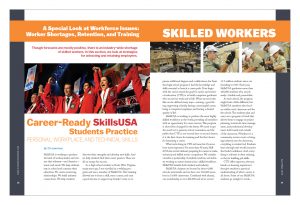
Career-Ready SkillsUSA Students Practice Personal, Workplace, and Technical Skills
By Tim Lawrence
SkillsUSA is working to produce the kind of worker, leader, and citizen that industry—and America—wants and needs. We help students stay in school and continue their education. We create mentoring relationships. We build industry connections. We help students discover their strengths and develop new skills. And we help students find their career passion. These are all on-ramps for success.
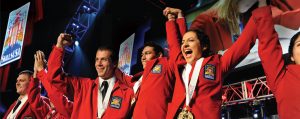
As a high school student in Rock, West Virginia, many years ago, I was enrolled in a welding program and was a member of SkillsUSA. That training allowed me to learn a skill, start a career, and earn a good income to support my family. I went on to pursue additional degrees and certifications, but from that high school program I had the knowledge and skills essential to launch a career path. If we begin with the end in mind, the goal for career and technical education (CTE) is to build competent graduates who succeed at work and at life. What success looks like can be defined many ways—earning a good living, supporting a family, having a meaningful career, being a competent employee, and having a desired quality of life.
SkillsUSA is working to produce the most highly skilled workforce in the world, providing all members with an opportunity for career success. This program is about lives changed for the better. We need to get the word out to parents, school counselors, and the public that CTE is not second class or second chance; it is the first choice for training and the first choice for launching a career.
What we’re doing in CTE isn’t new, but it’s never been more important. For more than 50 years, SkillsUSA has served students preparing for careers in trade, technical, and skilled service occupations. We consider ourselves a partnership of students, teachers, and industry working to ensure America has a skilled workforce. SkillsUSA benefits both students and industry.
SkillsUSA chapters are located in about 4,000 schools nationwide and we have over 360,000 members in 19,000 classrooms. Combined with alumni, our membership is over 400,000 and we’ve served 13.5 million students since our founding in 1965. Each year, SkillsUSA graduates more than 100,000 students who are job ready—hirable and promotable.
At each school, the program might look a little different, but SkillsUSA members elect leaders within each classroom and for the school. The students plan and carry out a program of work that allows them to engage in project planning, teamwork, time management, and professional development, both inside and outside of the classroom. Whether it’s a community service event or bringing industry into the classroom, everything is student led. Students learn through real-world scenarios that build confidence. And, everything is relevant to their training, so they’re building job skills.
CTE offers rigorous, relevant, hands-on learning experiences that give students a practical understanding of what a career is all about. Some of our SkillsUSA students go straight to work—but many more continue to higher education. CTE students have more options than ever to continue studies or to start applying the skills they’ve already learned. Dual enrollment programs, industry certifications, and technical degrees all create on-ramps to higher education or employment. Others seek an apprenticeship or join the military—any of these are viable paths to a career. The question most people ask is how does SkillsUSA benefit both students and industry?
More than 600 companies partner with SkillsUSA nationally, and thousands more at the state and local levels. Industry is involved in everything we do, from serving on local school advisory councils to helping us plan and run state and national contests. This partnership between education and industry informs curriculum to maintain current technology, standards, materials, and training. This ensures graduates have the skills that align with industry needs. Companies can support local schools and recruit employees, mentor students, and work directly with teachers in the field ensuring that ongoing pipeline of future employees. This involvement fosters strong relationships.
Many industry partners know career and technical student organizations (CTSOs) through competitions. As the state competition season begins in February and leads to our national SkillsUSA Championships in June, industry across the nation will step up to evaluate our students’ skills in 10,000 competitions at the local, regional, state, and national levels. SkillsUSA offers 103 hands-on contests in manufacturing, machining, robotics, engineering, automotive service, cybersecurity, construction, welding, graphic design, cosmetology, and health care—and leadership events like public speaking, entrepreneurship, or community service.
