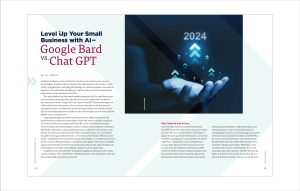
Artificial intelligence (AI) is a field of computer science that focuses on creating intelligent machines that can think and act like humans. AI is used in a wide variety of applications, including self-driving cars, virtual assistants, and medical diagnosis. AI is still under development, but it has the potential to revolutionize many aspects of our businesses and lives.
This article delves into the transformative potential of AI for small businesses in the insulation industry, with a specific focus on the comparative analysis of two advanced AI tools: Google Bard and OpenAI ChatGPT. These technologies are viable solutions for businesses in the mechanical insulation industry, presenting opportunities to revolutionize operational approaches and customer interactions, and visualize their future. Both are also user friendly and accessible, and are offered at no or minimal cost.
Large engineering and architecture firms have the ability to purchase and implement more expensive technologies, while mid-sized or smaller companies across the mechanical insulation industry often need to find ways to do more with less human and technological resources. Despite this, insulation contractors, distributors, fabricators, and manufacturers play a vital role in job creation, community development, and the pursuit of the American Dream. In an era defined by rapid technological advancements, access to tools that enhance efficiency and bolster competitiveness becomes paramount. AI emerges as a transformative force in this context, offering insulation contractors and suppliers the means to amplify impact and streamline operations by automating critical tasks and providing real-time insights, essentially replicating the output of a much larger team.
Google Bard and ChatGPT have both gained significant attention in the realm of AI (see sidebar, “How They Work”). While they share some similarities, there are also notable differences between the two.
Data Sources and Access
One of the key distinctions between Bard and ChatGPT lies in their data sources and access. Bard has real-time access to the internet, allowing it to supply the most up-to-date information. In contrast, ChatGPT’s training data—and, therefore, its knowledge level—is limited to sources available up to January 2022. Because it does not have access to current economic indicators or events, ChatGPT would not be the best tool to help you prepare your 2024 business plans, but it may help support the development and evaluation of plan scenarios by performing data analysis, creative generation, and communication, it can be a valuable partner in navigating the scenario and maximizing your success in the mechanical insulation market. ChatGPT Plus (or version 4), the paid version, can surf the web to find the latest info and double-check its facts, but it is limited to Bing search results. While this covers a considerable amount of information, it does not encompass the entire internet. ChatGPT Plus has its perks: It answers more quickly, you get first dibs on any new features launched, and you can tweak how it “talks” to suit your style. On top of that, you get expert help if needed, and third-party plugins that can add even more capabilities over basic ChatGPT.
Strengths and Weaknesses
Google Bard and ChatGPT are both powerful large language models (LLMs) with unique strengths and weaknesses (see Figure 1). Bard excels in providing comprehensive, informative, and conversational responses, while ChatGPT shines in generating creative text formats and summarizing information. The choice between the two depends on the specific needs and preferences of the user.
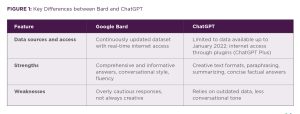
Bard stands out for its thorough answers to questions, drawn from its vast knowledge base and real-time internet access. It also demonstrates a higher level of fluency and conversational style in its responses. However, Bard can sometimes be overly cautious and hesitant, and it may not provide the most creative or engaging content.
ChatGPT, on the other hand, shines in its ability to generate creative text formats, such as poems, code, scripts, and musical pieces. It also exhibits a knack for paraphrasing and summarizing text, and it can provide more concise answers to factual questions. However, ChatGPT’s reliance on outdated data can limit its ability to supply the most accurate and relevant information. Additionally, its responses can sometimes be less conversational and more informational in tone. (Read “Mechanical Insulation Q&A with Artificial Intelligence (AI)” from the April 2023 issue of Insulation Outlook at http://tinyurl.com/mr3tfxb5.)
AI and LLMs have revolutionized the way businesses operate, providing innovative solutions and enhancing efficiency across industries. Small businesses have reaped significant benefits from the adoption of LLMs, leveraging these powerful tools to gain a competitive edge and achieve their business goals. Here are some practical applications for LLMs.
- Data-driven decision-making
- Effective communications and customer engagement
- Streamlined operations
- Market research and competitive analysis
- Training and skill development
As LLM technology continues to evolve, we can expect to see even more innovative applications that further empower small businesses to thrive in the competitive marketplace.
How to Use Each
Choosing between Google Bard and OpenAI ChatGPT for your business depends on your specific needs and requirements. Here is a breakdown of the key factors to consider and recommendations for evaluating and choosing between the two.
