Keeping Outdoor Pipe Insulation Dry: Some New Ideas
In a perfect world, insulation on outdoor pipes would never get wet. But since we don’t live in a perfect world, above-ambient service pipe insulation often does become wet, even above ground. This can lead to major problems, such as:
- Increased heat loss on above-ambient service
- Corrosion Under Insulation (CUI) of the pipe surfaces
- Galvanic corrosion of metal jacketing
- Deteriorated insulation.
Those familiar with pipe insulation at industrial and electric power facilities know that insulation all too often becomes wet, primarily from precipitation. Yet in most applications, the insulation is covered with a protective jacket, usually one that can withstand weather such as rain, wind, and sunlight. So, if the insulation is covered with weather-resistant jacket and installed per the specification by a competent insulation contractor, why does pipe insulation get wet?
On above-ambient pipe systems, water gets into the insulation at jacket penetrations and joints, particularly (although not exclusively) on horizontal lines. Water from precipitation can also penetrate the insulation jacket system at pipe hangers, butt joints, and even lap joints. Gored elbow covers, in particular, provide multiple lap joints where water can enter. Damage from foot traffic or tears to the jacket can aggravate the problem by opening gaps for water ingress. Figures 1, 2, and 3 show typical problem areas that allow water from precipitation to get into horizontal pipe insulation.
What can be done about this problem? The NACE International guide SP01981 provides a number of effective and practical ideas to keep pipe and equipment insulation dry. However, this article introduces some additional ideas not considered in that or other previously published documents.
Sealing Lap and Butt Joints
Lap and butt joints are normally designed to shed water by overlapping the jacket. Overlapping lap joints on horizontal pipes and butt joints on vertical pipes are effective so long as the jacket does not become torn or separated or otherwise damaged by some external force, such as foot traffic. Furthermore, on horizontal lines, butt joints can be a problem since water can flow along the jacket surface and get into the insulation.
Designers often specify caulk and contractors install it. Even if that is the case, caulk does not last very long, as pointed out in the NACE guide. Furthermore, an inspector cannot see the caulk to know whether 1) it was installed at all, 2) it was installed correctly, or 3) it has cracked. The caulking can crack for several reasons other than foot traffic, one being thermal movement of the pipe within the insulation system. Furthermore, if the insulation is walked on and compresses, causing the jacket to become dented and deformed, the caulked seams will leak anyway.
This author’s solution: Use a weather-resistant laminate tape with a pressure sensitive adhesive (PSA), preferably 4 inches wide, to cover and seal both the lap and butt joints. When properly applied on cleaned jacket, such tape will seal these joints extremely tightly against water ingress. Furthermore, an inspector can see the tape so he can verify that it 1) was actually installed at all locations, 2) was installed correctly, and 3) is in acceptable condition. An inspector can do periodic inspections to look for tape failures and, if any are found, schedule them for repair. Figures 4 and 5 show an artist’s concept of how this might be done with standard aluminum jacket over horizontal pipe insulation. Figure 6 shows how the tape might be used to seal the multiple joints on a multi-gored aluminum elbow cover. This author recommends to overlap at least one butt joint, without using tape, every 20 lineal feet or so to allow for thermal movement of the jacket. This author also recommends that the metal bands be added after taping the joints has been completed so as not to disrupt the tape.
Taped lap and butt joints won’t make the jacket indestructible by foot traffic; however, the PSA tape will make it more leak resistant when it is walked on. Furthermore, if the designer specifies high compressive resistance insulation, the insulation system will be considerably more resistant to foot traffic damage.
Keeping Water Out of Pipe Hanger Penetrations
Pipe hangers, particularly on horizontal pipes, penetrate the jacket, providing an easy entrance point for rainwater. This may seem easy to fix: just put a lot of caulk in there. However, as with the jacket joints, the caulk becomes brittle over a few years—particularly with high pipe temperatures, which degrade the caulk even faster. When there is pipe movement, the leak-proof caulk seal simply breaks and then leaks. Pipe hangers are a major source of water entry into insulation, which can lead to the normal problems, including CUI.1
This author’s solution: Using standard aluminum jacket, make a conical rain shield as shown in Figures 7 and 8. First, to set the height of the shield above the hanger, a small rod clamp should be attached to the hanger rod at the appropriate distance above the hanger; the metal cone is then formed around the hanger rod; and finally the two edges are riveted together using a pop rivet gun. While Figure 8 shows some caulk applied to the small space between rod and the shield, and the caulk will crack over time,1 at least it is where an insulation maintenance person can see it, inspect it, and re-apply it as necessary.