These contests are exciting for students and provide the opportunity to work against the clock against other students who are the best of the best. They offer recognition, scholarships, tools, and industry prizes. At the national event, more than 1,000 gold, silver, and bronze medallions are awarded, along with hundreds of scholarships. Total industry contributions of donated time, equipment, or materials is more than $36 million. Encompassing 25 acres, the national contest floor is highly visual. More than 18,000 students, teachers, and education leaders attend our championships. Each competitor is a state first-place winner.
The SkillsUSA Difference: The Framework
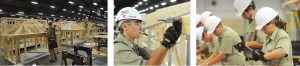
The contests are exciting, but learning takes place in every classroom—even for students who never compete. In SkillsUSA, much of our student preparation takes place through the SkillsUSA Framework. Integral to instruction, the Framework looks like a triangle and is our organization’s way to illustrate exactly how SkillsUSA students become world- class workers.
Framework components include 17 essential career-readiness skills. There are personal skills like work ethic, professionalism, and self-motivation. There are workplace skills like teamwork, communication, and decision making. And there are technical skills grounded in academics like job-specific skills, computer literacy, and safety. The framework was implemented to help more students learn a consistent skill set, but also to give students common language to use when they talk to employers about what they’ve learned and can do.
In classrooms across the country, students practice these career-readiness skills using our SkillsUSA Career Essentials suite. This program was created as an online solution to produce career-ready graduates. And finally, SkillsUSA has technical assessments to help CTE teachers measure what students know and can do in 41 occupations. SkillsUSA and its industry partners have invested in Career Essentials and our assessments to teach and measure skills in a way that’s easy to implement and engaging for students.
The Skills Gap Is Real
In my role as Executive Director, I travel the country to visit local schools and meet with industry partners. From training and education managers to CEOs, I hear the same thing over and over. The skills gap is real.
Construction, engineering, maintenance, repair, and customer-service sectors face worker shortages. Baby Boomers are retiring at a rate of 10,000 a day. Over the next decade, 3.4 million new manufacturing jobs will be available. Of those jobs, 2 million may go unfilled because of the lack of qualified workers.
The good news is that CTE is working to produce the kind of worker, leader, and citizen that industry—and America—wants and needs. The high school graduation rate for students concentrating in CTE is 93%, compared to a national average freshman graduation rate of 80%. CTE students are also more likely to continue on to higher education—91% of high school graduates who earned 2 to 3 CTE credits later enrolled in college. CTE students are more likely—through hands-on learning—to develop problem-solving, project management, research, math, communication, time management, and critical thinking skills.
The SkillsUSA Championships will be held in June 24–28 in Louisville, Kentucky, and everyone is welcome to come see firsthand what’s working in America’s public CTE. The future has never been brighter for career and technical education. For more information, go to www.skillsusa.org.
SkillsUSA and Construction Trades
Last school year, SkillsUSA had 61,677 members in the construction occupational cluster in high schools and colleges. According to the Bureau of Labor Statistics, employment in the construction industry is projected to grow about 12% through 2026, faster than the average for all occupations. Employment of construction workers is especially sensitive to the fluctuations of the economy, and demand for labor mirrors the overall level of construction activity.Repairing and replacing the nation’s infrastructure— including roads, bridges, and water lines—will result in steady demand for laborers, a demand also driven by the construction of homes, schools, office buildings, factories, and power plants. Because of the large size of the combined construction occupations, job prospects are favorable in this sector. NIA contractors, distributors, fabricators, and manufacturers who seek employees should be aware of career and technical education and SkillsUSA’s efforts as a talent pipeline and skills gap solution. To connect with your state’s SkillsUSA association, go to: www.skillsusa.org/about/state-directors/.
Tim Lawrence is the Executive Director of SkillsUSA (www.skillsusa.org), a national nonprofit education association that partners with industry to ensure America has a skilled workforce. Located in 4,000 schools nationwide, SkillsUSA members are trained with essential career skills and provided competition opportunities in local, state, and national competitive events. He can reached at tlawrence@skillsusa.org.