1. Consider your primary use cases.
Google Bard: Excels at providing comprehensive and informative answers to questions, drawing upon its vast knowledge base and real-time internet access. It is suitable for tasks like research, generating reports, and writing summaries.
ChatGPT: Shines in its ability to generate creative text formats. It is well-suited for tasks like creative writing, brainstorming ideas, and generating marketing materials.
2. Evaluate their strengths and weaknesses.
Google Bard: Strengths include comprehensive answers, conversational style, fluency. Weaknesses: Can be overly cautious, not always creative.
ChatGPT: Strengths include creative text formats, paraphrasing, summarizing, and concise factual answers. Weaknesses: Relies on outdated data, less conversational tone.
3. Assess their pricing and accessibility.
Google Bard: Free to use.
ChatGPT: Free version available with limited features; paid version (ChatGPT Plus) offers more features, including internet access and faster response times.
4. Conduct a trial or pilot test.
Use the tools to complete small tasks relevant to your specific business needs and evaluate their performance. With your unique knowledge of your business, such a test will probably reveal and inspire new ideas for their use.
5. Consider integration with existing systems.
Check if the LLM can integrate with your existing software tools, such as customer relationship management, marketing automation, or customer service platforms. Assess the ease of integration and the availability of technical support for the LLM.
6. Seek feedback from your team.
Get input from the team members who will be using the LLM on a regular basis. Understand their needs, preferences, and expectations to ensure the LLM selected is a good fit.
7. Stay informed about ongoing development.
Both Bard and ChatGPT are continuously evolving, so keep an eye out for new features and enhancements. New websites, apps, and services based on AI are being offered every day, so the resource you need might be available tomorrow.
The best way to choose between Google Bard and ChatGPT is to carefully consider your specific needs, evaluate the tools’ strengths and weaknesses, conduct a trial or pilot test, and seek feedback from your team. Remember, the LLM should serve as a tool to enhance your business operations, not as a replacement for human expertise and creativity.
How They Work
Google Bard and ChatGPT are examples of large language models (LLMs). LLMs are super-smart computer programs designed to excel with words: Think of them as language experts on steroids. These models use advanced networks to understand and generate human-like sentences on a massive scale. They learn patterns and connections in language, making them highly proficient in working with words.
LLMs undergo a two-step training process. First, they dive into massive amount of internet text, learning the rules of language and how words fit together. Then, they get specialized training for specific tasks, such as translating languages or understanding emotions in text. Once trained, they can be prompted with a question or statement, and they will generate intelligent and human-like responses.
These language wizards have achieved some impressive feats. They excel at understanding intent, whether it is a question or a sentence you want them to complete. They are proficient in language translation, creative writing, and coding assistance. Have you ever chatted with a bot that feels remarkably human? That could be one of these models at work. They are also adept at discerning the mood in a piece of writing and summarizing complex information, like business plans or medical notes. They are superheroes of technology, elevating computers’ ability to communicate and understand in ways we have never seen before.
Summary
In the rapidly evolving digital landscape, AI has emerged as a transformative force, reshaping the way businesses operate, innovate, and connect with their customers. Leading AI models like Google Bard and OpenAI’s ChatGPT exemplify the immense potential of AI to revolutionize diverse business applications, elevating operations to unprecedented levels of efficiency, enhancing customer experiences, and offering a decisive competitive edge.
AI’s ability to augment human capabilities, streamline processes, and unlock new frontiers of productivity underscores its importance for today’s businesses. Models like Bard—with its bidirectional learning (reads text both forwards and backwards for deeper understanding) enhancing context understanding—and ChatGPT—with its prowess in generating human-like responses—demonstrate the precision and conversational excellence that AI brings to the table.
To fully seize the opportunities presented by AI, businesses must embrace it as a catalyst for growth. By adopting this technology, small businesses can:
- Streamline operations and automate tasks, boosting productivity and reducing costs.
- Leverage AI for creative problem-solving, leading to innovative product or service offerings.
- Enhance customer interactions, understanding preferences and delivering personalized experiences.
- Stay ahead of the curve by adopting innovative AI technologies that align with their business goals.
The time to embrace AI is now. The future belongs to those who seize the transformative power of AI and harness it to drive excellence and growth.
DISCLAIMER: The author does not endorse or promote any of the tools mentioned in this article. The presentation of these technological advances and available options is for informational purposes only.
How Google Bard and ChatGPT Respond
Both Bard and ChatGPT were asked the same question and this is what each provided.
ChatGPT
Question One: What AI tools do you recommend for small contractors?
