Get Your Mechanical Insulation Ready for Winter
For many individuals, preparing their homes for
colder winter weather is an annual event that often includes a variety of
maintenance and winter–proofing activities. There are 2 basic objectives for
preparing a house for winter: make the house more energy efficient, and ensure
it is comfortable during the cold winter months. For a multi–story high–rise, a
commercial building, or an institutional building, the objectives are nearly
the same: make the building more energy efficient and more comfortable for the
occupants.
Unfortunately, the inspection
and maintenance of mechanical insulation is often neglected, leading to both
energy waste and discomfort for building occupants. While it is important to
maintain a mechanical insulation inspection plan year–round, it is particularly
important in the winter, when the temperature drops and there is an increased
chance for high wind gusts and other potentially damaging weather occurrences.
To appreciate the importance of
preparing a building’s insulation for winter, it is useful to consider exactly
what mechanical insulation accomplishes for hot service pipe and equipment. For
example, 2 to 3 inches of conventional pipe insulation on a 380°F steam pipe
reduces heat loss by 93% to 95%. That is the equivalent of reducing heat loss
to approximately 15 to 20 times less than an uninsulated pipe. Thus, relatively
small areas of bare pipe surface, or pipe surface with damaged insulation, can
result in enormous heat losses in a boiler room, mechanical room, or pipe
chases in a building. These heat losses result in energy waste that leads to
financial loss from money spent on extra fuel; excess greenhouse gas emissions;
and high air temperatures in boiler rooms, mechanical rooms, and utility
tunnels. With such clear benefits—or losses—in the balance, it makes sense to
take steps to prepare for winter.
First Step: Insulation Survey
Consider a
dormitory or classroom building at a university and include mechanical
insulation in the list of activities for winterizing the building. Where does
one start? For the purposes of this discussion, assume that the campus has a
central steam plant, with tunnels carrying the steam to each building. Each
building, in turn, has its own mechanical room and steam distribution system.
In such a case, the steam for
heating has been shut down for approximately 6 months over the late spring,
summer, and early fall. After this hiatus, an inspector is likely to find
missing insulation on gate valves, flanges, pressure relief valves, and other
pipe components. Additionally, one might find that some of the straight pipe
insulation has been damaged if other maintenance workers have used the
insulated pipes as stepping pads to gain access to pipes or wires located
higher in the mechanical room. If removable/reusable blankets have been used to
insulate the components, some of those may be laying on the floor, draped over
a pipe, or simply missing. Duct insulation may likewise have been stepped on
and crushed.
Inspectors should first make a
list of the damaged or missing mechanical insulation sections. At each site,
this might include the location of the deficient insulation; size of the pipe
or duct; system description (such as hot air supply, hot steam supply, etc.);
type and thickness of insulation on adjacent pipe; extent of missing or damaged
insulation; and any other relevant information. With this information, an
inspector may use what he or she learned from the National Insulation Association’s
(NIA’s) Insulation Energy Appraisal Program (IEAP), if applicable, to generate
an estimate of the energy wasted by ignoring the problems, the cost of that
wasted energy, and the excess carbon dioxide generated from emissions (see
sidebar on the IEAP on page 8).
Setting Priorities
If insulation
needs to be replaced or repaired, the building owner will have to pay for new
materials and labor costs. Going back to the university example, if the campus
Facilities Manager or Maintenance Manager has been properly educated on the
value of mechanical insulation, he or she may generate work orders to get all
the deficiencies corrected before the boilers are fired up for the fall. While
this is the ideal scenario, it is often not the case.
One way to encourage building
owners to maintain mechanical insulation is to perform a mechanical insulation
survey to estimate both the energy saved and the cost of correcting the
mechanical insulation problems. Typically, the pay–back period will be less
than 4 years and, in the case of 380°F (or hotter) steam systems, it will
probably be closer to 6 months. Making building owners aware of the uniquely short payback period of insulation may help place
repair and replacement of damaged or missing insulation on a high–priority
list. Short of shutting the building windows and doors, almost no other measure
has a shorter energy payback. In regard to the value of energy savings in most
institutional buildings, fixing missing or damaged mechanical insulation on hot
service pipes and ducts is the easiest measure, with the most significant
rewards.
In arguing the case for winterizing a building by repairing or replacing
damaged or missing mechanical insulation, it may also be useful to talk about
the thermal comfort of the building occupants. Cold buildings may lead to
complaints, which can cause difficulties for management as well as the
facilities and maintenance staff. After all, the main purpose of heating many