UpSkill Houston
An Industry-let collaboration building Houston’s talent pipeline
By Peter Beard
The Greater Houston Partnership is the region’s premier business association that works to make Houston one of the world’s best places to live, work, and build a business. In 2014, the Partnership created the UpSkill Houston initiative to focus on addressing Houston’s skills gap—where people lack the skills and education they need for the careers our region’s industries offer—and the people gap—where Houston’s employers cannot find the skilled workers they need when and where they need them. UpSkill Houston focuses on the more than 1.4 million careers and occupations in key industry sectors, including commercial and industrial construction, that require education and skills beyond high school and less than a 4-year college degree.
In Houston, the skills and people gap is acute for construction craft professions. The demand for skilled industrial construction workers in key crafts is projected to significantly exceed the supply of workers in the region between 2018 and 2022.
During the 2018–2022 period, the regional supply of industrial craft workers is estimated to be about 15,000 workers with a projected demand of between 25,000 and 30,000 industrial craft workers. Some of the high-demand industrial crafts include: pipefitting, welding, electrical, instrumentation, millwright, and crane and rigging. During this same period, the projected supply of insulation craft workers is approximately 800 with a range of projected demand between 1,900 and 5,000.
Since 2014, UpSkill Houston has focused on the following approaches and applied learnings to address our region’s workforce challenges:
- Business Leadership: UpSkill Houston invites business executives and employers to lead the way and create an industry table that focuses on collectively building a strong talent pipeline for critical careers in the industry.
- Collective Action: We also create a collective table that brings business and industry leaders, educators, community organization representatives, and government officials together to create a common language that allows everyone to focus on a common problem, establish a common goal, align their efforts, pursue separate tactics, and share results.
- Career Awareness: As a country, we can declare success in that we have persuaded almost everyone—students, parents, and others—that a 4-year college degree is the only pathway to success. We need to find new ways to inspire students to consider great careers that require education and skills beyond a high school diploma and less than a 4-year college degree.
Business Leadership: UpSkill Houston’s success hinges on employers assuming leadership and responsibility for building a strong talent pipeline for their industry. In construction, we work closely with business leaders from Associated Builders and Contractors, Associated General Contractors, and key construction leaders.
- Construction Career Collaborative: UpSkill Houston has worked with Houston’s Construction Career Collaborative (C3) to convene hospital and educational institutions, as building owners, to understand how their procurement policies can create a favorable environment for building a more sustainable construction craft workforce.
- PetrochemWorks Steering Team: Petrochemical plant managers and industrial construction executives are working on a number of different critical workforce issues, including developing common competency maps, linked with performance verification, to help create more consistent skills development of the industrial craft workforce.
Collective Action: Though UpSkill Houston is employer-driven, educational institutions and community organizations play crucial roles in its collaborative efforts. A collective table breaks down barriers and fosters a broad dialogue that brings all sectors of Houston’s economy together to create a singular vision and powerful solutions to expand the talent pipeline to the benefit of citizens and industries across the region. This approach has reinforced existing efforts, while spurring new coalitions, and it’s working in not just one area, but in multiple industries that are coming together.
- S&B Engineers and Constructors “Women in Construction” Program: S&B partnered with United Way of Greater Houston to implement a “Women in Construction” program that recruited women into and provided support for a “hire and then learn” pipefitter helper program. This program has helped to increase the diversity of the craft workforce.
- Trio Electric Pre-apprentice Program: Trio Electric partnered with Spring Branch independent school district to develop and conduct an innovative program that educates and develops the skills of junior and seniors in high school to become commercial electricians. Students in the program receive a paid summer internship between their junior and senior years and are guaranteed employment when they graduate and complete the program of study.
- SER Jobs for Progress and Gutier Roofing/Marek Bros.: SER partnered with Gutier and Marek to create an innovative approach that develops opportunity for youths and young adults in the Houston area for careers in commercial roofing and drywall. The approach features basic and on-the-job training in roofing and drywall.