ChatGPT: Small contractors can benefit from various AI tools to streamline operations, improve efficiency, and enhance project management. Here are some AI tools that can be useful for small contractors:
- Procore: Procore is a construction project management software that utilizes AI to
automate tasks, streamline communication, and provide real-time project insights.
- Plangrid (Autodesk Construction Cloud): Plangrid, now part of Autodesk Construction Cloud, uses AI to help with document management, change order tracking, and collaboration on construction projects.
- Buildertrend: Buildertrend is a construction management software that incorporates AI to assist with project scheduling, customer management, and budget tracking.
- Rhumbix: Rhumbix uses AI and mobile technology for real-time field data collection,
helping contractors with timekeeping, productivity analysis, and labor tracking.
- SmartBid: SmartBid is a construction bid software that uses AI to streamline the bid management process, helping contractors find and manage project opportunities more efficiently.
- Raken: Raken is a construction field management software that uses AI to automate daily reporting, providing insights into project progress and helping with compliance.
- Deepomatic: Deepomatic offers AI solutions for visual inspections and monitoring on construction sites, helping with tasks such as quality control and safety compliance.
- BIM 360 (Autodesk Construction Cloud): Building Information Modeling (BIM) tools
like BIM 360 by Autodesk use AI to facilitate collaborative workflows and improve project coordination, reducing errors and delays.
- CognitiveScale: CognitiveScale provides AI solutions for various industries, including
construction. Their AI systems can help with predictive analytics, risk management, and decision support.
- HoloBuilder: HoloBuilder uses AI and 360-degree photo capture to create virtual construction documentation. It aids in project monitoring, collaboration, and progress tracking.
- Tenna: Tenna uses AI for asset tracking and management, helping construction companies keep tabs on equipment and optimize resource allocation.
- Sitemate: Sitemate uses AI to enhance project control and visibility, providing tools for project planning, task management, and document control.
Google Bard
The same question was given to Google Bard and it said it couldn’t recommend
anything without knowing more about the company’s specific needs.
Question One: What AI tools do you recommend for small contractors?
Google Bard: “Once I have a better understanding of your needs, I can suggest AI tools that can help you with tasks like:
- Project management: Tools like ClickUp and OpenSpace.ai use AI to automate
tasks, schedule projects, and track progress.
- Estimating and bidding: Kreo uses AI to quickly and accurately create takeoffs and estimates.
- Fieldwork and reporting: Fieldwire and PlanGrid use AI to streamline jobsite management, track progress, and generate reports.
- Marketing and sales: Canva and Copy.ai can help you create professional proposals, flyers, and social media content.
- Financial management: Tools like QuickBooks and Wave offer AI-powered features for invoicing, bill pay, and expense tracking.
I’m here to help you navigate the world of AI and find the tools that can take your contracting business to the next level. So, don’t hesitate to share more details about your needs, and I’ll be happy to provide personalized recommendations.”
Then the following input was given “We need help streamlining business management, tracking employee hours, avoiding safety issues, and improving the marketing of our services. We are a commercial and industrial insulation contractor with a small team of less than 10 workers.” Here is Google Bard response.
Google Bard: “Based on your specific needs as a small commercial and industrial insulation contractor, here are some AI tools that can help you streamline business management, track employee hours, avoid safety issues, and improve your marketing:
Streamlining Business Management:
- Project Management: Consider ClickUp or HoneyBook. These tools use AI to
automate tasks like scheduling projects, sending reminders, and tracking progress. They also offer features like client portals and invoicing, providing a central hub for managing your entire business.
- CRM: Look at HubSpot or Freshworks CRM. These tools use AI to help you manage your relationships with clients and leads, from capturing leads to closing deals. They can automate tasks like email marketing, lead scoring, and customer support.
Tracking Employee Hours:
- Time Tracking: Options like Toggl Track or Harvest use AI to automatically track employee hours based on computer activity or GPS location. This can help you ensure accurate payroll and identify areas where you can improve efficiency.
- Safety Management: Consider Smartwatch-based tools like Rise Vision or Bodysmart. These wearables can detect unsafe behavior like fatigue or drowsiness, helping you prevent accidents and keep your workers safe. They also offer insights into workplace conditions and worker fatigue, allowing you to identify and address potential safety hazards.
Improving Marketing:
- Social Media Marketing: Tools like Buffer or Hootsuite use AI to schedule and optimize your social media posts, helping you reach a wider audience and generate leads.
- Content Marketing: Try Grammarly or ShortlyAI. These tools can help you improve your writing and create high-quality content for your website or blog, attracting potential clients and showcasing your expertise.
Conclusion
AI is a powerful tool that can help you save time, improve efficiency, and make better decisions. But it’s important to choose the right tools for your specific needs and budget.