The Impact of High Natural Gas Prices on the Mechanical Insulation Industry
In the last half-year or so, there has been much publicity and concern expressed about increasing natural gas (NG) prices in the United States. There should be concern since energy experts agree that the demand for NG in North America now exceeds the domestic supply, resulting in a decrease in availability and an increase in price. What is bad news for society, however, can be an opportunity for others. If you are reading this article and work in the insulation industry, the chemical industry, an electrical utility, or other energy consuming industry, you no doubt deal with energy use and energy conservation. If you are prepared for the coming high NG prices, you will be in a better position to take advantage of the situation. That will be better for both you and your firm.
Since use of mechanical insulation is an extremely cost-effective means of conserving thermal energy resources, the market for both the materials and services should increase. Furthermore, since higher NG prices will favor coal-fired and nuclear-fueled electric power generation, there eventually should be new construction of both coal and nuclear power plants. In this article, I will discuss a few of the future opportunities for the mechanical insulation industry, as well as the negative impact of higher insulation manufacturing costs. So, before you get angry at your higher home heating costs this coming winter or angry at the higher gasoline pump costs, consider that higher NG prices represent a great opportunity for the insulation industry. You want to be prepared for this opportunity.
What’s Been Happening to NG Prices?
In June, Federal Reserve Chairman Allan Greenspan expressed concern about the negative impact of NG prices on the U.S. economy. President Bush likewise has expressed concern and is promoting an energy bill that will make it easier to explore for new NG supplies. High NG prices could, with a cold winter in the next few months, prove to be a major political and economic issue in the Unites States. Wellhead NG prices are now in the $4 to $5 per million Btu (MMBtu) range, which is historically high. From 1990 to 2000, wellhead prices of NG averaged $2.07 per MMBtu, according to energy consultant Jim Schretter. What has happened to cause this big increase in the price of NG?
The answer can be found in standard supply and demand theory: simply put, the demand increased and the supply decreased to the point that demand now significantly exceeds supply in North America and in the United States. The demand increased partly for the expected reasons of economic growth, new housing and commercial building construction, etc., in spite of reduced demand for NG from manufacturing. But, more importantly, demand increased due to the massive construction and operation of new electrical generating stations. These are primarily NG turbines and NG-powered cogeneration units. In the past four to five years, some 200,000 megawatts of new electrical generating capacity, using NG as fuel, has been added in the United States. This is greater than the combined capacity of all the nuclear power plants in the U.S. As a result, gas stocks in the United States are now very low, 38 percent below what they were in 2002 and 28 percent lower than the five-year average. Further, with demand exceeding supply for the U.S. and Canada running low on NG supplies as well, the United States will increasingly need to import NG from outside North America to meet demand.
The reasons for adding NG-powered generating stations, as opposed to coal or nuclear or hydro, are economic. The construction costs for coal-powered and for nuclear-powered steam electric generating stations are very high in comparison. Coal is a relatively cheap fuel, costing electric utilities only around $1.25 per million Btu, according the Department of Energy’s (DOE) Energy Information Administration (EIA). However, new Rule 5 of the Environmental Protection Agency’s (EPA’s) Clean Air Act requires the limiting stack emissions of Hazardous Air Pollutants such as fly ash, nitrogen oxides, and sulfur oxides to very low levels. To achieve this, expensive pollution control technologies must be implemented. Hence, the cost of constructing a new, state-of-the-art coal-fired station is now around $1,500 per kilowatt. So even though coal is cheap as a fuel, the construction cost for a new, EPA-compliant coal-fired power plant is high.
In the case of nuclear power, the cost of construction is similar, according to the Nuclear Energy Institute (NEI). NEI claims that the cost of nuclear plant construction will be about $1,400 per kilowatt for a two unit, 2,000 Megawatt, Westinghouse Advanced Pressurized Water Reactor (there is significant disagreement about this number; the Congressional Budget Office estimates $2,300 per kW, a value which NEI vociferously disputes). This NEI construction cost may be low enough to make it competitive with construction costs for a new EPA-compliant, coal-fired plant. In addition, nuclear fuel is inexpensive, and add to this the fact that most operating U.S. nuclear plants have had successful operating histories.
Hydroelectric generation requires large, available rivers with fish populations that won’t be adversely impacted by new dams. Such rivers aren’t available any longer in the U.S. (and perhaps had current environmental laws been in effect, they never would have been available). So, hydro is having a decreasing impact on the domestic electricity supply.
