New HVAC Technology Emerges: VRF/VRV Systems
A new kind of HVAC system is emerging in the United States commercial building space conditioning market. This new system utilizes variable refrigerant flow (VRF) or variable refrigerant volume (VRV) technology and uses an evolved heat-pump technology with heat recovery systems and sub-cooling built in, which increases effectiveness and efficiency. The use of this evolved technology makes these systems a good option for certain kinds of commercial construction projects that require high levels of flexibility when it comes to occupant comfort or for retrofit projects. VRF/VRV systems require slightly different considerations for completion of the insulation portion of the project, and include challenges that mechanical insulation contractors will have to overcome. There are many considerations that are important when designing the project, selecting the insulation materials and methods, estimating the project, buying the materials, and planning labor requirements.
Multi-type ductless split systems and VRF/VRV systems have been around for almost 3 decades, but they are new to the U.S. HVAC market. As American engineers become familiar with the technology, and especially as they learn of its energy-efficiency advantages, they may become a more popular option. Market forecasts predict the growth of these kinds of HVAC systems to be as much as 230% from 2013 through 2020. This means more mechanical insulation contractors will be asked to provide pricing and insulation services for these systems as they appear on projects.
What Are They?
A quick review of air-conditioning principles might be useful in describing multi-type ductless split systems and VRF/VRV technology—the most basic principle being that air conditioning removes heat from the space to be cooled by pushing refrigerant through a cycle. HVAC systems are based on the fluid dynamics that when a refrigerant expands, it becomes cooler; and when it is compressed, it becomes warmer.
Changing phases from fluid to gas, or from gas to a fluid, adds to the cooling/warming effect. The cycle is comprised of 4 elements common to all HVAC systems: a compressor, a condensing unit, a metering device (or expansion valve), and an evaporator or heat sink.
A multi-type air-conditioning system operates on the same principles as a split-type air-conditioning system, however in this case there are multiple evaporator units—or fan-coil units—connected to 1 external condensing unit. These simple systems were designed mainly for small to medium commercial applications where the installation of ductwork was either too expensive, or aesthetically unacceptable.
The 2-pipe, small-bore refrigerant piping system, which connects each indoor fan coil and the outdoor unit(s) requires much less space and is easier to install than ducting associated with other types of systems. These systems are 2-pipe systems, like classic split-system heat pumps. Both pipelines need to be insulated to accommodate the reversal of the refrigerant flow and the pipe service temperature as the system changes from heating to cooling or cooling to heating.
The term VRF or VRV refers to the ability of the system to control the amount of refrigerant flowing to each of the evaporators, enabling the use of many evaporators of differing capacities and configurations, individualized comfort control, simultaneous heating and cooling in different zones, and heat recovery from 1 zone to another. Similar to ductless multi-split systems, which can also connect 1 outdoor section to several evaporators, VRF/VRV systems are different in one important respect. Unlike multi-split systems, which turn on and off depending on whether the room to be cooled is too warm or not warm enough, VRF/VRV systems constantly modulate the amount of refrigerant being sent to each evaporator. VRF/VRV flow systems with heat recovery (VRF/VRV-HR) capability can operate simultaneously in heating and/or cooling mode, enabling heat to be used rather than rejected as it would be in traditional heat pump systems. Most VRF/VRV systems are 3-pipe systems, with all 3 lines requiring insulation.
VRF/VRV systems are typically distributed systems—the outdoor unit is kept at a location such as the top of the building, and all the evaporator units are installed at various locations inside the building. Typically the refrigerant pipework (liquid and suction lines) is very long, running in several hundreds of feet in length for large multi-story buildings. This is different from typical split-system or package-unit HVAC systems that have short piping runs to an evaporator coil, and extensive duct runs to convey the cooled or warmed air throughout the occupied spaces.
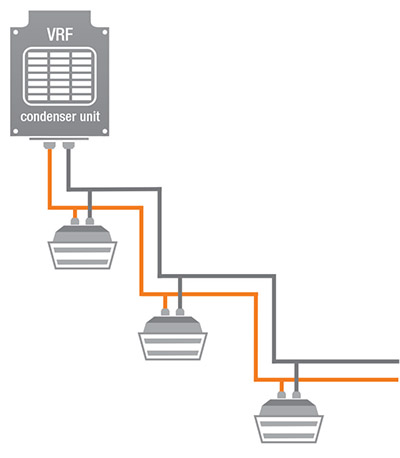
This change in thermal conveyance systems has the effect of turning an HVAC project into a major pipe insulation job with a small amount of duct, instead of a medium to large duct insulation project with a small amount of equipment-related piping to be insulated.