commercial buildings is to keep the occupants comfortable. In other applications,
heating can be a health and safety issue—consider, for example, a mechanical
room with a 120°F air temperature, along with hot steel surfaces. This is an
unsafe work environment for all maintenance craft laborers due to heat stress
and the danger of burn injuries. Building owners also must consider whether
they are up to date with current energy codes. If insulation is missing or
damaged, or the codes have changed, the building may no longer be compliant.
Executing the Work
It is important to remember that one of the reasons
for missing mechanical insulation is that mechanical maintenance personnel may
have removed it to do their work (such as replacing seals in pumps and valves,
replacing gaskets in flange pairs, draining strainers, etc.). To prevent damage
to newly installed insulation, all mechanical maintenance work scheduled for
the fall should be completed first, and the heating system should be tested for
leaks. All mechanical insulation work should be coordinated with the mechanical
maintenance crew to eliminate the possibility of one project interfering with
another. It is advisable to write a checklist for the insulation work and
establish an insulation maintenance schedule. Finally, to keep matters in
perspective, it is recommended to have an estimate of energy savings, insulator
labor cost, and insulation material cost for the proposed work.
After Finishing the Winterizing Work
After the insulators have finished the work of
repairing or replacing damaged or missing insulation, a staff person from the
facilities department should conduct a visual inspection using a checklist. It
is also advisable to turn on the boiler and measure the room’s air temperature
after several hours to verify that it is within reasonable limits. If it is
not, there may still be hot, bare surfaces on the heating system pipes. Lastly,
a member of the maintenance staff should write a final report to document and
justify the work that has been done, as well as to lay the groundwork for doing
the same evaluation a year later. While, ideally, no mechanical insulation will
need to be repaired or replaced the following year, that may be the case for
some facilities.
Preparing for the Summer Cooling Season in Early
Spring
Hopefully, after the Facilities/Maintenance Manager
has successfully prepared a building’s insulation system for winter, the
building owner will be on board with following the same preparation in the
spring for the cooling system. The process starts with evaluating the chiller
insulation and the chilled water pipe insulation. The incentive to do this is
not only to prevent energy waste and ensure thermal comfort, but also to
prevent water vapor condensation.
Before long, it will be time to
repeat the cycle once again for winter.
SIDEBAR
Energy Audits Can Save Money
One
of the best ways to fully understand the benefits of fixing missing or damaged
insulation is to do an insulation energy appraisal. NIA offers an Insulation
Energy Appraisal Program (IEAP), which can help insulators learn the skills
they need to complete these appraisals. The IEAP program consists of a 2–day
course that teaches students how to determine the optimal insulation thickness
and corresponding energy and dollar savings for a project. The program was
designed to teach students the necessary information to give facility/energy
managers a better understanding of the true dollar and performance value of
their insulated systems. To give facility managers the most accurate
information, students will gain skills in the following areas:
- Conducting a facility walk–through
- Interviewing customers
- Using the 3E Plus® version 4.0 software
- Determining the amount of greenhouse gases saved
through the use of insulation - Analyzing and completing the appraisal spreadsheet
- Completing and presenting a final customer report
Students
who pass the course exam—certified by the National Inspection Testing
Certification Corporation—will become Certified Insulation Energy Appraisers.
The certification will be valid for 3 years, after which the individual must
recertify. It is an invaluable distinction that can help give insulators a
competitive edge and help grow their business.
For
more information, visit www.insulation.org/training or email training@insulation.org.
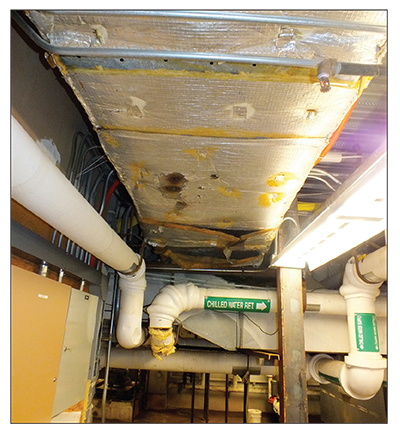
As this photo shows, some of the duct wrap insulation on the underside of this duct has become damaged and/or detached from the duct. This insulation should either be repaired or replaced in preparation for the winter heating season.
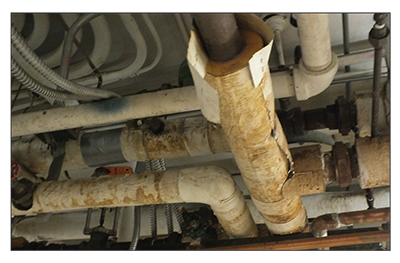
In this application, some pipe insulation is missing and needs to be replaced before firing up the boilers for winter. Some of the remaining pipe insulation clearly needs to be either replaced or repaired. Replacement with new material may be quicker and easier than trying to repair the old insulation.
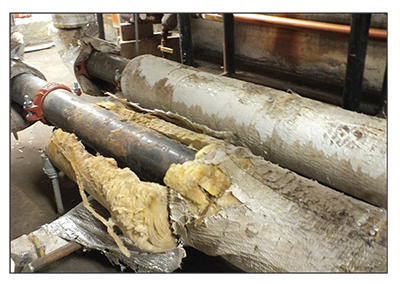
Most insulation professionals have seen pipe insulation damaged by foot traffic. These pipes are located close to ground level and have a high likelihood of being stepped on, resulting in damaged insulation. This damaged insulation should be replaced by new material before firing the boilers for the winter. It some cases, it may be prudent to use a hard, high–compressive strength insulation that can better withstand foot–traffic abuse.