Career Awareness
When we ask young people what they want to be when they grow up, the answers generally include doctor, professional athlete, musician, actress, etc. These are careers that we see every day in movies, TV, and real life. Rarely do we hear answers like an insulation installer, process operator, medical coder, or automotive technician. The reasons for this likely come down to one of several factors: a lack of awareness of available careers, negative perceptions of careers in some industries like construction or energy, and society’s long-held belief that the only pathway to success is a 4-year college degree.
- UpSkill Houston launched its What are you up for campaign? to tackle the awareness and perception challenges for “middle skill” careers. Through the “My Life As” career video series, UpSkill Houston is working with our school districts to help inspire students and their parents to consider the great careers in our region that don’t require a 4-year college degree. The videos have featured 4 craft professionals telling their stories and the paths they took for the great careers they have. You can view the video at www.UpSkillMyLife.org.
UpSkill Houston unites these powerful forces—industry, education, community, and government—and works to create the talent pipeline Greater Houston’s regional economy requires while helping individuals build careers that improve their lives.
The approaches described in this article could be used by a collaborative of insulation contractors. The first step would be to create a collective table of industry leaders committed to building the pipeline of talent for the insulation specialty. Next, the collaborative of employers would develop a shared understanding of the supply of and demand for craft professionals and agree on the skills and credentials that are needed for workers to be successful in the insulation craft. Because craft workers generally develop their skills over time, the collaborative would also need to map the skills progression for a worker. With this information, the members of the employer collaborative would then partner with educational institutions and community organizations that can develop the talent. The partnership would need to explore how to attract and screen potential workers, what it takes to develop the skills and the talent, and how to onboard talent with the employers. As with any new approach, the partners need to commit time and effort in order to develop an effective talent pipeline.
Peter Beard serves as Senior Vice President for Regional Workforce Development at the Greater Houston Partnership, whose mission is to make the Houston region the best place to live, work, and build a business. He leads the Partnership’s UpSkill Houston initiative—a business-led effort that works with employers, educational institutions, community-based organizations, and the public workforce system (www.houston.org/upskillhouston). UpSkill Houston works to ensure that the region’s businesses have access to workers that have skills and credentials for advanced and technical careers and occupations that require education beyond a high school diploma but less than a 4-year college degree. He can be reached at pbeard@houston.org.
Cultivating the Next Generation of E&C Technical Talent
By Priya Kapila
With information system innovation at an all-time high, the engineering and construction (E&C) industry is experiencing dramatic changes right now. New technological advancements, combined with demographic shifts in the workforce and owners’ demands for cheaper, faster, and better projects, are resulting in heightened pressure for E&C companies to continuously improve and advance.
Augmented reality, 3D printing and scanning, building information modeling (BIM), virtual design and construction (VDC), prefabrication, and even unmanned drones are helping E&C companies work smarter, boost productivity, and improve collaboration across project teams. But these innovations also pose challenges, particularly when it comes to finding, developing, and retaining the right talent.
In this article, we explore the impact of technological influences on today’s E&C labor practices, discuss what new skills and competencies will be required in the near term, and provide recommendations on how to develop a workforce of the future.
The Merging of Design and Construction
Over the past decade, we have witnessed a significant increase in firms adopting BIM/VDC systems in all aspects of the design-build process. This includes modeling, customer decision mapping, estimating, virtual building, prefabrication, site analysis and coordination, construction resource utilization, and field work planning, among others.
With the growing use of enhanced BIM/VDC systems comes the demand for specialists to employ these tools effectively. In one extreme example of how BIM/VDC usage is impacting the industry, we can look to Broad Sustainable Building, a Chinese construction firm that last year brought new meaning to fast-build projects by completing a 57-story skyscraper in Changsha in just 19 days. While this prefabrication feat was as much for notoriety as it was to meet housing demands in south central China, the project highlights the current prevailing expectations for efficient design-build engagements, which will rely heavily on effective BIM/VDC tools and a technically proficient workforce.
