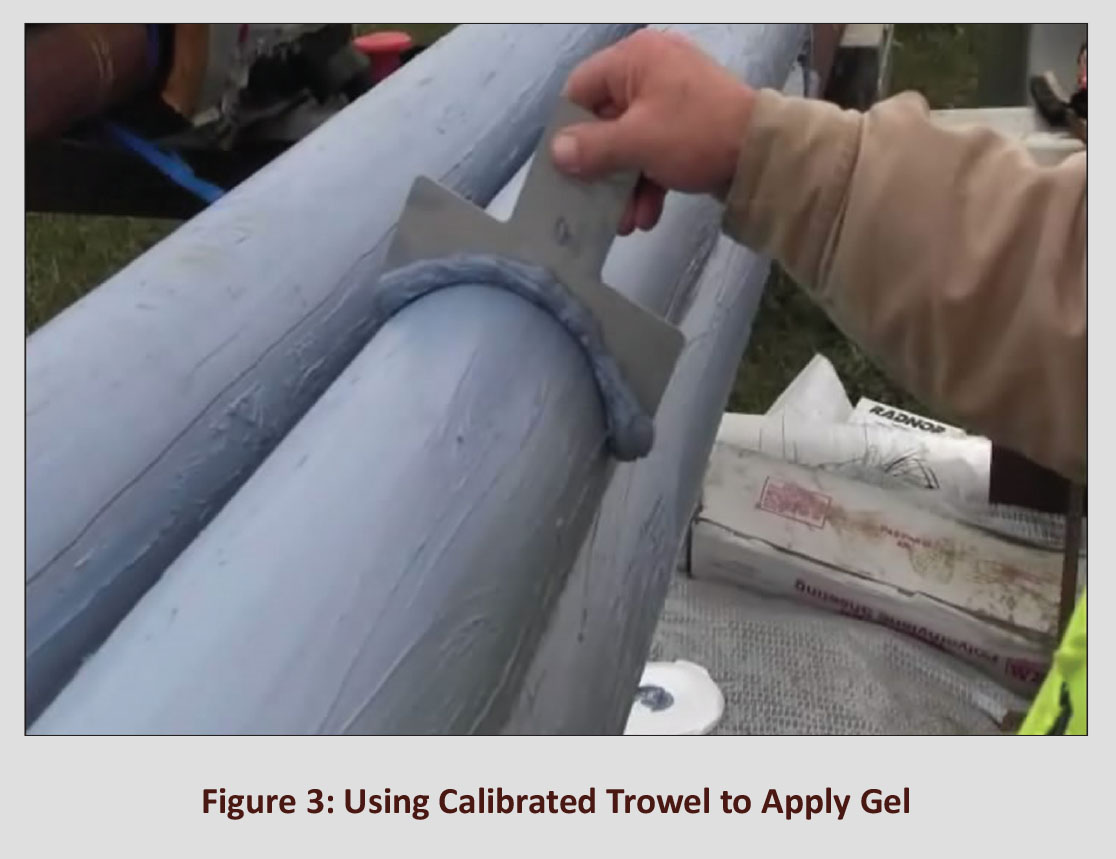
Ease of Gel Application
When applying gel coatings on existing piping, surface preparation is generally limited to removal of loose scale or rust using a wire brush. Paints and epoxies, however, typically
require removal of all scale and rust down to bare metal. Gel coatings are typically applied by hand since only as much gel should be applied as can be covered with insulation in the same day. The gels are applied at 25–30 mil thickness. One manufacturer offers stainless steel trowels in the most common pipe sizes that are calibrated to meter the proper amount of gel onto the pipe surface. Gels can also be applied using a brush, or for bigger pipes and vessels, may also be sprayed. See Figures 2, 3, and 4 for examples of these application techniques.
Pipe gel coatings can generally be split into 2 categories: Reactive Gel (RG) technology and Synthetic Petroleum Hydrocarbons with Thickeners (SPHT). There are significant differences in these types of products, which are made using different technologies. They are not the same type of technology, do not have the same performance characteristics, and have not been put through the same laboratory testing and field application trials.