This bare gate valve in a steam tunnel at a university results in excessive heat loss and high air temperatures in the tunnels. It should be insulated with either conventional insulation or with a removable/reusable insulation blanket as part of the process of preparing campus buildings for winter.

Preparing a spreadsheet such as the one above that summarizes the value of the energy savings, the simple payback, and the annual tons of greenhouse gas emissions reduction will help a facilities department get funding for their insulation project. With a simple payback of only 6 months (typical for a steam heating system with 380°F steam), the case for doing this maintenance work on the pipe insulation is compelling. (Note: 3E Plus® was used to calculate the heat flux values, not shown on this summary table).

On components such as this pressure regulator on a steam pipe, it may be prudent to use a removable/reusable insulation blanket. Mechanics may have removed this blanket assembly to perform necessary maintenance. However, it must be reinstalled by a skilled, knowledgeable insulator for it to insulate properly. Autumn is the best time to accomplish this.

This strainer and its connecting flanges should be insulated, and this work should be accomplished prior to the start of the heating season. Likewise, the butterfly valve to its right should be insulated. Leaving these 2 components bare will result in significant energy waste during the heating season and will contribute to a high–temperature boiler or mechanical room.

Every repaired pipe insulation project is not necessarily going to look this good. In this application, the strainer should be insulated, perhaps with removable/reusable insulation blankets, as well as portions of the 2 steam pressure regulators. It would also be beneficial to insulate the gate valve bonnets and steps, since those result in exposure of considerable amounts of bare steel that lose a great deal of heat.