Early adopters of BIM/VDC processes now have a performance record that proves the operational gains that may be realized using innovative modeling and virtual planning systems. Mortensen Construction, for example, analyzed 18 projects completed between 2004 and 2014 and identified the following benefits resulting from their VDC process:
- Average schedule reduction: 32 days
- Productivity increases: 25% and greater
- Average direct cost reduction: 2.95%
As the positive impacts of BIM/VDC are noted across the entire E&C industry, it’s clear that such innovations are revolutionizing project delivery. Some of the key areas of innovation include:
- Prefabrication: With the ability to better plan and model construction projects, E&C companies anticipate the expansion of prefabrication work, which has the potential to significantly reduce project timelines.
- Automation: Where possible, firms are seeking to implement automation processes already highly utilized within the manufacturing industry. This is critically significant from a safety standpoint, as the use of robotics could limit the exposure of workers to site safety hazards.
- Virtual Collaboration: The ability to liaise in real time with customers and other project stakeholders using mobile devices and related technologies is increasingly cited as advantageous to project design and decision making, particularly for health-care clients.
Technical Talent Wanted
Naturally, the expanding utility of BIM/VDC tools has driven the need for specialists that can effectively apply these systems. FMI Compensation has collected staffing and salary data from E&C companies for BIM professional jobs since 2009. Our longitudinal analysis reveals several key observations:
- Growth of the Profession
The number of companies that report having a BIM professional on staff has increased significantly over the last 2 years. In “FMI’s 2016 Construction Professional Compensation Survey,” we noted an increase of 68% in companies identifying at least one BIM professional within their workforces. Our survey findings also indicate the greatest growth of incumbents at the senior BIM professional level—a trend we expect to see continuing in the coming years. However, our research also shows a slight decline in entry-level BIM specialists, which seems out of line with the overall trajectory of BIM/VDC adoption and deployment. There could be several explanations for this observation, including:
• Demand for experienced BIM/VDC professionals is overwhelming and leaves little motivation for newcomers to enter the field.• The economic downturn led to layoffs and hiring freezes that stifled the recruiting of beginner BIM/VDC professionals.
• Training efforts, as well as employer expectations for rapid skills development for BIM/VDC specialists, are great, so employees are improving their knowledge and skills quickly and, therefore, moving beyond “beginner” status to higher steps on the career ladder in short order.
- Increases in BIM/VDC Staffing
FMI’s survey data suggests that companies are hiring more BIM/VDC professionals. In 2014, E&C firms participating in the “Construction Professional Compensation Survey” indicated that, on average, they employed slightly fewer than 4 individuals in BIM/VDC professional positions. In 2016, the average staff count rose to nearly 5 BIM/VDC employees. The largest staff increases involved higher-level roles, suggesting the increasing need among E&C firms for highly skilled professionals who can facilitate coordination and collaboration among multiple stakeholder groups on complex projects.
- Gradual Salary Increases
For the past 15 years, FMI’s Compensation Group has been tracking 6 key benchmark job families, including business development, project management, project superintendent, estimator, general foreman, and BIM (the latter has been tracked since 2009). Exhibit 1 shows the base pay trend for each job family and reveals that, in general, pay levels have been increasing since 2001. Although employment levels may have receded during the recession, those jobs requiring specialized skills and knowledge have experienced steady pay increases.Table 1 shows how national median salaries for less experienced roles (i.e., Levels 1 and 2) have grown little or declined since 2009, while salaries for more advanced roles (i.e., Levels 3 and 4) have increased.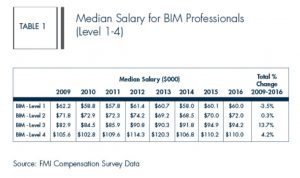
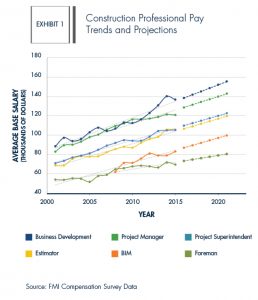
- With the decrease in beginner BIM/VDC professionals relative to more experienced incumbents, the median salary levels reported are no surprise. As such, there is little pressure to increase wages for entry-level roles, given the lack of growth at this level, while the focus on higher-level roles is driving salary increases. That said, apart from the “BIM—Level 3” position, the rise in BIM salaries since 2009 is lower compared to general E&C industry compensation increases. It remains to be seen whether continued demand for BIM/VDC specialists will ultimately result in larger pay increases in the near future.