Benefits for Engineers and Facility Managers
The benefits of VRF/VRV systems include energy efficiency, design flexibility for architects and engineers, quiet operation, and the ability for individual users to control the temperature in their own areas. Another appealing feature is a centralized monitoring application that gives users control over the entire system from a single location or via the internet. While the technology is sophisticated, the systems are not complicated.
The main advantage of a VRF/VRV flow system is its ability to respond individually to fluctuations in space load conditions, allowing users to set the ambient temperature of each room as per his/her requirements. These systems also offer design flexibility—a single condensing unit can be connected to a wide range of indoor units of varying capacity (e.g., 0.5 to 4 tons ducted or ductless configurations such as ceiling recessed, wall-mounted, and floor console). There are also certain installation advantages; while chillers often require cranes for installation, VRF/VRV systems are lightweight and modular. The modular concept makes it easy to adapt the HVAC system if the space needs to be expanded or reconfigured. Additionally, a VRF/VRV system can start functioning even while the building is still being constructed—unlike large duct or chiller systems that cannot function until the construction project is completed.
Furthermore, because ductwork is only required for the ventilation system, it can be smaller than the ducting in standard ducted systems, thereby reducing building height and costs. In fact, a VRF/VRV system minimizes or often eliminates ductwork completely and associated duct leakage losses.
VRF/VRV systems are also particularly suitable for retrofitting historical buildings without disturbing the structure, or for older buildings with no air conditioning—if operable windows are present and meet code requirements for ventilation. As the condensing units are normally placed outdoors, a machine room is not necessary.
When compared to the single-split system, a VRF/VRV system reduces installation costs by about 30%. A VRF/VRV system also provides a reduction in copper tubing and wiring costs. Additionally, energy sub-metering with VRF/VRV systems is relatively simple and inexpensive; this is a very important feature in multi-tenant buildings if energy costs are charged explicitly to each tenant. VRF/VRV provides an alternative
and realistic choice to traditional central systems. It captures many of the features of chilled water systems, while incorporating the simplicity of direct exchange (DX) systems.
Where Are They Popular?
VRF/VRV systems are generally best suited to buildings with diverse, multiple zones requiring individual control, such as office buildings, hospitals, schools, or hotels. A VRF/VRV system does not compete well with rooftop systems in a large low-rise building such as a big box retail store. Currently available VRF/VRV systems have no integrated gas heating option, which hampers their acceptance in cold climates for buildings with substantial heating loads. New technologies to overcome this common objection are being studied and tested.
Insulation Contractor Business Opportunities and Obstacles
Due to the increased amount of piping that needs to be insulated on these systems, the insulation industry is looking at a change in building space conditioning technology that is both a significant opportunity, if addressed properly, or a significant loss to the industry, if ignored.
Perhaps the most significant difference in VRF/VRV systems is that they do not require duct systems, or require very limited duct systems. Thus, duct insulation work in these structures becomes minimal to nonexistent, eliminating the need for this kind of insulation work, which removes a common installation project and income opportunity for insulation contractors in most of these facilities.
However, the VRF/VRV installation presents new opportunities for an insulation contractor. Broadly speaking, there are 3 separate piping systems that are typical in buildings served by these systems that need to be insulated. This special need increases the income potential from a VRF/VRV project. These systems operate at temperatures more like true refrigeration systems, requiring the skill and detail associated with a proper insulation installation of a refrigeration-system project. It is prudent that insulation contractors recognize this characteristic, so that projects are estimated and bid correctly.
The Importance of Proper Installation
Due to the fact that this system may seem similar to residential air-conditioning systems, some mechanical contractors or other parties may try to perform the insulation of these systems without consulting or hiring an insulation contractor. Unfortunately, if they do not enlist the help of an experienced insulation contractor, there are several areas that may be left under-insulated, which can severely compromise the system.
The following shortcomings are common in installations that are not done by an experienced insulation contractor:
- Valves, fittings, and pipe support locations are left uninsulated;
- Insulation termination points are not properly sealed;
- Seams of butt-ends and longitudinal seams of insulation materials are left unsealed;
- Electrical “zip-ties” are used as anchoring and closure devices, causing compressed insulation materials that will fail; and
- Rooftop piping is improperly insulated for outdoor service.