Then there is NG. A few years ago, when it was available to large-scale industrial users at about $2.50/MMBtu, and at the wellhead for about $2, it was a cheap fuel. Furthermore, with no air pollution controls required on a NG turbine unit and no need to construct high-pressure boilers and piping, a large NG plant can be constructed, so I have heard, for only about $600 per kilowatt. For an electric utility executive needing more generating capacity, a few years ago it was a "no brainer." Construct a NG turbine plant and use NG. It was clean and cheap so everyone was happy: the utilities, the customers, the environmentalists and the environmental regulators.
The following chart summarizes the relative costs per kW of NG turbine, coal-fired, and nuclear-powered electrical generating stations.
Estimated construction costs in dollars per kilowatt of generating capacity for NG fired turbine generators, coal-fired generators, nuclear plants per the Nuclear Energy Institute, and nuclear plants per the Congressional Budget Office projections.
Many of the utility decisions to construct new NG turbine generating stations were made when NG prices were around $2 per MMBtu. However, in the last three years or so, those prices have increased significantly, although with volatility. The graph below shows what has happened to those prices since 1990. The trend value in those prices increased slightly during the 1990s and then took a big jump in about the year 2000.
In a recent article from the Oil and Gas Journal called "Gas Spotlight" (Sept. 15, 2003), the author predicts that this year "The biggest price jump will likely occur in the fourth quarter, when wellhead prices are projects to be about $1/Mcf, 32% higher than 1 year earlier. Assuming normal weather, spot prices of $4.80 – $5.50/MMBtu range are expected for the rest of this year". The author quotes an energy analyst who predicted "an unprecedented $5/MMBtu for 2003." This depends somewhat on what the winter weather is like in the coming months. Recall that the winter of 2000-2001 was long and cold everywhere east of the Rocky Mountains; NG prices got as high as $10/MMBtu for a month or so that winter. The following winter, of 2001-2002, was extremely mild in most of the continental United States. As the graph (below, left) shows, NG prices that year dipped but still were greater than they were during the 1990s, averaging about $3/MMBtu.
Combined with what appear to be long-term structural changes in the North American supply and demand situation, it looks as if high NG prices may be here to stay. An article in the Sept. 29, 2003 issue of Oil and Gas Journal predicts NG prices will remain steady in a range of $4.50 to $5.00 / MMBtu through 2009 (in 2003 dollars). And that, of course, opens up exciting new opportunities for those who are in position, and prepared, to take advantage of those opportunities.
As a comparison, it’s worth noting how these NG prices compare to the highly publicized prices for crude oil. For example, Oklahoma crude has a fuel value of 141,116 Btu/gallon and a "barrel" of crude contains 42 gallons. Doing the arithmetic, that works out to almost $6 MMBtu / barrel. At $25 per barrel, the cost of oil by fuel value is $4.21/MMBtu; at $30 per barrel, that cost is $5.06/MMBtu. These prices, of course, don’t include refining and distribution costs. With the Organization of the Petroleum Exporting Countries (OPEC) keeping oil prices in that $25 to $30 per barrel price range, you can see that crude oil prices are only slightly less than NG prices, based on the fuel value.
Need for Increased Insulation Thicknesses
If the cost of energy increases, then certainly the demand should increase for mechanical insulation used to insulate things such as piping, equipment and ducts. Using 3E Plus® V3.2 to perform some optimum thickness evaluations, I conducted a couple of analyses using NG prices of $3.50 per MMBtu (i.e., an old, cheaper price) and then $5.50 per MMBtu (i.e., a new, higher price), a 57 percent price increase. Evaluating a flat surface operating at 600 degrees Fahrenheit (F) and keeping all other variables the same, the optimum thickness is 3 inches for the lower-priced NG and 4 inches for the higher-priced NG. Now, this probably is not going to cause existing facilities to call insulation contractors and add 1 inch of insulation over an existing 3 inches. However, in new construction, it provides the opportunity for using greater thicknesses from the start. And, for existing facilities, it gives the opportunity for contractors to conduct energy appraisals, per NIA’s Insulation Energy Appraisal Program (IEAP), and hopefully obtain purchase orders to add insulation to all the uninsulated surfaces. Either way, facility owners and operators will benefit by making certain that all heated and cooled surfaces are properly insulated and that new facilities are insulated to economic thicknesses at construction time. I believe that in a couple of years, with NG prices sustained around $5 per MMBtu, the mechanical insulation market can expand at least by $1 billion dollars per year due to the desire by facility owners and operators to save energy and hence reduce the costs of that energy. However, this will only happen if the mechanical insulation industry adequately promotes the thermal benefits of insulation. So, if you haven’t yet taken NIA’s IEAP class and become a Certified Energy Appraiser, now is the time to sign up. Don’t wait. (Visit www.insulation.org for details.)