Developing an Effective Talent Development Approach
As BIM/VDC systems continue to evolve, so too will the roles of individuals responsible for using them. Thus, E&C companies must remain cognizant of not only how they are using BIM/VDC for projects, but also how best to utilize staff and effectively hire, develop, and retain these increasingly critical employees. Here are our top recommendations for companies that want to fully leverage technological developments while maximizing their current and future workforces:
- Conduct Periodic Needs Assessments
To ensure the right people are in the right roles, start by assessing current BIM/VDC practices as well as forecasting process updates. Then compare existing employees’ skills and competencies relative to workforce needs, given current and future practices. Knowledge of the work to be performed will be essential in determining the incumbent qualities needed to perform BIM/VDC functions.
- Understand the Roles That Need to Be Filled
Today, BIM/VDC professionals take on a broad spectrum of roles, including:
• Technician Versus Facilitator. The technical BIM/VDC role is a traditional position that grew out of earlier design drafting roles. The technician role is responsible for administering systems and ensuring their effective and efficient operations. Alternatively, the facilitator role is responsible for project management and coordination related to BIM/VDC. While many firms distinguish between these 2 roles—namely because they tend to require different job competencies—we expect these roles to merge into one over time. This would require technical specialists to be well-versed in project coordination and bring greater efficiencies to projects through a primary, specialized point of contact.
• Expert Versus Cross-Training. Even while we observe growth in the number of BIM/VDC professionals, some firms want to train their existing workforces in BIM/VDC systems rather than staff subject matter experts. With the adoption of BIM/VDC integration, cross-training is a more plausible approach (versus when BIM/VDC is introduced and implemented in a short time frame). Deciding which job design approach to pursue will depend on the extent to which BIM/VDC systems are utilized on projects, who uses those systems and in what capacity, and how well various project team members learn BIM/VDC operations.
- Evaluate Recruitment Initiatives
E&C firms must determine how to staff the BIM/VDC function, given the results of a needs assessment. Desired job roles should be reflected in the firm’s recruitment strategies. For example, if a company finds that experts are preferred, it may need to provide a premium compensation package to effectively attract experienced talent. Based on the demands for talent and review of recruitment effectiveness, E&C firms may require outreach initiatives to expand the population of BIM/VDC professionals. This may be particularly true, given the diminished number of entry-level specialists.
- Sharpen Retention Efforts
As the labor market becomes constrained, companies that have successfully established high-functioning BIM/VDC teams will need to assess optimal staff retention approaches. Potential strategies may include:
• Professional Development. Given the targeted growth among experienced BIM specialists, it is mutually beneficial for employees to expand their skills and knowledge in BIM/VDC and for employers to invest in their employees’ long-term development. Career development offerings are also a key contributor to engagement among employees, according to FMI’s Industry Survey, “Millennials in Construction: Learning to Engage a New Workforce.” It is routinely recognized that engaged workers are more likely to remain with their employer long term.
• Career Tracks. Clearly defined advancement opportunities can help BIM/VDC professionals recognize their long-term employment possibilities. Many E&C firms began with just one BIM individual-contributor position, but today, many larger companies are building complete career paths that are similar to those in project management. For instance, one FMI compensation survey participant indicates that the following job descriptions have been drafted for BIM/VDC positions: specialist, engineer, manager, regional manager, and director.
What’s Next for BIM?