Technology
SPHT products are typically used as gear and chain-grease type lubricants; they are not commonly used as a CUI coating. RG products, on the other hand, are specially formulated and patented anti-corrosion products that are primarily designed to be used in CUI applications. RG products have the ability to form a mineralization layer as an integral part of the surface of the pipe; this prevents undercutting where moisture can get under the coating and begin the corrosion process.
Performance Characteristics
A CUI coating needs to have various properties in order to be successful at mitigating corrosion. A few basic characteristics of a good CUI coating are thermal stability, the ability
to resist water wash off, and the ability to protect the substrate from corrosion.
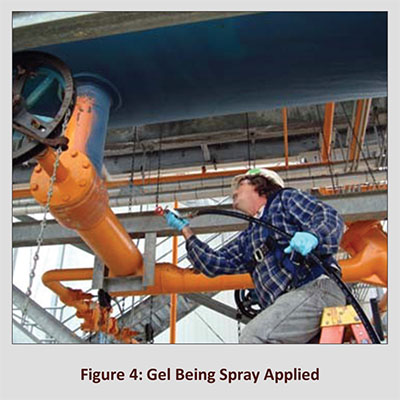
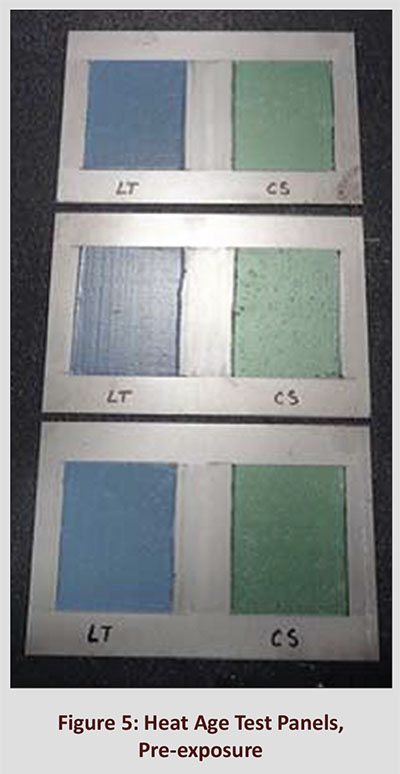
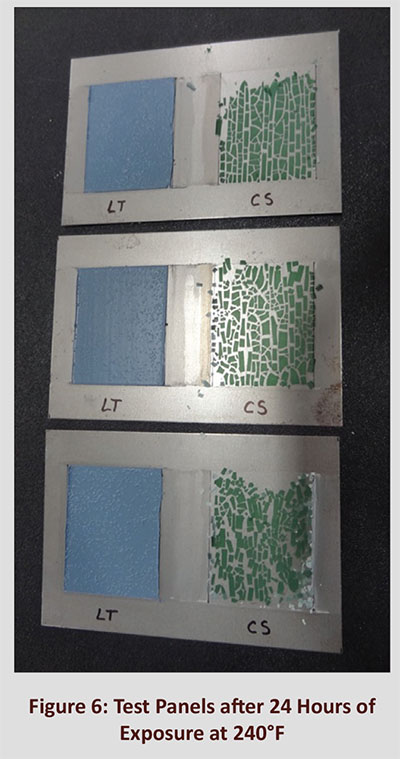
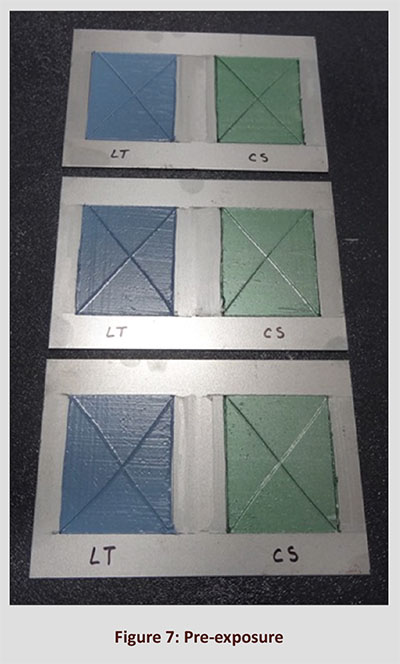
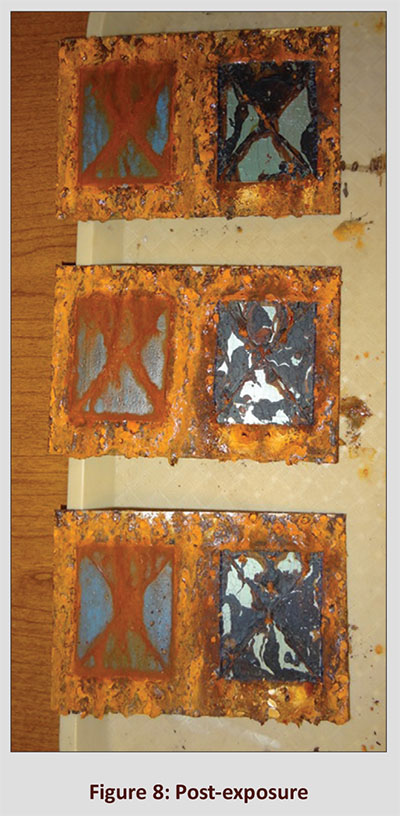
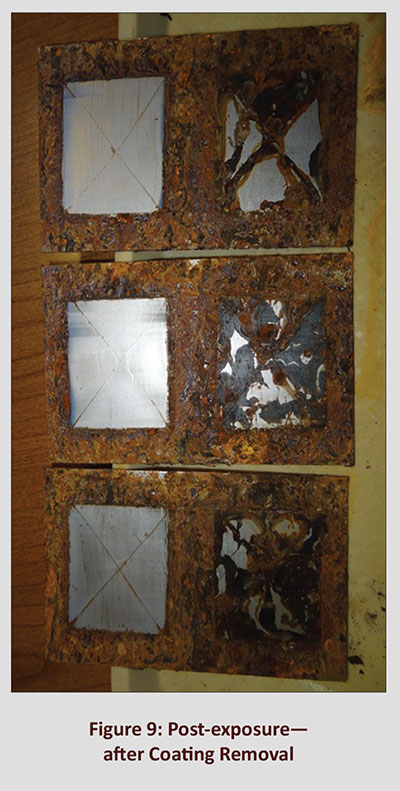
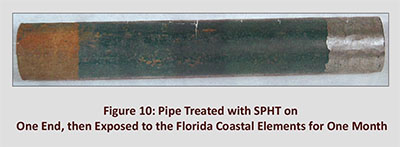
Thermal Stability: SPHT versus RG
- An independent lab tested both types of products at 240°F.1
- This test was conducted on cold-rolled steel (CRS) panels with the product applied at 25–27 mils thick (within the manufacturer’s recommended application thickness
range). Figures 5 and 6 show the test panels before and after 24 hours at 240°F, respectively. Figure 6 shows the degradation of the SPHT (on the right) while the RG (on the left) was
shown to have little to no change in physical appearance.
Water Wash-Off Resistance:
SPHT versus RG
- SPHT can be cleaned up using dishwashing liquid and water.
- RG is formulated to resist moisture/water and is designed to be cleaned up with a citrus-based cleaner.
Specific Gravity (The ratio of the density of a substance to the density of a standard, usually water for a liquid or solid.)
- Water = 1.00
- Typical SPHT = 0.85–0.95.
- Typical Reactive Gel = 0.98–1.08
- Because the SPHT product has a much lower specific gravity than RG, it will be much less resistant to water wash off.