Power Plant Construction
Increases in the cost of NG will significantly increase the operating costs of NG turbine electric generating stations and at some point make them unattractive for utilities to operate as base load generators. Most large utilities already have a mix of electricity sources. These are primarily coal, nuclear, fuel oil, NG, and hydro (there are some new wind farms under construction but so far, wind as a source of electricity generation is a negligibly small source). For a utility with these different types of plants, with excess capacity most of time, and with high NG prices, they will probably use their nuclear, coal, and hydro plants for base load generators until the electricity demand requires additional power. At that point, they will use their NG turbines as a last resort, as peaking units. Consequently, an energy-consulting firm recently forecast that only 10,000 to 15,000 megawatts of NG-fired power generation will be added in 2004, an 81 percent drop from the 70,000 megawatts that entered service in 2002.
When new base load generating capacity is needed, the utility executives who make the decisions will consider the expected future costs of NG, coal, fuel oil, and nuclear fuel. They will then perform complex Return on Investment (ROI) calculations to evaluate whether to construct inexpensive NG turbine units, that will be expensive to operate, or high first cost nuclear and coal units that will be less expensive to operate due to cheaper fuels. NG prices, if they stay at least in the $5/MMBtu range, will strongly favor coal and nuclear in those ROI calculations when different new construction options are evaluated. For new capacity, then, nuclear and coal fueled plants should become more favorable, even with their higher initial investment costs, as was the case more than 20 years ago.
From 1981 through 2002, the production costs for coal and nuclear have steadily decreased to about $0.0171 per kWh for nuclear and $0.0185 per kWh for coal, both very low numbers. NG production costs have been on a "roller coaster ride." Last year they were $0.0406 per kWh, almost 2-1/2 times greater than the production costs for nuclear. Oil has a slightly higher production cost, of $0.041 per kWh.
a. Insulating Coal-fired Units
New coal-fired steam electric plants require abundant thermal insulation. First there are the boilers and main steam and feedwater piping that must be insulated, along with a lot of other piping. In addition, there are the Air Quality Control Systems consisting of very large, extensive ducts for the bag houses or electrostatic precipitators to remove fly ash, Selective Catalytic Reducers (SCRs) to remove nitrogen oxides, and chemical scrubbers to remove sulfur oxides. I was informed by an experienced estimator that a new, 1,500-megawatt coal-fired generating station will require about $24 to $40 million worth of insulation, representing about 35 percent for materials and 65 percent for labor to install. This works out to $15 to $25/kW of insulation (by contrast, the insulation opportunity for a NG fired turbine generator plant is only about $4/kW). While this value for the coal-fired units is only 1 to 2 percent of the total construction cost, it would represent significant opportunity for the mechanical insulation industry. For example, if U.S. utilities construct 50,000 megawatts of new plant capacity per year as coal-fired units (not an unreasonable number considering the more than 200,000 megawatts of NG generators added in the past 4-1/2 years), that would represent an insulation opportunity in the range of $750 million to $1.25 billion per year. With the increasing cost of operating NG-fueled generating stations, this is entirely plausible within several years.
b. Insulating Nuclear Power Plants
A nuclear power plant is very different since it doesn’t combust a fossil fuel and hence doesn’t have stack emissions that need to be addressed. Three utilities (Exelon, Entergy, and Dominion) have recently told the Nuclear Regulatory Commission of their intent to apply for licenses to construct new-nuclear-generating units at existing nuclear plant sites. However, no American utility has yet made the decision to do this. Regardless, there is widespread belief among people in the utility industry that a "nuclear renaissance" is in the future in the U.S. And, I, for one, believe that the U.S. is on the edge of a "nuclear renaissance." This is because of the successful operating experience of most operating nuclear plants and because of high, structural NG prices in North America and high world crude oil prices.