Looking ahead, we expect to see continued innovation across BIM/VDC systems where prefabrication, automation, and virtual collaboration will begin to take center stage as the industry’s use of technology expands and matures. To best leverage these trends, E&C companies must sharpen their talent management pencils in a way that ensures the recruitment and retention of the right level of technical talent. That talent must be able to leverage advanced technologies and work even smarter in 2017 and beyond. For this and other reasons, a competitive pay strategy serves as a cornerstone of any good human capital investment approach.
Priya Kapila is the Compensation Practice Leader with FMI Corporation (www.fminet.com). Reprinted with permission from FMI Corporation. Ms. Kapila is responsible for leading the compensation consulting practice of FMI Compensation.
Attracting and Growing Talent: What Contractors Need to Know
By Stacey Holsinger and Mark Drury
Across many industries in the United States, there is a decline in educated, skilled, and experienced personnel as the largest generation in history moves out of the workforce and into retirement. As a result, it’s become a war for talent, and construction companies are on the front line.
This comes at a critically important time for the construction industry as the current volume of work already exceeds the human capital resource capacity. Furthermore, between natural disasters, a growing economy, and a crumbling infrastructure, the demand for increasing the industry’s production capacity is at an all-time high.
Increasing Need for Employee Education and Training
In any industry, knowledge coupled with talent is the pathway to advancing a career. Now more than ever, offering a robust employee development program is key to attracting the right people for the right careers. Recruiting the best candidates is a good start. But if you don’t train or educate those top talents, it could have a disastrous impact on project delivery. Don’t let this become the type of employee who represents your company and destroys your brand on a daily basis. To put it bluntly, investing in your employees through education and training is an opportunity for success that today’s contractor simply cannot afford to ignore.
Companies are all desperate for candidates who have at least 5 to 10 years of construction experience to fill the gap created by the increasing number of workers in their 50s and 60s who are retiring from the industry. As a result, the construction job deficit is expected to increase to 2 million unfilled positions by 2022. This means those experienced candidates everyone is so desperate to hire do not exist, and construction firms will not be able to sustain their current capacity, much less realize their strategic growth goals.
To help solve this problem, construction companies must embrace the emerging Z Generation (recent high school graduates) as well as the tail end of the Millennial generation (those just graduating college). The huge benefit? Investing in their training and education to help them in their career goals and become contributors to success will be the key to helping a contractor achieve his strategic goal. A young professional who has the right attitude every day, is ambitious, has the aptitude to learn and develop skills, and is a hard worker will find a career with great wages, benefits, and many opportunities for success. As the workforce deficit increases, companies are offering more attractive benefits and perks that help define their company culture to attract young candidates.
Helping Current and Prospective Employees Choose the Right Construction Trade
Owners of construction firms have discovered that workers can develop skills that are transferrable and highly valued throughout the United States and all over the world. This is advantageous because every project is unique, locations vary, and project teams change. Moreover, construction appeals to those who take pride in being a part of a successful team accomplishing something tangible every day in a variety of interesting environments.
When exploring the various career paths in this field, you should encourage prospective employees to weigh the options based on their level of interest as well as earning potential. In terms of earning potential, the top trades are plumbing, electrical, and HVAC, all of which have state-level licensure requirements. Meanwhile, the most popular trade is carpentry.
In these licensed trades, the career path starts at apprentice, progresses to licensed journeyman (who can have one apprentice working under him or her), and culminates with a master’s license. Like the bar exam for lawyers or the medical boards for doctors, a journeyman needs that master’s license to realize his/her full income potential in the trade. With a master’s license, the tradesman or tradeswoman has the ability to start his or her own business in their respective trade.
Additionally, to further help workers choose the right trade, the Core Curriculum, which is a requirement in National Center for Construction Education and Research (NCCER) apprenticeship programs, serves as an introduction to the trades and provides some universal education and skills components as well as some exposure to all of the apprenticed trades.