Anti-Corrosion Testing
- ASTM B-117 is the most effective test in assessing the laboratory performance of anti-corrosion coatings and is used by corrosion engineers worldwide to compare product
performance.
An independent lab tested both RG and SPHT side by side at a thickness of 25–27 mil with an “X” scribe for 504 hours.2 You can see the results in Figures 7, 8, and 9.
An “X” is commonly added to this type of test to show resistance (or lack of resistance) to edge undercutting.
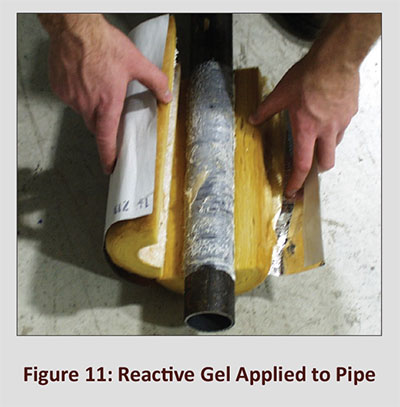
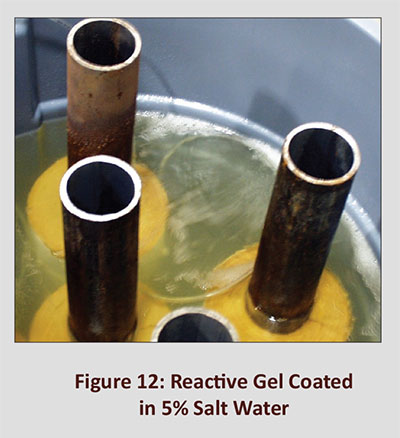
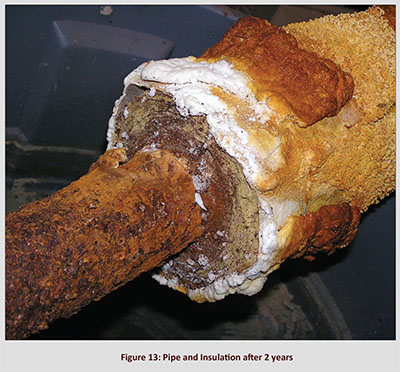
Actual Field Performance of Gel Products
SPHT
- A leading manufacturer of SPHT says that the corrosion properties have been previously verified by exposing a pipe to the Florida coastal elements for 1 month, and no
corrosion formed (Figure 10). - SPHT products have no documented record of long-term success in mitigating corrosion in general or CUI specifically.
RG
- RG has been tested in a salt-water immersion test where pipes were coated, covered with fiberglass insulation, and submerged in 5% aerated salt water for 2 years (Figures 11,
12, 13, and 14). As can be seen in the photos, the pipe was corroded except for the area coated with RG, which was corrosion free. - In addition, RG technology has 40 years of performance history in stopping corrosion in the auto industry and on U.S. Navy vessels in high corrosive environments. RG
technology also has over 10 years of specific experience in mitigating CUI in the food and beverage industry as well as the oil industry on the Alaskan North Slope.
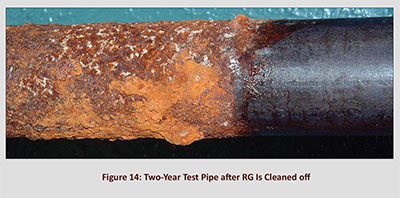
Conclusion
Lab testing shows that there is a significant difference between RG technology and SPHT in thermal stability, resistance to water wash off, and anti-corrosion properties. In addition,
RG technology has significantly longer field experience in various applications and significant direct experience in CUI applications.
In ammonia refrigeration and other very low-temperature applications, where system integrity and worker safety are important considerations, engineers will need to closely evaluate the
above factors in choosing the proper gel technology to use.
References
1. Intertek Report No.: 101276703GRR-001c, September 27th, 2013
2. Intertek Report No.: 101276703GRR-001b, September 27th, 2013