Of course, nuclear plants also require significant quantities of thermal insulation. A nuclear generating unit has the Nuclear Steam Supply System (NSSS), mostly inside the nuclear containment, consisting of some very large piping and large equipment. This requires a pre-engineered, pre-fabricated, removable/reusable insulation system supplied under a nuclear quality program. Outside of the containment, there’s a large quantity of main steam and feedwater piping, and miscellaneous other piping and equipment, to insulate with conventional insulation and removable blankets, as well as the turbines to be insulated with removable blankets. With assistance from an experience estimator, I estimated the total insulation opportunity (material and labor) at a new, 2-unit, 2,000-megawatt Westinghouse Advance Pressurized Water Reactor to be worth a total of $25 million to $30 million, breaking down to about 63 percent for materials and 37 percent for labor to install.
This opportunity represents a range of $12.5 to $15 per kilowatt of generating capacity of mechanical insulation.
While no new nuclear units have been approved for construction in the United States in more than a quarter of a century, high sustained NG prices for utilities of about $5/MMBtu will eventually spur the construction of new nuclear units. The Bush Administration has stated that it has a goal of getting several new units into construction by the end of the decade. If we assume four new 2-unit plants per year starting in 2007, then that could represent an insulation opportunity of $100 million to $120 million per year in 2003 dollars. This isn’t huge amount for a $7 billion per year mechanical insulation industry, but it’s a start. With time and with greater nuclear plant construction, say in 10 years, it could grow to be significant.
Liquefied Natural Gas (LNG)
The fundamental change in supply and demand for NG in the U.S. hasn’t gone unnoticed by the large energy companies. The four U.S. Liquefied Natural Gas (LNG) receiving terminals, constructed in the 1970s and later mothballed, are now all in back in service. In addition, all are adding capacity. Furthermore, numerous other new LNG receiving terminals are at various stages of approval process. These existing terminals, after expansion in 2005, will have a combined storage capacity of 28.75 billion cubic feet (bcf) and a combined "sendout capacity" of 4.9 bcf per day, enough to supply about 4 percent of the total domestic NG demand. There’s a detailed report in the June 23, 2003 issue of Oil and Gas Journal (OGJ) titled, "LNG poised to consolidate its place in global gas trade," by Colleen Taylor Sen, which gives these, and many other, numbers on LNG.
What’s more noteworthy, however, is that the pending (based on active applications for permits) total projected U.S. terminal capacity expansion is in the range of 71 to 80 bcf. This planned construction is based on a projected price for NG exceeding $3 per MMBtu, the approximate trade-off point in the NG price for the viability of LNG according to the OGJ article.
The best part of these new LNG receiving terminals is that all will need lots of mechanical insulation. So what gets insulated on a LNG-receiving terminal? Keep in mind that these terminals are receiving LNG at cryogenic temperatures, below minus 260 degrees F, and this requires considerable thickness to prevent frost formation on the surfaces. The tanks are typically insulated with a large amount of expanded perlite, amounting to about $500,000 of perlite material per tank, poured into an annular space of a stainless steel, double walled tank, with about $500,000 of craft labor per tank (see drawing at bottom left on page 22). Typically, there are two to three tanks per LNG receiving terminal, which can store about 5.5 to 6.0 bcf of NG (these volumes are in terms of the LNG as usable NG, not as a liquid). Then, there’s lots of piping, which typically gets insulated with a cellular insulation, either cellular glass or polyurethane covered with an extremely durable, vapor resistant rubber jacketing. That piping insulation may represent $3 million to $4 million of insulation material and labor per two to three tank terminal, depending on the distance between the tanks and the off loading terminal. With assistance from an expert in insulating LNG facilities, I predicted that the tanks’ insulation and the piping insulation add up to approximately $10 million of insulation opportunity per new LNG receiving terminal. That, in turn, works out to about $1.75 million per bcf of NG storage capacity.
Chicago Bridge & Iron’s Web page describes the tank insulation:
"Sidewall insulation is provided by perlite expanded and installed under CB&I specifications. Perlite is an inorganic, nonflammable, lightweight insulation produced from special volcanic rocks. The volcanic rock or ore is finely ground and then expanded in furnaces operating at about 2,100 degrees F. The perlite is normally expanded in a field operated furnace and placed in the insulation space while still hot. This method minimizes moisture in the insulation. It also minimizes breakdown of the perlite particles, since they are handled only once after expansion. The welded steel plate outer shell provides both containment and vapor protection for the perlite insulation.
The insulation closure is a lap welded steel plate between the inner tank roof and the outer shell. The outer shell is entirely butt welded together and fillet welded to the outer steel bottom. The outer lap welded tank bottom furnishes a positive bottom seal for the shell insulation and a positive vapor barrier for the load-bearing bottom insulation."