The misconception that VRF/VRV systems do not require the services of an insulation contractor may prove to be a significant problem resulting in a loss of market share in many kinds of commercial HVAC installations, including offices, educational facilities, medical facilities, and light-production facilities, among others. If HVAC contractors perceive that these systems are just larger residential HVAC systems, and owners or designers do not challenge that assumption, insulation contractors may not be seen as necessary and thus, these systems may not be properly insulated, severely damaging long-term performance.
A somewhat similar set of circumstances occurred with traditional types of DX air-conditioning systems, both with duct and piping. If the misconception that these systems can be insulated by anyone persists, insulation contractors will lose the opportunity to provide a proposal for correct and effective insulation services, damaging the scope of the insulation market and leading to less effective and efficient systems. Mechanical insulation contractors will need to continue to represent to design professionals and owners that enlisting their labor is crucial to an effective insulation system. While the first impulse of designers and owners may be to look for corrective action through changes in material selections, the most common cause of failed applications is poor installation due to inexperience. The insulation industry has seen this before when mechanical contractors made it standard practice to self-perform, like in small commercial duct insulation jobs or large retail refrigeration system projects.
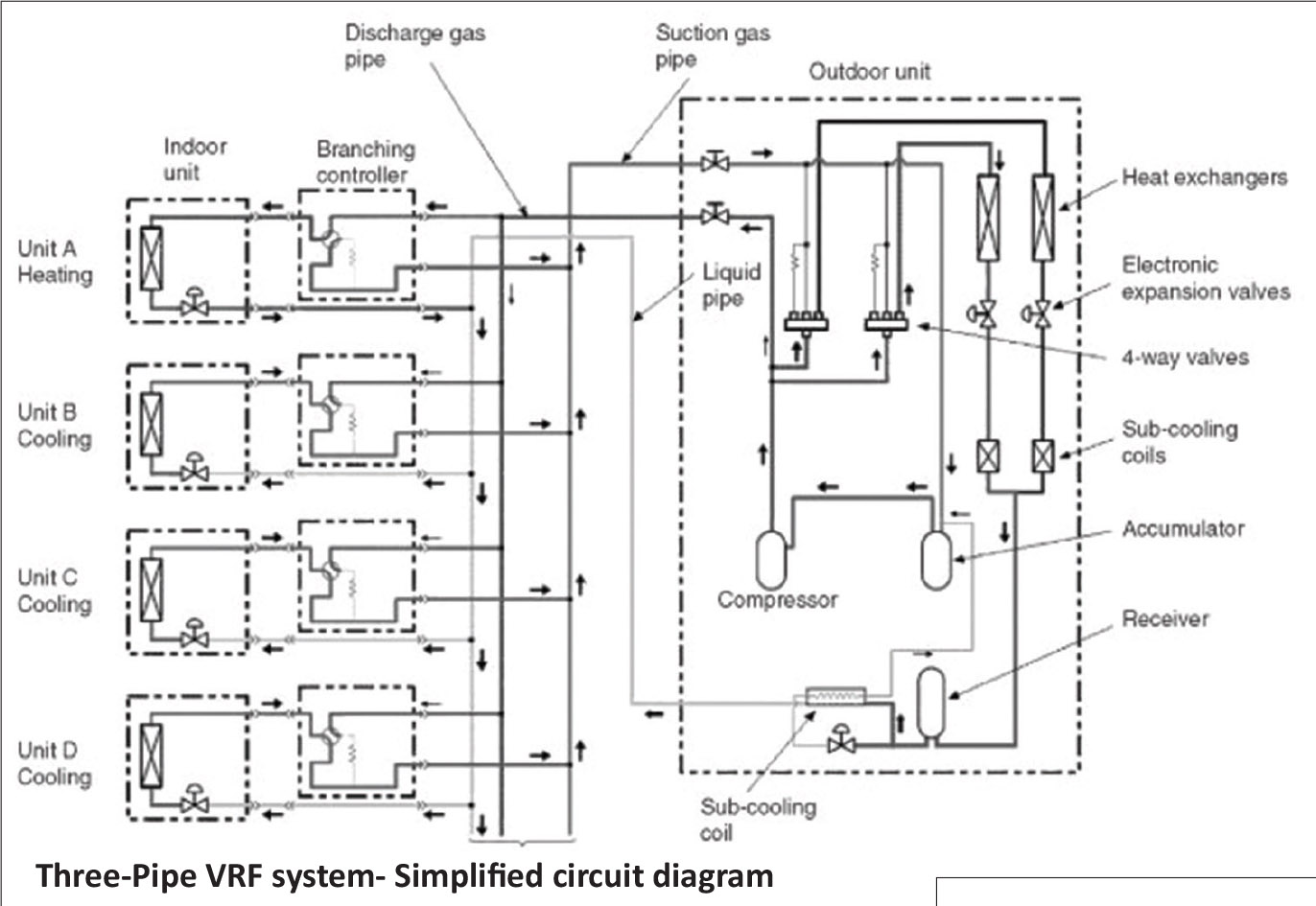
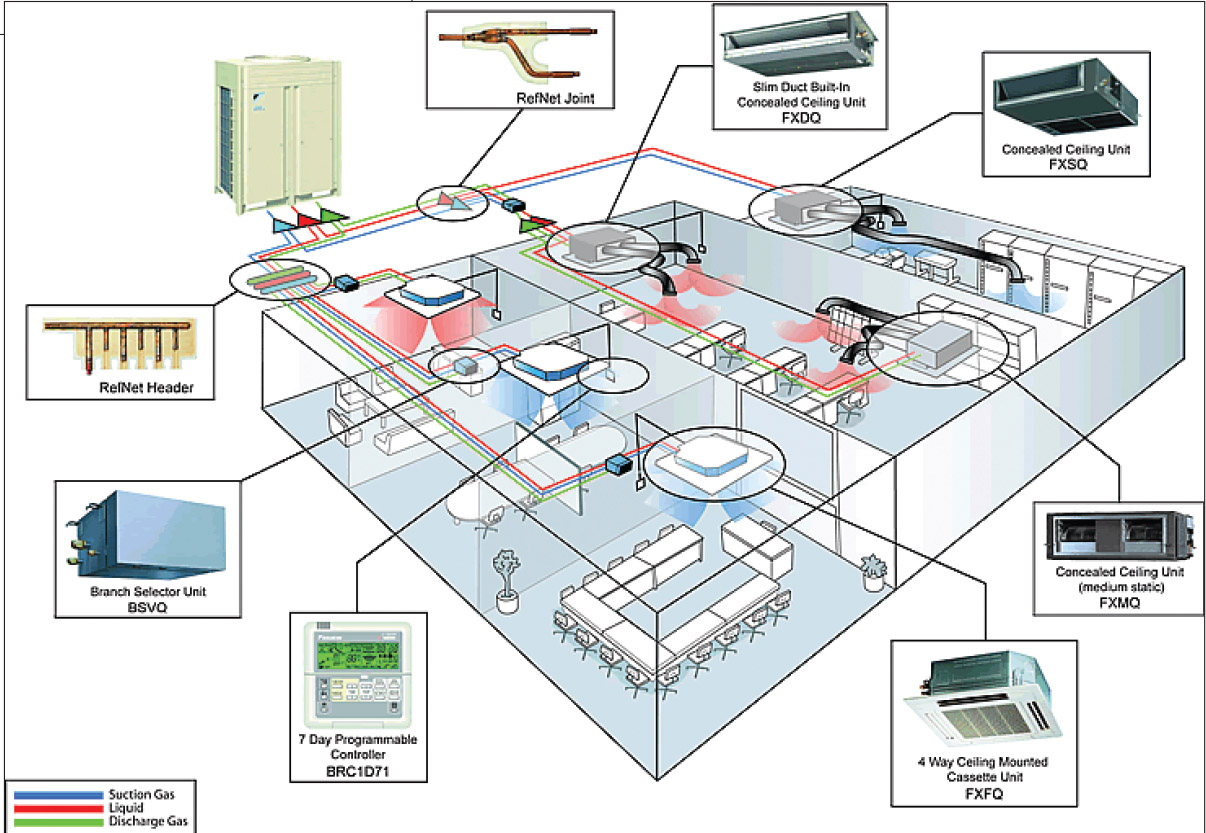
It is imperative that insulation contractors understand the complexities of these systems, and make the design and ownership communities aware of why the insulation installation needs to be completed by a competent and well-trained insulation professional, as these 2 communities are crucial to affecting practices in new projects.