The rain shield can be an effective solution. With strong winds, some rainwater may occasionally blow under the shield and get into the insulation, but it will be much better than having no rain shield at all. If shields become damaged, they are easy and inexpensive to repair or replace. Installed and maintained, rain shields should significantly reduce the quantity of rainwater entering the insulation through pipe hanger penetrations of the protective jacket. Note that if the pipe hangers are outside the insulation system, water leakage at the hangers is not a problem and rain shields are not needed.
Repairing Tears in the Jacket
The same laminate tape with PSA can also be used to repair tears in the jacket. Figure 9 shows such a tear in standard aluminum jacket on an outdoor insulated pipe. Figure 10 shows how this tear might be sealed with the laminate PSA tape using a very basic repair technique. An alternative repair technique, not pictured, would be to use a piece of laminate jacket that has either a PSA or sticky interior surface and has been cut to a size adequate to cover the tear in the jacket.
Conclusion
Pipe insulation in outdoor locations too often gets wet from precipitation, whether through lap and butt joints or pipe hangers that penetrate the jacket. Simple, inexpensive preventative measures are available, including using weatherproof laminate tape with a PSA on all joints. On existing hangers that penetrate the jacket, conical rain shields can be formed from standard aluminum jacket material and installed around the pipe hangers, a short distance above the hanger clamp, to effectively shed the rain.
The use of high compressive resistance insulation will make an insulation system more resistant to jacket damage from foot traffic. However, these ideas for keeping the insulation dry, combined with high compressive strength insulation, will result in a more durable system that will effectively keep most rainwater out of the insulation.
Reference
1. NACA International SP0198-10, “Standard Practice: Control of Corrosion Under Thermal Insulation and Fireproofing Materials—A Systems Approach.”
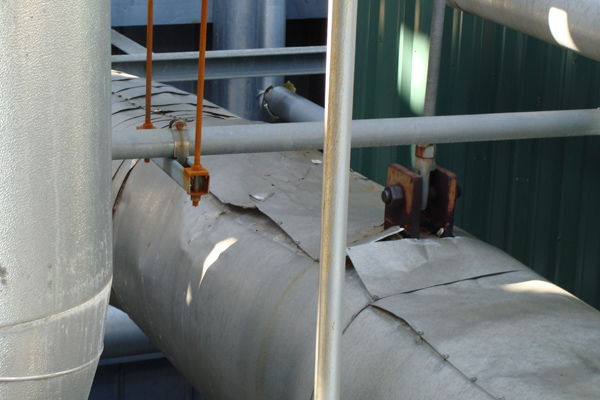
Horizontal pipe with aluminum jacketed pipe insulation. With some damage by foot traffic, it is apparent that water from precipitation gets into the insulation through opened lap joints on the straight pipe as well as the mitered elbow covering. There are also gaps around the hanger penetration that allow water to get into the insulation.
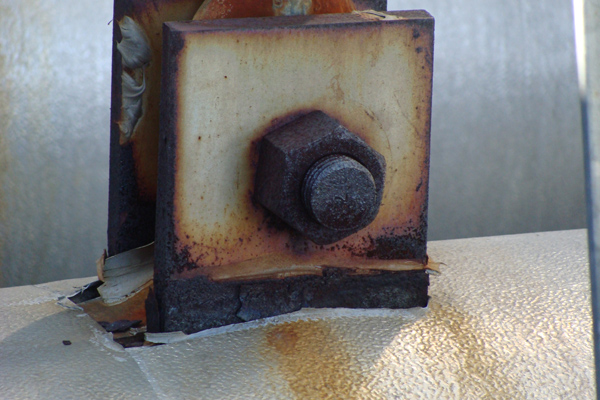
Close-up of a pipe hanger with deteriorated caulking, which is no longer effective in sealing this penetration from rainwater and melted snow. The corrosion also demonstrates one of the disadvantages of allowing this hanger to get wet.
