What Happens When Metal Building Insulation Becomes Wet?
“What happens when metal building insulation becomes wet?” is a question that gets asked frequently. In most cases, the next question is, “Does the insulation need to be replaced?” The most common response to both the original and the follow-up questions is, “It depends.” This article will walk through how insulation typically becomes wet on a job site, what to do if/when it becomes wet, and what preventative measures should be taken to reduce the chance of insulation becoming wet. (Editor’s Note: Next month, look for an article from NIA Consultant Ron King sharing solutions about wet insulation for mechanical insulation applications.)
How Did the Insulation Become Wet, and Was the Water Clean or Dirty?
Clean Water
The most common cause of wet insulation is a rainstorm. When metal building fiber glass insulation becomes wet from rain or another clean source of water, it can temporarily lose a substantial measure of its thermal resistance (R‑value). This is because the spaces created by the glass fiber filled with air will now be filled with water. Water is more conductive than air, which reduces the thermal value of the insulation. The water also may reduce the thickness of the insulation as the glass fibers are not able to support the weight of the water. Reduced thickness also will reduce the thermal value.
This loss of thermal performance may only be temporary. As soon as the water evaporates and the insulation becomes dry again, it can regain its original performance level. In addition, since fiber glass insulation does not absorb water, the insulation fibers will not be structurally altered or permanently affected in any other way, meaning it likely will return to its original listed thickness and thermal value. Insulation that has been installed and becomes wet with clean water like condensation or rainwater likely can be left in place and allowed to dry. Unused material can be unrolled and allowed to air dry.
For both situations, this drying process should take no longer than 24 hours to avoid establishing conditions that may encourage mold and mildew growth. As long as the insulation is allowed to dry from clean water exposure, and it retains its original thickness, it does not need to be replaced. Once dry, it should contain no more organic material or contaminants than insulation that was never wet. If the insulation does contain
contaminants or takes longer than 24 hours to dry, it should be replaced with new insulation.
Please note, however, that if the water infiltration and saturation is substantial enough to mat down the fiber glass insulation to a greatly reduced thickness, the insulation will not likely regain its original shape. If this occurs, and the insulation cannot be fully dried and/or cannot recover to its original thickness, it will not retain its original R-value and should be replaced with new insulation.
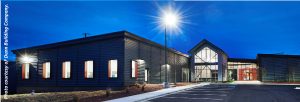
Dirty or Contaminated Water
Another common example of insulation becoming wet is if the insulation was resting on the ground at the job site during a storm. In this scenario, large puddles of contaminated water can form around the insulation. The contamination can be from dirt, mud, oil, etc. The issue with dirty and contaminated water is that when it evaporates, it can leave deposits of foreign materials or other contaminants in the insulation. These may decrease the R-value, and more importantly, also could give mold and/or mildew a food source and a place to propagate within the insulation. This growth and/or odor also may be transferred to connected building materials. For this reason, if the condition or contamination of the water is unknown, it is highly recommended that the insulation be removed, disposed of, and replaced with new insulation.
Therefore, any insulation that becomes wet with contaminated water should be replaced with new insulation.
How Do I Make Sure Insulation Does Not Become Wet on a Jobsite?
While there are never any guarantees when it comes to Mother Nature, there are ways to store and stage the insulation to ensure that the chances of it becoming wet are greatly minimized.
The best way to ensure that insulation does not get wet is to keep it covered and secured in
a trailer at the jobsite, as can be seen in the picture (below).
If having a trailer full of insulation at the jobsite is not an option, then store the insulation on pallets so that it may be raised high enough off the ground to be above any puddles forming or potential flooding from heavy rains. If possible, place the pallets of insulation on concrete or at the highest elevation on the jobsite.
Besides keeping the insulation off the ground, if there is a potential for rain in the forecast, placing tarps over the insulation can further reduce the chance it will become wet.
During installation, any insulation that will be left exposed at the end of the workday should be covered, especially if there is even the slightest chance of rain in the forecast. The small amount of time it takes to cover up exposed insulation at the end of the workday may be well worth the effort.