Insulation Installation Requirements and Challenges
Insulating the piping of these new systems delivers the same challenges as a dual-temperature piping system that circulates chilled water and high-temperature heating water, but with more severe extremes. In a typical dual-temperature piping system, the chilled water tends to be around 3840°F and the high-temperature heating water tends be around 190°F. VRF/VRV systems are designed to operate at temperatures from below freezing to +248°F. This range equates to the extremes of a retail food case refrigeration system to a low-pressure steam system that operates using the same piping system. Many producers of VRV/VRF systems are requiring insulation materials that have upper service temperatures of +248°F or hotter. One producers installation instructions, for example, require insulation that is rated for a continuous service temperature of 212°F or greater. This is critical, since many insulation contractors are unaware of this requirement, as are most mechanical contractors. Unfortunately in some cases, an HVAC contractor may or may not make the insulation contractor aware of this requirement until some portion of the material has been installed, requiring removal of the first insulation installation and forcing the contractor to reinsulate. It may also lead to the wrong material being purchased, requiring a return and repurchase.
Unique in HVAC, and more like refrigeration, the piping can be hot or cold depending on system operations for occupant comfort, and whether or not the fan-coil unit is running as an evaporator coil (cold) or a condenser coil (hot). Because sub-cooling is used in some VRF/VRV systems, the cold piping is below 40°F, sometimes below freezing, requiring installations as detailed as chilled water or even refrigeration installations to make the insulation last. Installation of the insulation needs to be treated like a true refrigeration system—completely insulated, including solenoid valves, unit connections, fittings, and pipe supports. The insulation system also needs to be thoroughly sealed so condensation and ice formation is not a problem when operating in the cooling mode.
Choosing the Right Materials
There is a selection of products at various prices—some specialized and some standard—that are appropriate for these systems. It is important, however, to ensure that the specialized materials that are appropriate for the required temperature ranges are also meeting other performance requirements, such as flammability properties. The material needs to be able to survive the warm operating temperatures as well as the conditions that come with refrigeration operating temperatures. Historically, that has been one of the biggest challenges insulation contractors have faced with dual-temp piping systems. The materials may not come in the range of sizes needed or may not come in a form that allows for productivity that other materials afford. Insulation contractors will need to do some comparison before selecting a product that can help them continue to be successful in performing this work profitably and cost effectively.
These systems typically have wall thicknesses of 3/4″, but they can be 1″ or 1½” by code or ASHRAE 90.1 standards—or even as thick as 2″ for condensation control in certain environments. Refrigerant liquid lines tend to be 3/8″ in diameter, and gas lines 5/8″ to 3/4″ in diameter. Recent system configurations include piping as small as 1/4″ outside diameter, and as large as 1 5/8″ in diameter, as systems increase in total capacity. Each manufacturer has its own proprietary design (2-pipe or 3-pipe system), but most use a 3-pipe system (liquid line, a hot gas line, and a suction line) and special valve arrangements. Control wiring follows the piping path and must be dealt with during the insulation system installation.
Piping
In these systems, refrigeration pipework up to 500 feet long is feasible. A difference from VRF/VRV systems’ early years is the amount of pipe that can be used in installations. The piping network was limited to approximately 1,000 feet in 2004; but in 2013, the typical piping network limit has increased to approximately 3,280 feet per condensing unit. Two major kinds of piping systems are being used in the installation of multi-split and VRF/VRV systems: copper and aluminum. Traditional already cleaned refrigerant (ACR) hard copper that is brazed together is still common and is insulated using traditional practices that have been used for many years. Aluminum is a newer piping material that was recently introduced to the industry for piping these systems. Aluminum piping for multi-split and VRF/VRV systems is sized like traditional ACR copper, but is connected with mechanical crimped connectors and fittings. These fittings present a challenge to the insulation contractor since they require special fabrication of covers that can accommodate them. The work is more comparable to insulating a threaded steel piping system than a brazed or sweat copper piping system.
In a VRV/VRF system, each indoor unit is branched off from the 3 pipes using solenoid valves and each of these pipes requires insulation of the proper inside diameter and thickness. Each of the solenoid valves also requires insulating, increasing the amount of fabrication of valve insulation significantly. A special type of wye fitting is used for the branch piping and that must also be insulated. These wye fittings present the insulator with a challenge in designing an effective method of covering them, and such a solution is still being sought. Fortunately, when this process is developed, it should become a fairly routine, production-type work that allows the project to keep pace.