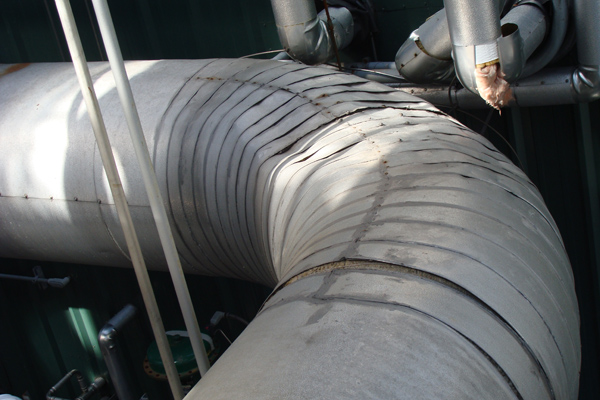
Mitered elbow on a horizontal, insulated, and aluminum jacketed pipe. The gaps in the overlapping metal gores allow water from precipitation to get into the insulation.

Horizontal pipe with aluminum jacket that is ready to be taped. In this case, the jacket butt joint can be left separated, without overlapping, since that seam will be taped. Furthermore, this increases the jacket coverage by several inches.

Aluminum jacket being taped with laminate, PSA tape with a release liner on the adhesive. I recommend 4-inch wide tape instead of the standard 3-inch—the wider tape will hold better and provide greater coverage.

Sealing a gored aluminum elbow cover with laminate, PSA tape. While a gored elbow cover is beautiful when first installed, the individual gores can eventually open up, allowing rainwater to get into the insulation. Using this tape to seal the joints can increases the life of the insulation system.
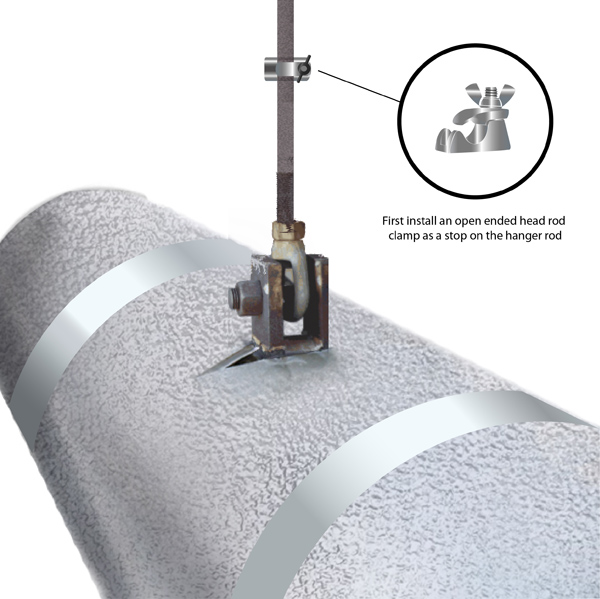
Pipe hanger with an open-ended Head Rod Clamp on the hanger rod. This will be used to secure a conical rain shield shown in Figure 8.
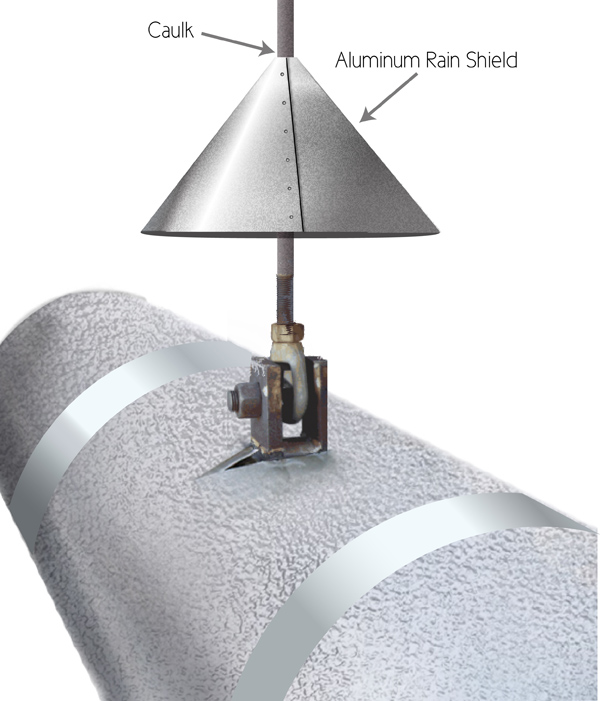
Conical rain shield installed on the hanger rod. This can be fabricated from aluminum jacket material and closed using either rivets or even the laminate PSA tape. A small amount of rubberized caulk should be applied between it and the hanger rod to prevent rainwater from running down the hanger rod, bypassing the rain shield, and getting into the insulation.