Based on existing applications for construction permits, I then estimated that there’s an upcoming insulation market potential (M&L) of $125MM to $140MM in North America for new LNG receiving terminals. Although not known for sure, it’s reasonable to assume that after approval, these will come on line between 2005 and 2009, a five year span. Based on these values, then the mechanical insulation industry could see an opportunity in the range of $25 MM and $28 MM per year in those five years. Again, while not really a huge opportunity, there’s certain to be much more to follow since the demand for NG in North America has exceeded supply and that gap, between supply and demand, be made up by imported LNG. To accept LNG, there must be LNG receiving terminals.
Incidentally, there are huge NG-reserves in Russia and several countries in the Middle East. Worldwide, there is plenty of supply. The U.S. simply needs to get it here. To do so, we will need many new LNG-receiving terminals.
Increased Costs of Manufacturing Insulation
The flip side of the increased demand for thermal insulation, caused by higher NG prices is that some types of insulation will cost more to manufacture. This is because some types are energy intensive to manufacture and some even require petrochemical feedstock.
For example, there was an industry survey conducted in the 1994-98 period of fibrous glass wool manufacturing. This survey concluded that of all the energy used, 72 percent was from electricity energy use (at the electric power plants), 25 percent from NG, and 3 percent from other fuels. If we assume a 25 percent conversion and transmission efficiency for the electricity and 80 percent combustion efficiency for the NG, the amount of energy used at the plant from each type is about equal. If I assume that the energy cost used to manufacture each pound of fibrous glass wool in that time period was $0.12, then an increase in the NG price of 57 percent and an increase in the electrical energy cost of 15 percent would increase the energy cost of making the fibrous glass wool by 1/3, to about $0.16 per pound. Over time, this may increase the sale prices of fibrous glass wool for manufacturers.
To the best that I can determine, organic cellular insulation materials, such as polystyrene, phenolic foam, and polyisocyanurate use petrochemical feedstocks. None use NG as the chemical feedstock. However, as NG prices increase, the price of crude oil follows, and vice versa, since the costs of different fuels affect one another (as shown earlier in this article). Hence, the long-term affect will be to increase the manufacturing costs of organic cellular insulation materials as well.
What Can We Do Now?
As people representing the mechanical insulation industry or as people who are responsible for energy use at an industrial facility, you should be preparing for a new era of high NG prices and of high-energy prices in general. Everyone reading this article should become a Certified Energy Appraiser, per NIA’s IEAP, if you have not already done it, so you can intelligently help customers or others at your industrial facility determine optimum insulation thicknesses. You should also be conversant in the language of costs of energy and energy conservation. In short, you should be an energy conservation expert.
For those in the mechanical insulation industry, you should be knowledgeable about the insulation requirements at a new, coal-fired electric generating station with a state of the art Air Quality Control System. I would recommend that you become knowledgeable about insulating LNG tanks and cryogenic piping so you are prepared for the emerging LNG receiving terminal opportunity. Finally, if you are an insulation manufacturer and use NG for process heat, I would recommend that you study your process carefully to determine if there are steps you can take to make your process more energy efficient.
For those prepared for the future, the future is yours.
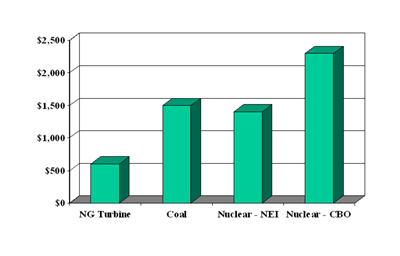
Estimated construction costs in dollars per kilowatt of generating capacity for NG-fired turbine generators, coal-fired generators, nuclear plants (per the Nuclear Energy Institute) and nuclear plants per the Congressional Budget Office predictions.
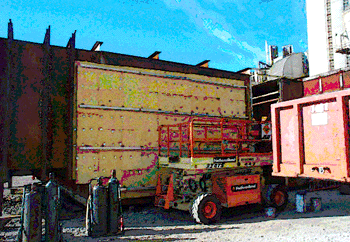
Extensive duct work such as this on Selective Catalytic Reducers, used to take out polluting nitrogen oxide gasses, needs to be thermally insulated.

Huge fans such as this one at SCR also need to be thermally insulated. This example has been insulated and is ready for operation.

Steam generators and main steam piping at a Westinghouse Pressurized Water Reactor, constructed in the early 1980s, are insulated with pre-engineered, pre-fabricated removable/reusable thermal insulation system, including stainless steel lagging. New nuclear plant construction would offer significant opportunity to the mechanical insulation industry.