Selecting Hangers and Pipe Supports
Choosing hangers or pipe supports presents the familiar challenge of a cost-effective and easy way to properly support insulated refrigeration piping without breaching the vapor sealing of the installation. Coordination with the mechanical contractor before the piping installation begins can save much time and expense in effectively providing a correct insulating support method. It is extremely important to understand which trade is going to be responsible for providing this part of the project, and working toward the best solution from the beginning. Fortunately, many of these piping systems are being run with strut and strut clamps as the pipe support and anchoring system. There are multiple products available that install easily with this kind of system. For other types of pipe support and anchoring methods, like clevis hangers or split-ring hangers, the job becomes a bit more tedious, but time-tested methods of high compressive strength materials, in combination with the main insulation material, can do the job effectively. Wood blocks do not fit the category of properly supporting a refrigeration pipe, and have been removed from the National Commercial and Industrial Insulation Standards manual.
Controlling Condensation
Vapor dams are important in these systems, since they do have a high chance of generating condensation, and are especially important in systems that are roof-mounted. There are a high number of these systems that are being mounted on the roofs of multistory buildings with many pipelines running into a single mechanical chase leading to the lower floors of the structure. Condensation can easily run down the line into the fan-coil unit in the building and flow out, damaging building contents, ceilings, drywall, carpets, etc.
Hand-in-hand with providing vapor dams as a way of controlling condensation or icing troubles is sufficient sealing of all joints, seams, and penetrations. Installations can be difficult and even present problems at valve access ports, valve operators, valve stems, test ports, strainer ports, and pipe terminations at the fan-coil units or at the condenser. Pipe support/anchoring is another tricky area, as discussed above. All these areas must be properly sealed against water vapor intrusion, as must all circumferential and longitudinal pipe insulation seams. It is also important to be sure the products being used are vapor retarder products. Quite often, weather barrier coatings that are breather coatings are mistaken for vapor barrier products. Fish-mouthing or voids in closure materials of all kinds can leave small entrances that water vapor finds fast and easily.
Preventing Corrosion
Corrosion of piping should also be considered when these piping systems are being insulated. As mentioned above, these piping systems are being installed in building chases in heavy multiples, and may be very hard to access for service after installation. Since the most severe operating condition will be when the system is in the cooling mode, this should be the primary consideration. Additionally, the heat of the system, when the piping is in the heating mode, is in the ideal temperature range commonly identified as the most prone to inducing corrosion under insulation. Avoiding the introduction of moisture that can help accelerate corrosion is critical in the installation of the insulation system. Sealing against water and water vapor intrusion needs exceptional attention, since many of these systems are roof-mounted and subject directly to whatever weather comes along, in addition to being highly susceptible to condensation troubles.
This same moisture can leach corrosive components out of insulation materials, and create a caustic solution that can accelerate corrosion under insulation. Pinholes can also leak refrigerant and cost the building owner significant expense in lost refrigerant, and there is also an expense associated with identifying the leaking areas, and repairing leaking pipes. Insulation contractors should evaluate the ability of a material to contribute to corrosion on piping. Materials that have been tested using a recognized ASTM test method for corrosion contribution, such as ASTM C692 or ASTM C1617, should be considered. Not all products have undergone this testing, but many have since there are a large number of applications that require the use of non-corrosive products.
VRF/VRV Technology in Sustainable Construction
Sustainable construction requirements will apply to many of these systems. The types of structures that VRF/VRV systems are frequently used in are all the most common types of structures to be subject to the requirements of some sustainable or green building program certification. It is prudent to expect that low-VOC emitting materials and materials that contribute to ecologically sound building practices or protocols will be heavily in demand for these systems. Identify methods and materials early that can perform in the tough refrigeration service environment, as well as in the same conditions as low-pressure steam, and will comply with the needs of a sustainable building certification program. Wrapping all of the above needs of system performance—while meeting the needs of a sustainable construction certification—into a completed mechanical insulation project on an HVAC piping system can be a real challenge, but can also yield substantial benefits.
Multi-type and VRF/VRV systems deliver a new set of challenges because of the unique operating conditions and systems they deliver. The mechanical insulation contracting community has solved these sorts of problems for years, and this challenge is no different. Methods and materials exist that have delivered solutions to previous challenges, and can help with this one. With cooperation, the insulation community can and will develop solutions that are effective and realistic for this new technology.