Demonstrating the Worth of a Construction Career
To recruit top talent, Shapiro & Duncan is heightening awareness among prospective employees that jobs are in high demand, the skills learned are transferable, and that the company supports education and career development. As many contractors are aware, apprenticeships are like obtaining a 4-year degree without the cost. The trade-off is working full-time while going to school either a couple of evenings a week or 1 to 2 days a month, depending upon the program and employer. For many employees who know about this type of opportunity, this is an appealing blend of classroom instruction and on-the-job training.
Your prospective and current employees need to be educated on the fact that they can have mobility within the construction field—that it’s not a dead-end career. In reality, there is always opportunity to evolve and there is substantial room for growth in the field, no matter where your employee starts.
Field leadership team members are encouraged to push their teams to engage in education and training to ensure that they continually grow in their personal capabilities and contribution to the team effort. Also, the company’s monthly employee newsletter provides information on all education and training opportunities.
Merit and Union Shop Training Resources
Both union shops and merit shops provide training programs for construction workers. A requirement of apprenticeship is that the employer be the sponsor and pay the employee tuition. The most popular national training program is the one provided by the NCCER, which is affiliated with the University of Florida. Curricula include more than 70 craft areas and a complete series of more than 70 assessments offered in over 4,000 NCCER-accredited training and assessment locations across the United States. NCCER’s apprenticeship training modules are used in both high schools and technical schools.
Value of a Construction Internship and Apprenticeship Program
The company is a firm believer in the value of internship and apprenticeship programs.
Its summer internship rotation program is geared toward young people who are majoring in construction management or mechanical engineering. However, office internships, including marketing, accounting, IT, and human resources are also available. First year summer interns spend a week or more in several different departments, including preconstruction, engineering, fabrication, production, and project management, receiving a well-rounded exposure to the industry. Returning summer interns will be placed in a more consistent position based upon needs, interests, and talents for a more focused exposure to the S&D world. The year-round internships engage students in different departments on a part-time basis coordinated with their class schedules providing valuable work experience, a nice paycheck, and for many, additional academic credits.
The apprenticeship programs, meanwhile, currently have almost 70 participants with 29 being first-year apprentices. The program includes a mix of high-school graduates, young adults who have separated from the military, and adult career changers from other industries. All apprentices have journeyperson mentors to guide them through the program.
The company seeks apprentices and intern candidates with postings on the company’s website and on a variety of third-party employment websites. Additionally, the company as a whole supports and is actively involved in career and technology programs in the local school systems. Many team members regularly participate in career days and fairs as well.
The Next Level for Employee Development
Internship and apprenticeship programs are just the starting point for employee development. We’ve taken employee education and training to the next level by creating S&D YOUniversity.
This in-house educational program helps employees advance in their careers and earn more as they continue their career development. The company also offers tuition reimbursement (up to $5,250/year), for those pursuing associate’s, bachelor’s, and master’s degrees.
Key Takeaways for Construction Contractors
The sooner construction companies recognize the tremendous workforce potential of the Z and Millennial generations entering careers in the construction trades, the better it will be for the nation’s economy. Construction, literally and figuratively, builds economic opportunity. Just as a business invests in IT infrastructure, new equipment, or facility improvements, construction companies need to view education, training, and development as a strategic investment opportunity.
Owners of construction companies, meanwhile, can offer useful guidance to young people deciding on a career path. A key point to share is that by the time a young person would have graduated from college, they can be making as much or more as a 4-year degree holder—without the overwhelming burden of student debt. But prospective employees also need to know that success in the construction trades demands investing in oneself through continuing education and training.
We consciously provide career development opportunities that provide the impetus for new employees to find the right career path. Are you making the investment in the people who are working for you? If not, you are missing an opportunity to create not only a better image for your company and for the industry at large—but also a healthier bottom line!
Stacey Holsinger is Marketing Manager and Mark Drury is VP of Business Development at Shapiro & Duncan, Inc., a third-generation family-owned mechanical contracting business serving customers in the Washington, DC, area since 1976. Reprinted with permission from Constructor, March/April 2018, a publication of the Associated General Contractors of America, www.constructormagazine.com.